在電子產品服役過程中,由於溫度和振動等外部環境的影響,焊點的焊料與封裝結構的樹脂等材質熱膨脹系數(CTE:Coefficient of Thermal Expansion)的不匹配會使得焊點發生蠕變而造成疲勞開裂[1]。倒裝類的BGA封裝具有較高的整合度且已廣泛地被套用於通訊端的訊號處理和儲存領域。為了提高這類焊點的熱疲勞壽命,業內采用較多的是在芯片底部填充樹脂(底部填充工藝)使其與基板膠黏固定[2],從而降低溫循過程中的熱失配應力、起到提升焊點機械強度與熱疲勞可靠性的作用。

目前較多的研究均集中在底部填充工藝後的有限元仿真分析上。透過建模仿真得到底部填充前後焊點內的應力應變分布,模擬計算底部填充後對焊點壽命的改善效果[3-5]。在隨機振動應力仿真方向發現,采用底部填充膠對焊點進行填充可以有效地降低隨機振動載荷作用下焊點內的應力應變,底充膠彈性模量越大,密度越小,越有利於減小焊點內的隨機振動應力應變[3]。熱迴圈仿真方向的結論顯示,選取一種CTE較小的環氧類底部填充膠對封裝焊點進行填充能有效地減小元件內部熱應力和焊點蠕變[4]。這類仿真在進行建模時考慮的都是膠水是否完全填充,從而忽略了具體的工藝生產中的膠水填充比例的實際影響。此外,在施加環境應力的過程中認為底部填充膠水的效能不發生老化或者改性。
關鍵詞:焊料 電阻值 焊點
本文基於IPC 7091A【表面貼裝錫焊件效能測試方法與鑒定要求】設計了菊花鏈結構的電路板及阻值即時監測系統。實驗參考仿真結果,選取了不同的玻璃化轉變溫度(Tg)和CTE的膠水在TC4(-55~125℃)溫循條件下測試焊點的熱疲勞壽命。實驗中還考慮實際的免洗工藝中助焊劑殘留等問題導致膠水無法100%填充的情況,建立了內部底部填充工藝的評估方法,對於膠水的選型及工藝質素評估具有一定的參考意義。本文最後還對溫循後失效焊點焊料的金相結構和undefill膠水的形貌進行了分析。
本文選取了Amkor公司15 mm×15 mm×1.2 mm菊花鏈結構的BGA芯片。焊球為17×17的四周陣列排布,共208個,間距(pitch)為0.8 mm。將PCB側的焊盤同樣設定為菊花鏈結構,使得焊接後所有的焊點透過芯片側和PCB側的鏈狀結構全部串聯在一起。PCB選擇FR4(Tg:130℃,Td:310℃)的6層疊板結構。其中,兩層芯板均為S1141,3層玻纖布為S2116,板厚為1.6 mm,銅厚為0.035 mm。焊料采用無鉛SAC305體系的ALPHA OM-340。焊點菊花鏈結構設計如圖1所示。
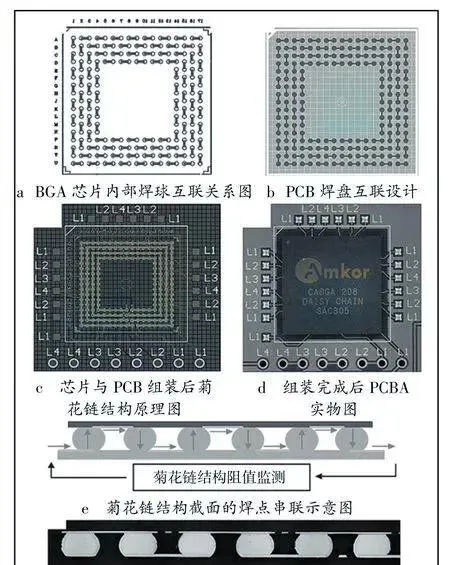
圖1 焊點菊花鏈結構設計
底部填充膠是利用毛細作用使得膠水滲透進入BGA芯片底部,經加熱固化後在芯片封裝和PCB之間形成牢固的填充層,起到包裹保護焊點的作用。當填充工藝不良時,容易出現芯片底部膠水滲透不良而產生氣泡或者芯片封裝側面充填高度不足;而過量塗覆,則會導致膠水溢位流到器件表面或其他位置,影響外觀及後續的組裝測試。此外,目前的電子產品一般均采用無鉛免洗工藝,助焊劑的殘留也容易導致膠水無法完全包裹焊點。底部填充工藝質素如圖2所示。

圖2 底部填充工藝質素
綜合衡量各類產品的底部填充需求,本專案考慮從底部填充比例和側面的填充高度來對底部填充膠水的工藝質素進行管控。
為了保證底部填充膠水能有效地包裹所有的焊點,本文中底部填充質素的評估標準是側面填充高度超過芯片塑封體厚度的1/2(如圖2所示,h/H>50%)且底部的膠水填充率>95%。允許焊點PCB側存在少量的氣泡,但所有的焊點周圍均要有填充,不允許膠水外溢到芯片封裝的表面。
部份研究結果顯示,底填膠水對焊點的熱疲勞壽命改善效果與膠水的CTE相關[4]。因此本實驗選取了3款典型的CTE膠水,同時兼顧了膠水是否可返修效能(A的Tg值最小,最容易返修;C的Tg值居中,可以返修;B類Tg值較高不可返修),如表1所示。

表1 3款待評估底部填充膠水的材料效能參數
本實驗參考了IPC 7091A中的TC4等級加速條件(-55~125℃)。最高溫和最低溫駐留時間都為10 min,溫變時間為15 min(溫變速率為12~20℃/min)。
溫度參數設定完成後,實際監測箱內溫度與焊點處的溫度發現,箱子內部溫度變化情況與設定溫度基本一致,但焊點處的實際溫度與設定溫度存在較大的差異,實際的焊點溫度範圍為:-42.3~101.6℃,如圖3a所示。經排查發現,溫差是由於實驗測試板的熱傳導系數決定的,PCB的銅箔和樹脂等材料的散熱效能和溫變速率使得焊點處的溫度無法與設定參數保持一致。焊點經歷的實際溫度迴圈條件仍呈現周期性且與設定參數的周期一致,但是最高溫與最低溫以及溫變速率存在差異。後續的仿真分析需考慮這一實際情況。
測試開始後同步監測某條菊花鏈結構的電阻值變化,結果如圖3b所示。初始狀態下(常溫且焊點結構正常)電阻約為6.4Ω,此時電阻值來源於焊點、導線等處的互聯電阻。當溫循開始時,電阻值隨溫箱內溫度同步呈現小範圍內的周期性波動,這是由溫箱內的焊點及導線內阻隨溫度變化而導致的。

圖3 溫度迴圈測試結果
某菊花鏈焊點結構1 000個迴圈過程中的阻值變化如圖4所示。參考IPC 7091A,本文將菊花鏈的電阻值變為100Ω的時刻作為焊點完全失效的判斷點。
圖4顯示,實驗開始後電阻值維持在很小的值不變,從某一時刻開始出現波動,此後一直呈現更大範圍的變化。聚焦到電阻值開始波動的那一個時刻發現,在此時刻之前,焊點菊花鏈的電阻值基本與初始時刻一致且仍是保持隨溫度呈現周期性變化的規律。從該時刻起,阻值開始變大,且此後迅速地變為幾千歐姆甚至無窮大,呈現為無規律的電阻值波動。當電阻值超過100Ω後,後面的溫度迴圈周期內,焊點阻值也不會恢復正常狀態,可以排除此時刻電阻變化是環境變化等導致的異常點,該點時刻可以用來表征焊點阻值隨時間的變化情況。
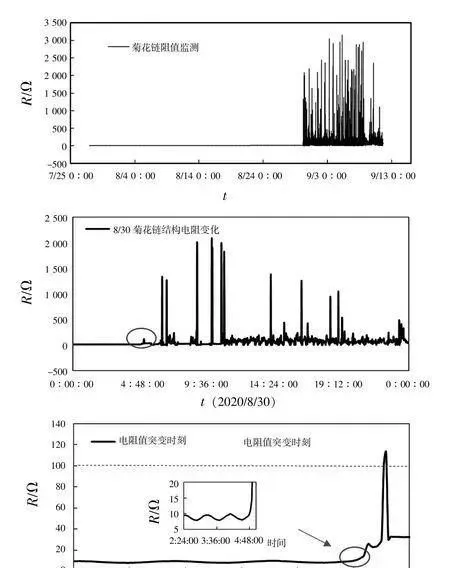
圖4 焊點菊花鏈結構電阻值監測結果
監測每一個菊花鏈結構的電阻值變化並統計焊點失效點時刻,以此作為該結構的焊點熱疲勞迴圈壽命。
統計1 000個溫度迴圈測試後菊花鏈焊點失效迴圈數。經檢驗,該數據符合兩參數的威布爾分布,焊點壽命分布如圖5所示。
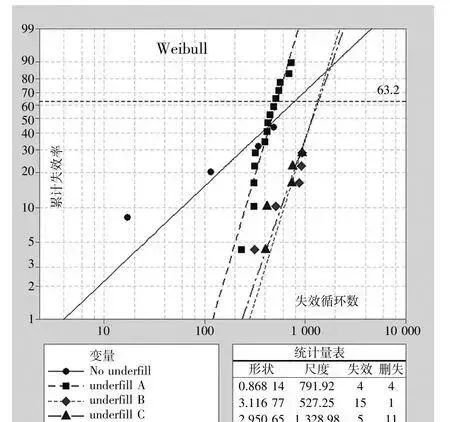
圖5 溫度迴圈測試後焊點熱疲勞壽命的威布爾分布
統計分布數據表明,B和C兩種底填膠水的壽命Nf(63.2%)約為1 350個迴圈,相比於無底部填充膠時焊點壽命約提升了2倍。然而,A類底部填充膠後的焊點壽命約為527個迴圈,比無底部填充膠可靠性差。
分別選擇這幾類溫循後失效的菊花鏈焊點進行切片分析發現,焊點內部確實出現了熱疲勞性開裂,並且芯片的最外圈焊點開裂得最多,這與仿真結果(邊緣焊點最容易開裂)一致。
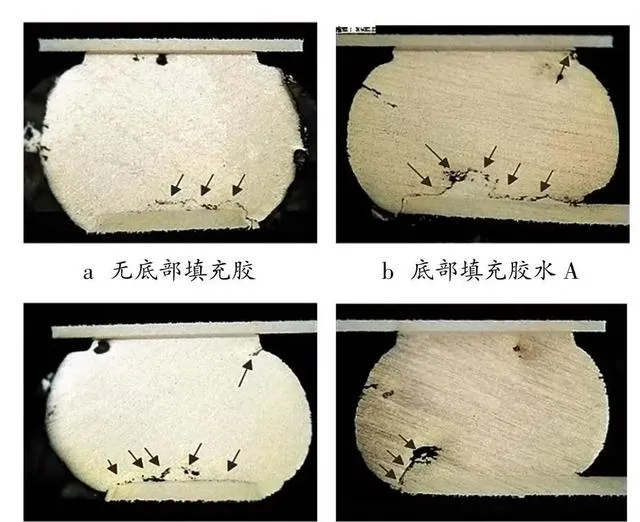
圖6 菊花鏈結構失效焊點切片分析
進一步對失效焊點裂紋進行金相結構分析發現(如圖7所示),裂紋是從焊點邊緣處的金屬間化合物(IMC)開始產生的,然後逐漸地向焊點內部擴充套件。SEM結果顯示,焊料裂紋基本是沿著大的顆粒Ag3Sn的晶界處生長,這些大的晶粒來源於溫度迴圈過程中焊料的重結晶。隨著結晶過程的產生,晶粒開始生長粗化從而產生更大的晶界,並逐漸地擴充套件為微裂紋。

圖7 失效焊點裂紋金相及SEM分析
一般認為,焊點的IMC處最脆最容易出現機械應力開裂[5-6]。當焊點邊緣IMC處出現起裂點後,裂紋沿著焊料內部晶粒粗化形成的晶界微裂紋生長,並最終形成貫穿整個焊點的大裂紋。
如圖8所示,對有底部填充工藝的樣品進行切片檢查發現,本實驗中樣品的底填工藝側面填充質素均良好,並且實驗後未發現側面膠水有分層開裂異常。進一步地檢查焊點周圍的膠水發現,A、B和C 3類膠水均存在不同程度的開裂,部份位置的膠水裂紋有向PCB或者芯片基板中擴充套件,甚至PCB焊盤和內部玻纖有被拉扯變形和開裂。

圖8 溫度迴圈測試後底部填充膠水的形貌分析
底部填充膠水裂紋主要是從膠水與焊球的接觸位置開始出現的。這是由於SMT使用的免洗工藝導致焊球邊緣有助焊劑殘留包裹,使得底填膠水與焊料或者PCB的粘合強度導致的。膠水的吸濕效能以及在熱迴圈條件下的效能退化(老化),也會加速膠水的老化開裂[7]。
本文基於IPC 7091A焊點可靠性實驗參考標準,設計並討論了在熱迴圈交變條件下的無底部填充工藝和有底部填充工藝下的BGA焊點可靠性壽命,得出了以下幾點結論。
a)底部填充膠水對焊點熱疲勞壽命的改善效果與膠水的效能密切相關。選擇高Tg值與低CTE的底部填充膠水,可以增強焊點的熱疲勞壽命;而低Tg和高CTE的膠水則會帶來相反的效果,導致焊點更容易熱疲勞開裂。
b)采用無鉛免洗工藝會使得焊點周圍有較多的助焊劑殘留並影響底部填充效果。進行底填工藝時,應透過工藝改善最佳化,減小底填膠水內的空洞。建議底部填充率>95%,且芯片表面無溢膠。
c)進行可靠性溫循實驗,焊點處的實際溫度與溫箱設定溫度存在差異,下一步進行焊點有限元仿真分析時需關註實際的溫循條件。
d)焊點熱疲勞裂紋是從IMC處開始產生的,然後向焊料內部擴充套件。焊料內的微裂紋沿晶格重結晶晶粒的晶界處生長。底填膠水的老化開裂,也是加速焊點熱疲勞失效的原因。