2018年,全球拖拉机市场掀起了一场高功率化的热潮。欧美和日本的几大拖拉机巨头纷纷推出了500马力、600马力甚至更高功率的产品,配备无极变速、动力换挡等先进技术,瞬间占据了市场的制高点。面对这样的国际形势,国内拖拉机制造商们也不甘落后,纷纷跟风生产大功率拖拉机,试图借此在市场中分得一杯羹。然而,当国内企业忙于马力的疯狂增长时,真正决定拖拉机竞争力的核心技术却被忽视了。为什么国产拖拉机的故障率居高不下?为什么看似强劲的大功率机型在田间地头频频「趴窝」?
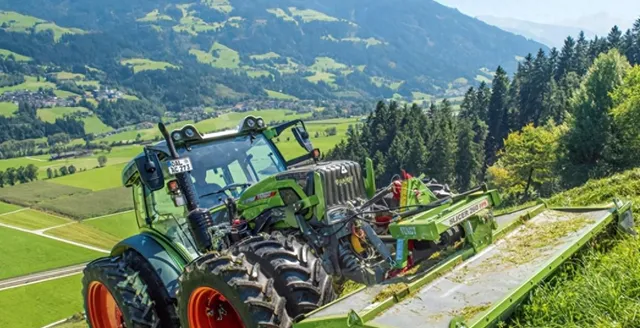
中国拖拉机产业的起步与成长
1959年,中国开始成批生产拖拉机,这标志着中国农业机械化的初步发展。在这之前,农业生产基本依靠人力和畜力,机械化程度极低,生产效率难以提升。新中国成立初期,为了摆脱落后的农业生产方式,中国政府开始大力推动农业机械化。那个时候,国内缺乏相关技术和设备,于是通过引进国外的先进技术和生产设备,尤其是从苏联等社会主义国家引进成套技术,这成为了早期中国拖拉机生产的主要路径。
最初引进的拖拉机型号多为苏联的「东方红」系列,这些拖拉机因其强劲的动力和坚固的设计,被广泛用于国内的农田作业。这一时期,工人们在工厂里忙碌地组装这些「舶来品」,从零件到整机的装配都严格按照外国的标准执行。然而,在实际使用过程中,这些拖拉机并非完全适应中国的农业环境。由于土壤条件、作业习惯的不同,外国产的拖拉机在一些作业环境下频频出现问题,这促使国内技术人员对这些拖拉机进行试用和调整,以适应本土需求。
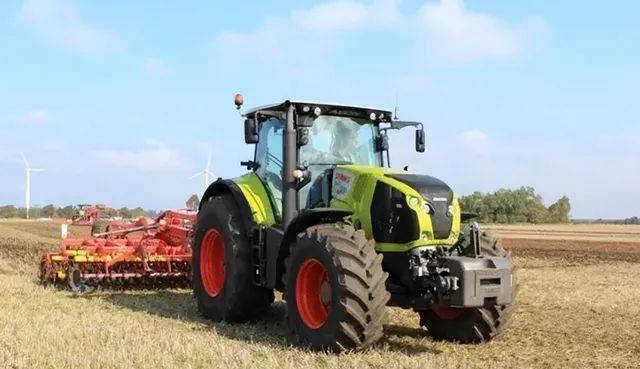
面对这些问题,国内的技术人员和工人们开始深入研究这些进口拖拉机的结构和原理。工厂里的技术骨干经常加班加点拆解研究,试图从每一个零件的设计中找到改进的方向。在不断的试用和研究过程中,他们逐渐掌握了这些拖拉机的基础生产技术。为了提高技术水平,各地的工厂纷纷设立了技术攻关小组,许多机械工程师甚至自学外语,翻阅外国的技术手册和资料,通过「边学边干」的方式,逐渐摸索出一套适合中国实际情况的生产方法。
与此同时,国家也在不断地鼓励技术创新。技术人员在生产一线不断提出改进建议,有的甚至在实验室里通宵达旦地进行各种新型零部件的测试和改造工作。许多老工人回忆,那段时间每天的工作都紧张而充实,拖拉机的生产和改进仿佛成了一场攻坚战。在这些努力下,国产拖拉机的质量逐渐得到提升,工厂开始尝试仿制国外的成熟机型,并逐步对这些机型进行适应性改良。
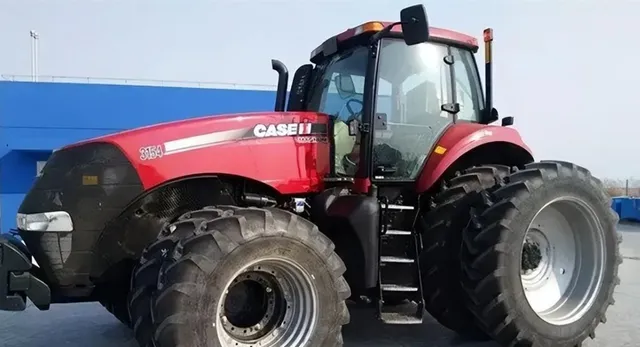
经过不断的摸索和实践,国产拖拉机的性能逐渐稳定,生产规模也逐步扩大。上世纪60年代,中国的拖拉机生产线已经能够相对稳定地批量生产多种型号的产品。随着生产规模的扩大,中国拖拉机制造逐渐实现了规模化和标准化生产。这些国产拖拉机虽然在技术上仍与国际先进水平有一定差距,但已经能够基本满足国内农业生产的需要,特别是在改善农田作业效率、减少农民体力劳动方面起到了不可忽视的作用。
技术差距的正视与改革开放的影响
改革开放后,中国的拖拉机产业迎来了新的发展机遇。随着国家经济的逐渐开放,国内企业有了更多机会与国外同行交流学习,这为中国拖拉机制造注入了新的活力。大量国外先进的机械制造技术、管理经验和设备被引入国内,国内拖拉机企业纷纷开始与国际知名企业进行合作,签订技术引进协议、进行技术转让,一些大型国企甚至直接从国外引进整套生产线。
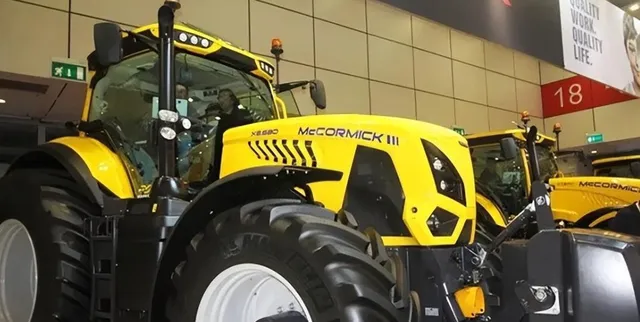
在上世纪80年代,各大拖拉机厂开始派遣技术人员前往欧美等发达国家学习先进的制造技术。这些技术人员回国后,把学到的知识和经验运用到生产实践中,从产品设计、零部件加工到装配线的优化,都进行了大量的改进。
然而,尽管取得了一定的进步,国内拖拉机企业在核心技术的掌握上仍显得力不从心。尤其是在发动机、变速箱、液压系统等关键部件的设计和制造上,国内企业仍依赖于进口技术和零部件。很多企业虽然能够自行组装拖拉机,但核心部件仍需从国外采购。这些高端零部件价格昂贵且供货周期长,直接影响了国内拖拉机的成本控制和生产效率。同时,国产拖拉机在适应性、耐久性等方面与国外产品相比仍存在较大差距。
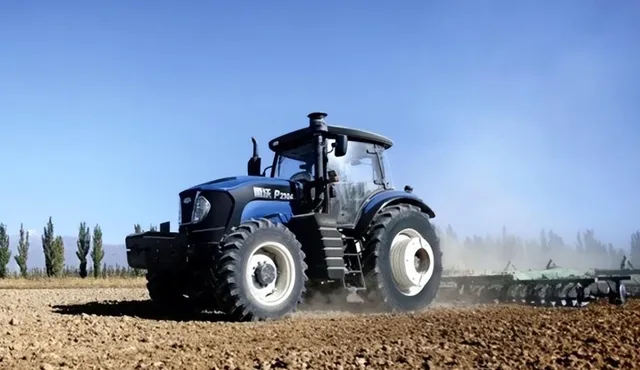
大功率化趋势与国内拖拉机的应对策略
2018年以来,国际拖拉机市场的变化显而易见,大型化、高功率化成为主流趋势。欧美市场上,各大知名品牌纷纷推出了高达500马力甚至700马力的高端拖拉机,产品不仅在功率上遥遥领先,还配备了先进的电子控制系统、自动导航等智能化功能,这些新技术显著提高了作业效率和操作舒适性。
面对国际市场的这一趋势,国内拖拉机制造商也不甘落后,纷纷跟风投入大功率拖拉机的生产。许多企业认为,只要能够生产出高功率的产品,就能在市场上占据一席之地。于是,各家企业加大了对大功率拖拉机的投入,不少中小型制造商也开始争相上马高功率机型,甚至出现了多家企业几乎同时推出200马力以上拖拉机的现象。
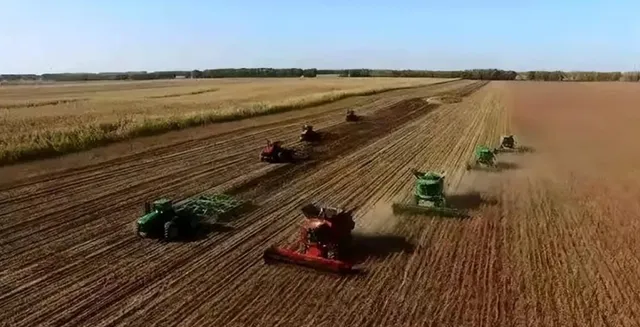
然而,问题也随之而来。由于国内拖拉机制造商在核心技术储备和产业链完善方面存在明显不足,这种盲目追求大功率的做法很快暴露出诸多问题。首先是发动机、变速箱等关键部件的技术积累不足,导致国产大功率拖拉机在实际作业中故障频发。特别是在动力输出轴、液压系统和传动装置等核心部位,问题尤为突出。这些零部件的质量和耐用性未能达到国际标准,直接影响了整机的可靠性和使用寿命。
实际使用中,拖拉机用户反映最多的问题就是各种小毛病不断,维修成本高昂。很多农场主在田间作业时常常遇到动力输出轴故障或者液压系统泄漏的问题,很多修理工表示,国产高功率拖拉机在设计和制造上存在诸多瑕疵,除了发动机性能相对稳定之外,其他部分几乎都难以令人满意。特别是齿轮、离合器等部件,磨损快、故障率高,严重影响了拖拉机的正常使用。这些问题的出现,与国内拖拉机企业的技术准备不足和产业链不完善密切相关。
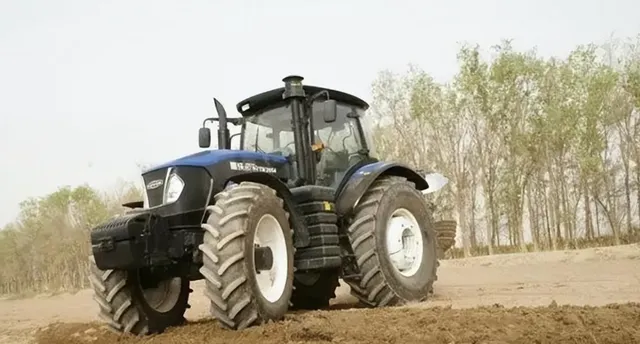
国内外技术差距的具体体现
从1990年至今,国内拖拉机的无故障使用时间一直远低于国际标准。无论是小型拖拉机还是大中型拖拉机,国内产品的无故障使用时间虽然经过多次改进有所提升,但与国际先进水平仍存在显著差距。根据相关数据,国内小型拖拉机的无故障使用时间大约在500个小时左右,而大中型拖拉机的无故障使用时间约为750个小时。相比之下,欧美国家的拖拉机在同一时期的无故障使用时间已经稳定在1500至2000小时之间,并且这一数字还在不断刷新。尤其是像美国的约翰迪尔、德国的福格尔等品牌,它们的拖拉机在各类农田作业中的可靠性和耐用性都是全球领先的,这直接反映出国际市场上拖拉机技术的差距。
欧美和日本的拖拉机不仅在基本性能上优于国产产品,在一些关键技术领域更是实现了突破性发展。例如,无极变速技术和动力换挡技术已经成为国际市场上的标准配置。这些在国外已经非常成熟的技术,在国内的普及和应用还处于起步阶段。许多国产品牌的拖拉机仍然依赖于传统的机械变速系统,缺乏对新技术的深入研究和应用,这使得国产拖拉机在国际市场上难以与外国高端产品正面对抗。
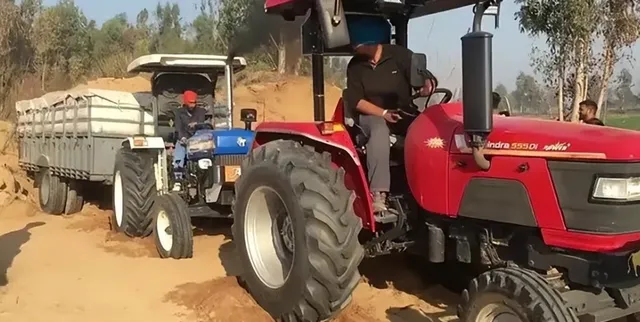
这种技术断层直接影响了国产拖拉机的市场表现。在国际市场上,高端拖拉机产品的竞争不仅是性能和质量的比拼,更是技术水平和创新能力的较量。国内的拖拉机制造商虽然努力通过改进设计、优化工艺来提高产品质量,但核心技术的缺失始终是一个难以逾越的障碍。比如,无极变速技术可以根据农田作业的需求自动调整速度和扭矩,这种智能化的操作方式极大地提高了作业效率,同时也减少了对操作者的技能要求。但由于国内企业在这一技术领域的研究起步较晚,缺乏足够的技术积累和人才储备,这一技术在国产拖拉机上的应用还远未达到国际水平。
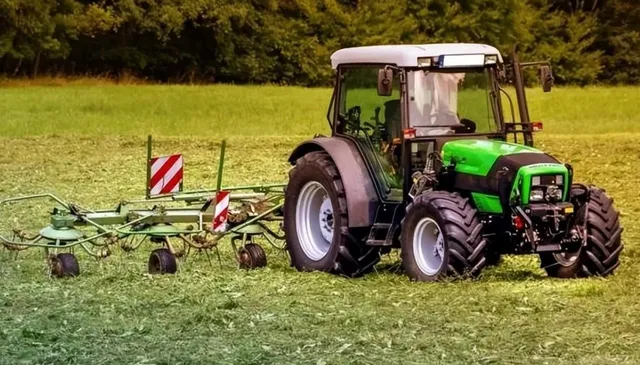
面对技术和市场的双重挑战,中国拖拉机制造业需要正视现有的技术差距。这不仅仅是简单地引进国外技术或模仿先进产品能够解决的问题,更需要国内企业在核心技术的研发上加大投入。只有不断加大研发力度,才能逐步缩小与国际先进水平的差距。近年来,一些国内企业已经意识到这一点,开始增加研发经费的投入,同时积极引进高水平的技术人才,通过自主研发和技术引进相结合的方式,逐步提升自身的技术水平。
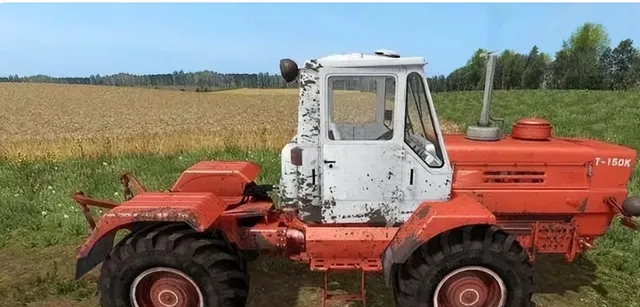
此外,市场需求的深入分析和精准定位也变得至关重要。中国拖拉机市场的特点在于农户和农场主的需求多样化,既需要高端大功率拖拉机,也需要适合小规模农田和丘陵山区的中小型机型。国内企业在产品开发过程中,必须充分了解市场需求,不仅要在高端领域进行突破,更要在中低端市场保持优势。过去几年,一些企业开始针对不同作业场景开发多元化产品,注重提升拖拉机在不同环境下的适应性,这种精准的市场定位在一定程度上提高了国产拖拉机的市场竞争力。
参考资料:[1]姚彬.从国产CVT拖拉机汉诺威首秀看中国农机强「芯」路[J].农机科技推广,2024(1):61-63
