文 | 【中國科學報】 記者 陳彬
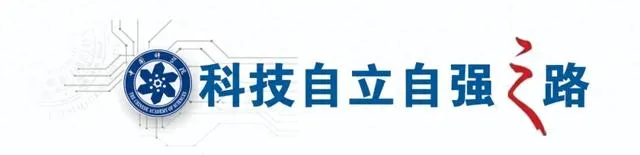
中國科學院金屬研究所(以下簡稱金屬所)研究員李殿中永遠忘不了2020年的一天,當他走進某國內盾構機制造企業的倉庫時,眼前的一切讓他震撼不已。
「盾構機制造是一項長周期工作,本不需要儲備過多元件,但這間倉居里卻放著十幾套盾構機主軸承,總價值達上億元。」李殿中說。
彼時,中國已進入軌域交通基礎設施建設高峰期。作為鑿山開路、過江跨海工程專案的利器,大型盾構機已實作大部份部件的國產化,但最關鍵的核心部件——主軸承卻長期依賴進口。
如果將大型盾構機比作一個人,那麽主軸承的作用堪比心臟。當「心臟」被攥在別人手心時,盾構機制造企業所承受的壓力以及中國基礎設施建設面臨的潛在風險可想而知。於是,為了規避可能的「斷供」,很多企業只能不惜成本囤積大量主軸承。
「我們有責任給國產大型盾構機裝上一顆‘中國心’。」李殿中暗下決心。
2022年12月15日,金屬所宣布,李殿中和該所研究員、中國科學院院士李依依,該所研究員胡小強帶領團隊,聯合國內其他研究機構和企業,成功研制出超大型盾構機用直徑8米主軸承。中國大型盾構機國產化和自主可控鏈條由此順利打通。
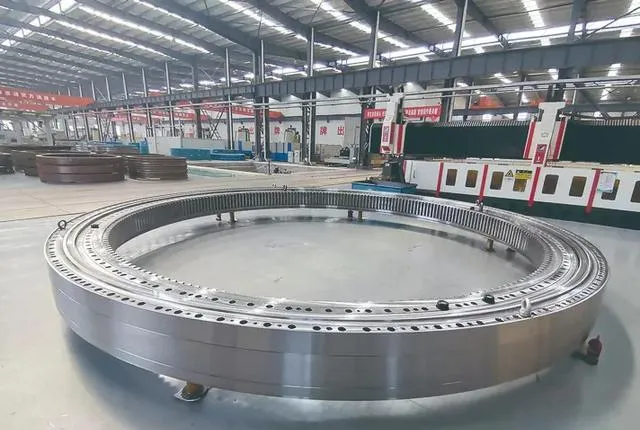
自研超大型盾構機用直徑8米級主軸承。
幾代人接力攻克「稀土鋼」
盾構機全名盾構隧道掘進機,是一種隧道掘進的專用工程機械,其主軸承是刀盤驅動系統的關鍵核心部件。盾構機在掘進過程中,主軸承「手持」刀盤旋轉,切削掌子面並為刀盤提供旋轉支撐。
「直徑8米的主軸承在運轉過程中,承載的最大軸向力可達1億牛頓,相當於2500頭成年亞洲象的體重。」胡小強介紹,大型盾構機在掘進時只能前進不能倒退,主軸承一旦失效,會造成嚴重損失。主軸承的國產化自然而然成為必須攻克的「卡脖子」難題。
然而,這個問題出現在李殿中和同事們視野中的時間並不長。至少在2019年之前,他們更多關註的是另一個「老大難」問題——研發「稀土鋼」。
所謂稀土鋼,簡單地說,便是在鋼材制造過程中加入一定比例的稀土元素,從而改變鋼材的某些特性。這看似容易,實則困難重重。
稀土被稱為工業的「維生素」,大量研究表明,添加微量稀土就能顯著提高鋼材的韌塑性、耐磨性、耐熱性、耐蝕性等。正因如此,稀土添加過程中的微小變化或摻雜雜質,都會引發很多不可測的問題。
「在稀土鋼的研發過程中,有兩個始終繞不過去的難題。」胡小強說,一是鋼材在添加稀土後,效能往往會劇烈波動,存在穩定性不好的問題;二是很多大型關鍵零部件的材料制備不能在實驗室完成,很難保證稀土在大工業環境下穩定發揮作用。
為了解決上述問題,自20世紀50年代起,金屬所幾代科研人員接力攻關,就稀土元素對鋼材的影響進行了深入研究。直到2007年,在進行一項針對厚大斷面大型鋼錠的科研攻關專案時,金屬所科研團隊偶然發現稀土鋼效能波動問題的根源可能在於稀土元素自身的氧雜質,而非傳統認為的鋼材內部雜質。
由此,科研團隊順藤摸瓜,經過大量實驗、計算和表征,最終揭示了稀土在鋼中的主要作用機制,並開發出一套「雙低氧稀土鋼」關鍵技術。采用該技術研制出的稀土鋼的拉壓疲勞壽命延長40多倍,捲動接觸非疲勞壽命提升40%。
由此,稀土鋼的問題被徹底解決了。而彼時沈浸在喜悅中的科研人員還不知道,眼前的成績不僅是他們過去幾十年努力的碩果,更將是未來開展大型盾構機主軸承攻關的重要基石。
「國家隊」需要站出來
彼時,正值中國科學院組織實施戰略性先導科技專項。伴隨著專項的實施,一項歷史性使命落到了金屬所科研人員身上。
先導專項是中國科學院瞄準事關中國全域和長遠發展的重大科技問題提出的一項戰略行動計劃。自2019年開始,金屬所希望依托自身在稀土鋼方面的長期積累,凝練、提出和承擔一項與此相關的先導專項,並為此開展了廣泛的實地調研。
「最初,我們並沒有將研發重點放在大型盾構機的主軸承上。」李殿中回憶說,直至2019年歲末年初,在調研了國內十幾個省份的30余家單位後,他們才發現主軸承的國產化已是一個不容忽視的「卡脖子」難題。
中國引入首台盾構機是在1997年,並於本世紀初開始探索盾構機的國產化。至2019年,盾構機的幾乎所有部件均可以實作自給,唯獨最關鍵的主軸承始終依賴國外進口。由此產生的問題,國內企業的感受最深刻。
在與胡小強等人交談時,某盾構機制造企業領導算過一筆賬,由於核心技術不在自己手中,從國外進口一套主軸承的價格往往超過千萬元。不但價格昂貴,而且在正常情況下,盾構機主軸承的進口訂貨周期短則10個月,長則超過一年。但中國的很多基建專案,從立項到完工也不過三五年時間。
更重要的是,由於存在供貨隨時停止的風險,國內企業對依靠外國供貨總有一種「不安全感」,最終轉化為希望盾構機主軸承國產化的一致呼聲。
但同時,對於使用國產器材,國內企業又存在矛盾心理——盾構機造價動輒幾千萬元,其背後的基建工程花費更以億元計,國產主軸承即便研制出來,使用風險有多大,誰的心裏也沒底。
胡小強總結了研發主軸承必須克服的三大困難——
其一,大型主軸承最大直徑達8米,承載幾萬噸,但加工精度要達到微米級別,其技術難度可想而知。
其二,盾構機在施工過程中不能後退,主軸承一旦出現問題將無法更換,導致在實際套用場景中的試驗風險特別高。
其三,大型主軸承的攻關鏈條特別長,涉及結構設計、材料制備、加工裝配、測試評價和套用考核等諸多環節,關聯到20多家單位,僅制造過程就有130多道工序。
李殿中認為,要克服以上困難,必須從基礎理論做起,向上整合各研發生產鏈,才能保證最終結果萬無一失,「也正因如此,需要我們‘國家隊’站出來」。
說出這番話,金屬所的科研團隊是有底氣的。他們發現,經過幾代人接力攻關所解決的稀土鋼制備問題,已經從理論和材料層面為大型主軸承的研發打下了堅實「地基」。他們接下來要做的是,在這片「地基」上蓋起自立自強的「高樓大廈」。
2020年2月,中國科學院正式啟動先導專項「高端軸承自主可控制造」。金屬所整合所內軸承鋼、熱處理、陶瓷、保持架等12個團隊,以及院內7家研究所的力量,組建了覆蓋軸承研發、軸承材料、制造、評價與服役全生命周期的全鏈條科技團隊。
一場新的「戰役」就此打響。
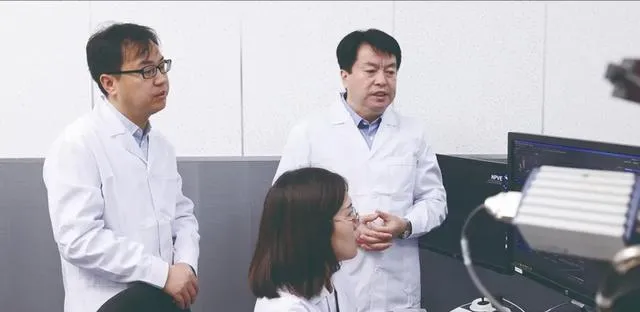
胡小強(左)、李殿中(右)在實驗室。
1.5微米的「天塹」
2020年「五一」假期前一天,一架從沈陽飛往廣州的客機即將落地。胡小強和幾位同事充滿期待地看著舷窗外繁華的都市。
他們此行的目的地是廣州貝崗的一處基地。那裏有一台主軸承直徑6.3米的盾構機,由於超出設計使用裏程,需要接受專家評估。得知訊息的他們馬上趕過去,全程參與了對盾構機主軸承的測評和分析,並詳細了解主軸承的每一處細節。
在承接先導專項任務之前,金屬所的科研人員並沒有設計盾構機主軸承的太多經驗。「正因如此,我們不會放棄任何一次學習和調研的機會。」胡小強說。
即便這樣,想要單打獨鬥完成這項工作也不現實。
憑借前述自主開發的「雙低氧稀土鋼」關鍵技術,科研人員已經實作了對主軸承大型套圈和大型滾子「潔凈、均質」的制備,並獲得強韌性、抗疲勞性和耐磨性等綜合效能較好的鋼材,這為大型主軸承的研制打下了很好的基礎。至於主軸承的設計問題,則可以一點點摸索、學習。但李殿中坦言,他們還要面對另一個難題——軸承加工精度不過關。這個難題不是單靠研究人員的努力就能解決的。
當時,中國進口器材由於受國外技術限制,大型滾子的加工精度只能達到二級,即幾百個滾子直徑的誤差不大於正負2.5微米,但要制造出符合盾構機要求的滾子,加工精度必須達到一級,即柱體直徑誤差不能大於正負1微米,兩者之間1.5微米的差距,雖然僅相當於一根頭發絲直徑的1/40,但在科研團隊的眼中無異於一道「天塹」。
要跨過這道「天塹」,只能聯合企業一同攻關。
直到現在,談及與企業的合作,胡小強言語中仍有些激動。據他回憶,意識到問題後,他們便主動聯合相關企業一起討論、建模,從基本理念到方法,再到具體實踐。「我們提需求,相關企業一起攻關。一邊幹一邊解決隨時出現的問題。」
與金屬所合作進行滾子加工的是遼寧省內一家主要從事風力電機滾子加工的企業。此前,該企業從未加工過直徑這麽大、精度這麽高的滾子。合作之初,幾乎每次技術升級嘗試都宣告失敗。
「那段時間,每個人都承受著巨大的壓力,以至於合作企業的現場負責人開始懷疑,他們采用自主開發的工藝和生產線是否能實作如此高精度等級的加工。」胡小強回憶道。
然而,經過反復論證和計算,科研團隊堅信他們的精度要求是可以達到的,企業也選擇相信他們的論斷,並嚴格按照給定的工藝要求,一步步嚴格推進。
當完全符合要求的滾子被加工出來,企業負責人透過電話向胡小強報喜時,那種激動與自豪的語氣令胡小強記憶猶新。
由此,中國企業徹底掌握了大型滾子的一級精度加工技術,並一舉達到國際先進水平。
未完成的挑戰
耗時3年,經20多家科研機構和企業通力合作,主軸承材料制備、精密加工、成套設計中的12項核心關鍵技術問題先後被解決。最終,科研團隊成功用1467.4噸稀土軸承鋼研制出41支大型套圈、7996粒滾子、492段銅鋼復合保持架……陸續生產出直徑3米級到8米級共10套4個型號的國產盾構機主軸承。
2021年11月,在沈陽市政府的支持下,裝有自研直徑3米主軸承的盾構機正式下線,並在沈陽地鐵工程中成功套用。
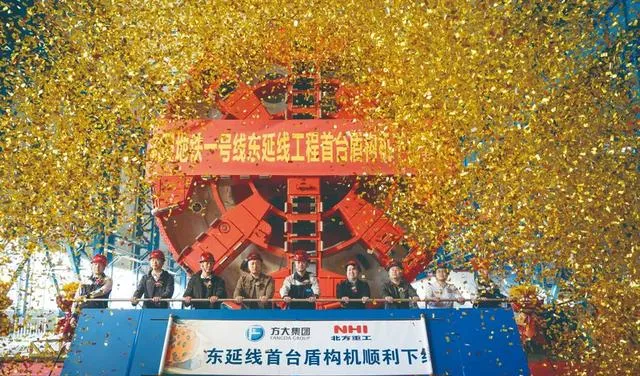
2021年11月,裝有自研直徑3米級主軸承的盾構機下線儀式舉行。
2022年9月30日,超大型盾構機用直徑8米級主軸承驗收合格,標誌著由金屬所領銜的「高端軸承自主可控制造」先導專項任務圓滿完成。
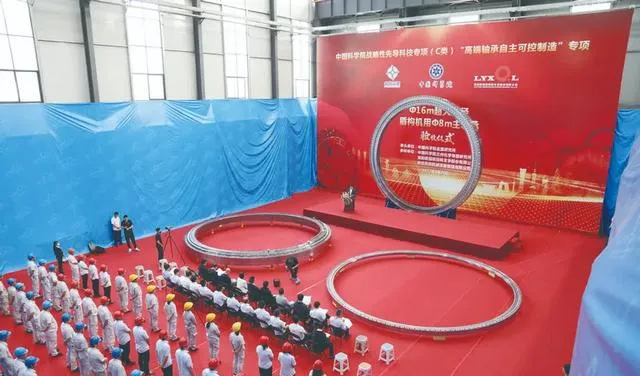
自研直徑8米級主軸承驗收會。
一天後的國慶假期,幾乎3年沒休過節假日的科研人員終於可以休息了。而胡小強回到家後的第二天,雙眼便腫脹到完全看不見東西。
「把任務卸下來後,身體裏積攢的‘火氣’就湧出來了。」李殿中對胡小強「病因」的診斷並非完全戲謔之言。
李殿中總結,在攻克盾構機主軸承技術的過程中,金屬所走通了一條從基礎研究出發、組織建制化攻關,到攻克「卡脖子」難題的科技創新之路。
他介紹說,中國科學院對套用性強的戰略性先導專項管理一般采取「行政指揮線」「技術指揮線」雙線並列的模式。金屬所領導班子經過深刻思考,從強化「高端軸承自主可控制造」專項管理的角度出發,在「雙線」的基礎上進一步建立「黨委保障線」的三線並列機制。
「我們構建了‘院領導—業務局—研究所’三級高效協同的管理架構,上下貫通,黨政聯動,多方互動。」受訪時,金屬所所長劉崗表示,正是在這樣的有組織科研體系下,科研人員的工作熱情被最大化激發出來。
胡小強清晰記得,2022年7月,專案已經進入「會戰」階段,從全國各地制造完成的零件陸續運抵河南洛陽,準備組裝。就在這一關鍵節點,人們發現目前的機床器材出現了問題——用於給器材進行表面淬火的機床完全無法滿足如此大直徑軸承的使用要求,同樣不具備使用要求的還有高精度磨床。
「事實上,當時國內生產的高精度磨床都無法滿足要求,要進口的話,直徑5米的磨床不但要價高達8000萬元,而且制造周期要兩年;至於直徑8米的磨床,國外對我們完全禁售。」胡小強說。
這是一個幾乎無法解決的難題,嚴重的挫敗感籠罩在大家心頭。金屬所黨委迅速作出決定,組建以首任所長李薰名字命名的「李薰大型多載軸承攻關突擊隊」。在突擊隊成立大會上,李依依深情講述了李薰當年舍棄國外奮鬥多年所得,沖破重重阻礙回到祖國,率領團隊開展「兩彈一星」關鍵材料攻關的感人事跡……
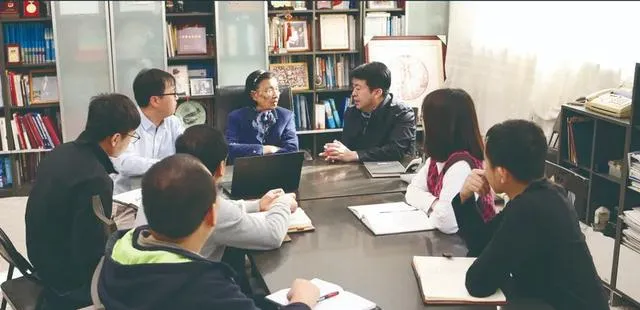
李依依(右四)主持研討工作。
這份回憶感染、激勵了突擊隊的每名成員。在其感召下,所有攻關人員群策群力、反復探索。現有機床不能滿足要求,就聯合各單位在現場一點點改造;買不到合適的磨床,就試著將大直徑車床改造成磨床,取得一定參數後,聯合磨床企業共同研發……
最終,問題被一點點解決,專案得以順利推進。
如今,大型盾構機主軸承專案已經塵埃落定,當年的昂揚鬥誌已沈澱為科研人員腦中一段沈甸甸的回憶。但這並不代表所有任務都已完成,正如李殿中所言,「針對‘卡脖子’問題的科研只有落實到產業、只有構建完整的產業生態鏈,才能徹底解決問題」。
他表示,在大型盾構機主軸承專案上,技術層面的問題已經得到解決,但在產業層面還需要和業界共同合作,持續發力。「目前,主軸承產業化基地正式落地,為打通盾構機國產化‘最後一公裏’奠定了堅實基礎。」
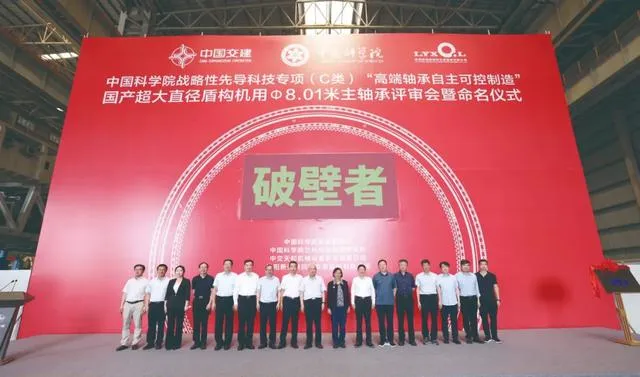
自研的直徑8.01米主軸承透過評審並被正式命名為「破壁者」。金屬所供圖
李殿中暢想著高端主軸承相關技術的進一步套用。他說:「我們可以把它套用到風電等新能源領域,當然還有疏浚、塔吊、港機,乃至於一些高端精密醫療器械中。」
他們時刻準備著,迎接下一場關鍵技術的挑戰。