(報告出品方/作者:華寶證券,胡鴻宇)
1. 碳化矽產業鏈包括上遊襯底和外延、中遊器件、下遊套用
以碳化矽材料為襯底的產業鏈主要包括碳化矽襯底材料的制備、外延層的生長、器件制造以及下遊套用市場。從工藝流程上看,碳化矽一般是先被制作成晶錠,然後經過切片、打磨、拋光得到碳化矽襯底;襯底上生長單晶外延材料。外延片經過光刻、刻蝕、離子註入、沈積等步驟制造成碳化矽功率器件和碳化矽射頻器件。將晶圓切割成die,經過封裝得到器件,器件組合在一起放入特殊外殼中組裝成模組。
碳化矽產業鏈附加值向上遊集中,襯底和外延的成本占比最高。根據CASA整理的數據,產業鏈中,碳化矽襯底和外延的成本分別占整個器件成本的47%和23%,為產業鏈中價值量最大的兩個環節,相比矽基器件、價值量顯著倒掛。
2. 襯底:產業鏈價值量占比高,良率和訂單是勝負手
2.1. 技術及資本密集型產業,是碳化矽降本的關鍵環節
襯底在碳化矽產業鏈中價值量最高,高達 47%。碳化矽產業鏈附加值向上遊集中,襯底和外延的成本占比最高。根據 CASA 整理的數據,產業鏈中,碳化矽襯底和外延的成本分別占整個器件成本的 47%和 23%,為產業鏈中價值量最大的兩個環節,相比矽基器件、價值量顯著倒掛。
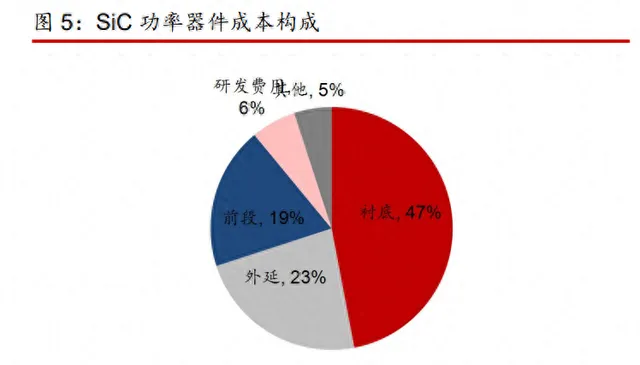
襯底屬於技術密集型行業,生產工藝水平直接影響良率。從生產工藝來看,以高純碳粉、高純矽粉為原料合成碳化矽微粉,在碳化矽單晶爐中進行碳化矽單晶生長,再經過晶碇切磨拋及清洗等工序,產出碳化矽襯底。襯底的品質影響下遊外延和器件的品質,優質的襯底可以抑制外延生長缺陷和器件效能退化,但襯底的控制難度又較大,其生產過程中的每個環節都具有較高技術要求,當每個環節都具有一定良率損耗時,合在一起就會產生指數級遞增的損耗,碳化矽襯底龍頭 Wolfspeed 良率也僅為 65%,這其中技術難度最高的又是長晶環節:
原料合成:獲得高純度碳化矽粉難度高。將高純矽粉和高純碳粉按一定配比混合,在2,000℃以上的高溫下反應合成碳化矽顆粒。再經過破碎、清洗等工序,制得滿足晶體生長要求的高純度碳化矽微粉原料。難點在於碳化矽粉料合成過程中的環境雜質多,難以獲得高純度的粉料;作為反應源的矽粉和碳粉反應不完全易造成 Si/C 比失衡;碳化矽粉料合成後的晶型和顆粒粒度難控制。 晶體生長:長晶是技術難度最高的環節,工藝水平決定良率。長晶技術包括 PVT 法(物理氣相傳輸法)、溶液法和高溫氣相化學沈積法等,目前商用碳化矽單晶生長均采用 PVT 法。具體原理為將高純碳化矽微粉和籽晶分別置於單晶生長爐內圓柱狀密閉的石墨坩堝下部和頂部,透過電磁感應將坩堝加熱至2,000℃以上,控制籽晶處溫度略低於下部微粉處,在坩堝內形成軸向溫度梯度。碳化矽微粉在高溫下昇華形成氣相的Si2C、SiC2、Si 等物質,在溫度梯度驅動下到達溫度較低的籽晶處,並在其上結晶形成圓柱狀碳化矽晶錠。
長晶有以下難點: 1) 熱場控制難:密閉高溫腔體監控難度高不可控制。區別於傳統矽基的溶液直拉式長晶裝置自動化程度高、長晶過程可觀察可控制調整,碳化矽晶體在2,000℃以上的高溫環境中密閉空間生長,且在生產中需要精確調控生長溫度,溫度控制難度高;2) 晶型控制難:生長過程容易發生微管、多型夾雜、位錯等缺陷,且相互影響和演變。微管(MP)是尺寸為幾微米到數十微米的貫穿型缺陷,是器件的殺手型缺陷;碳化矽單晶包括 200 多種不同晶型,但僅少數幾種晶體結構(4H 型)才是生產所需的半導體材料,生長過程中易產生晶型轉變造成多型夾雜缺陷,因此需要精確控制矽碳比、生長溫度梯度、晶體生長速率以及氣流氣壓等參數;此外,碳化矽單晶生長熱場存在溫度梯度,導致晶體生長過程中存在原生內應力及由此誘生的位錯(基平面位錯BPD、螺旋位錯 TSD、刃型位錯 TED)等缺陷,從而影響後續外延和器件的品質和效能。3) 摻雜控制難:必須嚴格控制外部雜質的引入,從而獲得定向摻雜的導電型晶體;4) 生長速度慢:碳化矽的長晶速度非常慢,傳統的矽材料只需3 天就可以長成一根晶棒,而碳化矽晶棒需要 7 天,這就導致碳化矽生產效率天然地更低,產出非常受限。
結合密閉生長,容易發生諸多缺陷,因此很難在生長過程中及時發現並進行調整,需要等到每一次生長完成後再不斷改進工藝,這不僅僅需要原理的認識,更需要時間的積累,是一個非常漫長且艱難的過程。 碳化矽襯底由於加工環節復雜且耗時,裝置投資額較高屬於資本密集型產業。從碳化矽襯底的制備流程來看,需要碳化矽粉料合成裝置、長晶爐、切片機、研磨機和拋光機、量測儀器等,其中最為關鍵的核心裝置就是長晶爐,由於晶體生長速度非常慢且良率低,長晶過程需要大量的單晶爐,要獲得一定規模效應以降低成本就需要大量裝置投入。單晶爐國產化率較高,國內有外采和自研兩種形式。那些技術積累水平較深發展時間較長的襯底廠商大多自研長晶爐,大多數後進入者采用外采的方式。國內的碳化矽單晶爐裝置供應商主要有北方華創和晶升股份,兩者在國內占有的份額超過 70%,國產化程度較高。全球範圍看,國際主流半導體材料廠商經過數十年積累,其工藝和產品遠領先於業界同行,多透過自研以釘選裝置從而保持領先水平(如日本信越化學和日本勝高),部份選擇向 S-TECH Co, Ltd.等公司采購裝置。由於裝置認證周期較長、廠商更換成本、穩定性風險等因素,國產供應商尚未實作國際主流碳化矽廠商的裝置供應。
晶錠加工:將碳化矽晶錠使用 X 射線單晶定向儀進行定向,之後透過精密機械加工的方式磨平、滾圓,加工成標準直徑尺寸和角度的碳化矽晶棒。對所有成型晶棒進行尺寸、角度等指標檢測。 晶棒切割、研磨拋光及清洗:容易發生翹曲、表面劃傷、表面粗糙度高等問題。碳化矽硬度與金剛石接近,切割、研磨、拋光技術難度大,加工過程中存在易開裂問題,加工完成後的襯底易存在翹曲等品質問題;為了達到下遊外延開盒即用的品質水平,需要對碳化矽襯底表面進行超精密加工,以降低表面粗糙度、表面平整度並達到嚴苛的金屬、顆粒控制要求。根據英飛淩的數據,在傳統的往復式金剛石固結磨料多線切割方法下,在切割環節對整體材料利用率僅有 50%,經過拋光研磨環節後,切損耗比例則高達 75%,可用部份比例較低。
2.2. 國產廠商進展不斷加速,良率和訂單是勝負手
2.2.1. 國產廠商順應產業趨勢,加速釋放產能
供給端,海外廠商在 SiC 襯底賽道具備先發優勢,國產廠商加速釋放產能。根據Yole的數據, 2022 年全球碳化矽襯底市場中,美國 Wolfspeed、美國Ⅱ-Ⅵ和日本Rohm(收購德國 SICrystal)三家企業合計占據全球約 72%的市場份額。中國公司天科合達、天嶽先進努力追趕,2022 年導電型襯底合計實作營收 1.04 億美元,合計占比15%,同比+5pct。
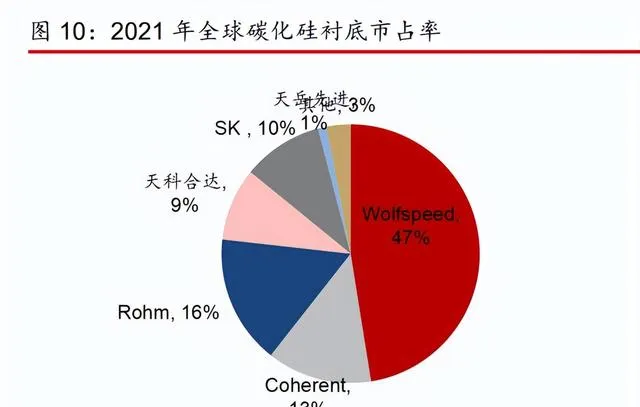
目前海外廠商加速碳化矽擴產行程,並大力布局 8 英寸。在碳化矽市場的全球格局中,海外企業由於早期投入和技術研發等優勢,占據了主導地位。國際大廠產能加速擴張,積極布局碳化矽市場,爭先恐後加碼擴產。當前國際大廠仍以 6 英寸晶圓為主,為進一步提升產能,降低單個器件的成本,如英飛淩、Wolfspeed、ST、羅姆半導體等幾年前就開始布局8寸碳化矽晶圓,並計劃逐漸實作向 8 英寸晶圓的過渡。2015 年 Wolfspeed 便對外展示了8英寸碳化矽襯底,2019 年投入 10 億美元進行 8 英寸晶圓廠建設,並於2022 年宣布投資13億美元建設8英寸碳化矽襯底工廠,羅姆、意法半導體等諸多大廠均宣布投資建設8 英寸碳化矽襯底。雖然海外市場擴產腳步已紛紛轉向 8 英寸,但實際大規模量產仍需到2025 年之後。
國內廠商加快擴產打造規模優勢,8 英寸正在突破技術。下遊套用市場龐大,無論是在新能源汽車還是光伏太陽能行業,國內都具備領先優勢,在市場需求快速爆發的背景下,國內企業一方面加快對技術差距的追趕,另一方面也在積極投入大量資源進行產線的建設來滿足市場需求和提供技術叠代的產業土壤,如天科合達、山東天嶽等頭部廠商持續加大投入進行擴產。國產 SiC 襯底廠商積極擴產,積極把握碳化矽市場視窗期。根據CASA統計,2022年中國襯底產能達到 94 萬片/年。根據我們的不完全統計,預計 2023 年底中國襯底產能已超過130萬片/年,增速迅猛。雖然擴產規模及速度較快,但能夠規模化量產出貨的只有天嶽先進、天科合達、山西爍科、同光晶體、南砂晶圓五家,其他公司均處於研發或小批次階段,而8英寸襯底量產出貨的也僅山西爍科一家。
2.2.2. 良率和訂單是企業盈利的關鍵
關註有效產能,企業需要平衡規模提高盈利能力。盡管各國產廠商規劃產能增速極高,但由於碳化矽襯底存在降低缺陷密度等技術門檻,因此並非所有規劃產能均能如期實際交付。核心裝置目前大多都已實作國產化,單台裝置投資額也不超過200 萬,因此裝置和資本並非關鍵卡點,更為重要的是工藝——掌握能夠大批次生產的工藝,獲得規模效應且提高良率,能夠低成本、高品質、大批次供應才是真正的產業化。規劃布局的投資規模並不等於實際能夠達到的生產能力,並不等於能夠實作的供貨能力,更不對於能夠獲得的市場收入。由於目前技術工藝的不完善,襯底良率水平較低,需要透過打造規模效應打磨工藝、降低成本、獲得客戶從而形成正迴圈,但若布局的規模過大,投資量過大,包袱過重,運高成本極高,若盈利能力差更會造成失血過快,現金流斷裂的風險;若布局的規模不夠,則又會缺乏規模效應,市場競爭力不夠。因此最核心的關鍵還是打磨工藝、投入研發、提升技術從而提高良率和盈利能力。
落到最後,更為直觀且核心的就是能否拿到客戶訂單。襯底廠商關鍵在於盈利性,而盈利性又是由良率和訂單決定的,能賣的出去產品且能盈利才是硬道理。目前國內廠商天嶽先進、天科合達已成功供應英飛淩、博世等國際大廠。以天嶽先進為例,2021 年及之前,天嶽先進主要向無線電探測、資訊通訊行業廠商供應半絕緣型 SiC 襯底,2022 年公司實作將部份產能轉移至導電型襯底後,陸續與國家電網等多個國內客戶建立合作關系,並與英飛淩、博世集團等海外大廠簽訂長期合作協定,國內廠商進展飛速。
3. 外延:技術工藝裝置相對成熟,國產化進展較快
3.1. 外延技術相對較為成熟,外延爐是核心裝置
外延生長技術是碳化矽器件必不可少的環節。碳化矽外延晶片是指在碳化矽襯底的基礎上,經過外延工藝生長出晶格一致、高純度、低缺陷的特定單晶薄膜。由於采用昇華法制備的單晶襯底無法實作對載流子濃度的精密控制,且無法有效降低晶體缺陷,因此需要在襯底上生長高品質的外延層,可以消除襯底中的某些缺陷,使晶格排列整齊,即外延生長技術是碳化矽器件必不可少的環節,外延品質對器件效能影響極大。 現階段碳化矽外延制備主要透過化學氣相沈積(CVD)方法,核心裝置為CVD外延生長爐以進口為主。現階段 SiC 薄膜外延的方法主要包括:化學氣相澱積(CVD)、分子束外延(MBE)、液相外延法(LPE)、脈沖雷射澱積和昇華法(PLD)等。目前化學氣相沈積(CVD)是最為普及的 4H-SiC 外延方法。其優勢在於可以有效控制生長過程中瓦斯源流量、反應室溫度以及壓力,改變成膜環境,可以精準控制外延生長參數,具有重復性良好,裝置體積適中的優良特點。
高品質的碳化矽外延晶片生長受到外延生長過程中使用的CVD 外延爐、襯底等上遊裝置及材料的影響。國際上已經商業化量產的 SiC-CVD 裝置有義大利LPE、德國Axitron和日本NuFlare 產品,這三家公司也占據了國內市場。由於起步晚和產業化水平低,國產裝置在使用方便性、可調性、穩定性以及執行維護性方面與國外先進裝置相比存在較大的差距,重點需要提升溫場和流場的均勻性方面的技術。以芯三代、晶盛機電為代表的國內SiC-CVD裝置廠家,產品各項指標已經達到甚至領先國際先進水平,國產 SiC-CVD 裝置目前的重點是進入生產線接受大批次生產考驗。
碳化矽襯底缺陷較多,需嚴格控制缺陷工藝難度較大。碳化矽襯底缺陷較多,主要包括微管缺陷 (Micropipe) 、多型缺陷、劃痕缺陷包裹物缺陷、層錯缺陷、貫穿螺型位錯(TSD)、貫穿刃型位錯(TED)和基平面位錯(BPD)等。許多襯底缺陷會隨著外延生長延伸到外延層中,部份缺陷會轉換成外延缺陷,導致器件效能退化或直接失效。透過外延工藝最佳化可以有效降低或消除這些外延缺陷,從而改善器件良率。優質的碳化矽外延生長工藝不僅可以改進碳化矽襯底缺陷,還可以減少外延自身生長缺陷,大幅提升下遊器件良率。
3.2. 外延環節國產化水平較高,有上下遊向外延延申的趨勢
全球來看外延環節呈現雙寡頭壟斷,國內來看中國碳化矽外延國產化率水平不斷提高。頭部企業主要有 Wolfspeed(Cree)、DowCorning、II-VI、Norstel、ROHM、三菱電機、Infineon等,其多數是 IDM 公司,CR7 占據市場 90%份額。國內純外延產業化比較成熟的企業有天域半導體和瀚天天成,其已研制成功 6 英寸碳化矽外延片,且基本實作商業化。國內外在碳化矽外延水平上的技術差距相對較小,均滿足 3-6 英寸各種外延片的生產。目前各大廠商均在擴產8 英寸襯底產能。
國內外廠商紛紛擴產,且有上下遊向外延環節延申的趨勢。一方面,外延環節技術及工藝相對襯底較為成熟;另一方面,相較純外延廠商,襯底廠商向下遊外延延申可以直接為客戶提供外延產品,具有更強的客戶優勢,晶圓廠商向上遊外延延申可以縮短驗證周期,具有更強的驗證優勢。目前碳化矽產業鏈已經呈現出了上下遊紛紛向外延環節延申的趨勢。但我們認為長期來看,當碳化矽產業鏈具有一定產業規模時,純外延廠商作為代工廠為客戶提供代工服務,那些具有規模優勢的廠商仍然具備顯著的成本優勢。外延作為技術密集型和資本密集型行業,行業對技術和工藝要求較高,所需固定資產投入較大,固定成本分攤較大,因此規模優勢有望帶來成本優勢。
4. 器件及模組:「上車方顯英雄本色」
4.1. 晶圓制造環節技術難度僅次於襯底,需要使用特定裝置
碳化矽材料特性導致的器件制造難度高,仍需要不斷改進生產工藝。與矽基器件類似,碳化矽僅需要部份特定裝置的升級或新開發,但這些新增裝置又具有一定技術難度,可以這樣理解,矽基器件發展超過 70 余年技術水平十分成熟,而碳化矽產業化也不過20余年,沒有指路人可以參考,而其自身材料特性又造成了工藝改進慢的問題,我們此處所指的工藝是指能夠達到批次生產的水平。碳化矽器件制造環節與矽基器件的制造工藝流程大體類似,主要包括光刻、清洗、摻雜、蝕刻、成膜、減薄等工藝。不少功率器件制造廠商在矽基制造流程基礎上進行產線升級便可滿足碳化矽器件的制造需求。在此,我們僅對其需要改進或新開發的裝置進行探討:由於碳化矽硬和化學穩定性高的材料特性,需要對幹法刻蝕機進行升級。由於碳化矽具有很高的硬度和化學穩定性,碳化矽器件圖形的加工較為困難。一般采用具有較高的刻蝕分辨率、選擇性比較高的幹法刻蝕方法加工,同時采用較大的刻蝕功率。碳化矽幹法刻蝕機主要技術難點包括高潔凈抗腐蝕工藝腔體設計與制造、高效能電漿源技術等。目前國產化率水平較低,以海外廠商為主,海外廠商主要包括 Sentech、TEL、AMAT、Oxford 等;國內主要單位包括北方華創、中微半導體、中科院微電子所等。
由於碳化矽晶格難擴散的材料特性,需要新增高溫離子註入機,產業化難度較大。區別於矽可以采用擴散或離子註入實作摻雜,碳化矽晶格難擴散,摻雜需要采用更高的註入能量,一般註入能量在 300KEV,基至需要到 700KEV 以上,高能量的離子註入的工藝制造成本高、流片效率低。高能量的離子註入會造成註入區域的損傷,為了解決註入離子啟用問題,減少註入損傷,碳化矽註入一般需要在 500℃以上高溫條件下進行。目前主要廠商以海外為主,包括ULVAC、NISSIN、AMAT 等,國內裝置註入能量、束流大小、註入晶片溫度等技術指標與國外相差不大,在產能等方面有待提高。根據泰科天潤,高溫離子註入機的保有量是衡量碳化矽晶圓產能的關鍵,目前國內 20 台左右,價格在千萬級別,裝置交期十分漫長,需要10個月到1年的時間,因此國內部份廠商也是由於缺少高溫離子註入機而選擇代工模式。
此外高溫離子註入會造成損傷,因此需要高溫退火爐。離子註入後仍需進行高溫退火,才可以啟用註入離子。N 型摻雜的退火溫度一般需要大於 1200℃,P 型摻雜的退火溫度一般需要大於 1600℃。實作碳化矽高溫退火爐主要技術難點包括高溫爐膛熱場設計制造工藝,快速升溫、降溫與控溫技術等。國外主要廠商主要包括 Centrotherm、日本真空等。由於碳化矽具有雙元素,需要使用高溫氧化爐來制備柵極氧化層。柵氧工藝不得不面對碳原子的反應,會形成碳相關雜質,需要高溫氧化工藝,被業內成為皇冠級難度。與矽柵氧化工藝不同,碳化矽高溫氧化時需要通入特定工藝瓦斯促進碳原子的析出,增加了工藝的復雜性。主要技術難點包括無金屬加熱技術、抗氧化無汙染高溫爐膛設計與制造、高溫氧化工藝等。因此面臨矽產業無法借鑒,工藝需要摸案、裝置配套較局限,高濕爐易受汙染、長期穩定性差的難點。國外主要廠商包括 Centrotherm、東橫化學等。國內主要廠商為北方華創等。由於碳化矽材料較硬且脆,需要使用更為堅硬的背面減薄機。背面減薄機主要技術難點包括高硬度材料減薄厚度的精確測量及控制,磨削後晶圓表面出現損傷層、微裂紋和殘余應力,SiC 晶圓減薄後產生比 Si 晶圓更大的翹曲現象等。國外主要廠商包括日本不二越、Disco等,國內裝置主要差距在於產業化程度有待進一步提高。
4.2. 器件仍以海外廠商為主,國內廠商不斷跟進
目前,碳化矽器件的市場份額以海外廠商為主。2022 年意法半導體仍然居首,碳化矽功率器件營收增加到 7 億美元;英飛淩次之,Wolfspeed 居於第三(僅包括器件),安森美以2.6億美元的營收,超過了日本廠家羅姆晉級第四。部份原因在於安森美從碳化矽襯底、外延、裸片,再到單管和模組封裝測試完全垂直整合,而羅姆在單價更高的碳化矽模組,特別是車規產品較少。按照 CR5 中部份企業公布的數據,以及 01 芯聞公眾號的統計,2022年意法碳化矽功率器件的市占率低點為 37%,高點為 40%。英飛淩和 Wolfspeed 則占據了20%左右的市場。安森美緊隨隨後,份額為 14%。最後,根據數據來源的不同,羅姆市占率在7%-11%之間。
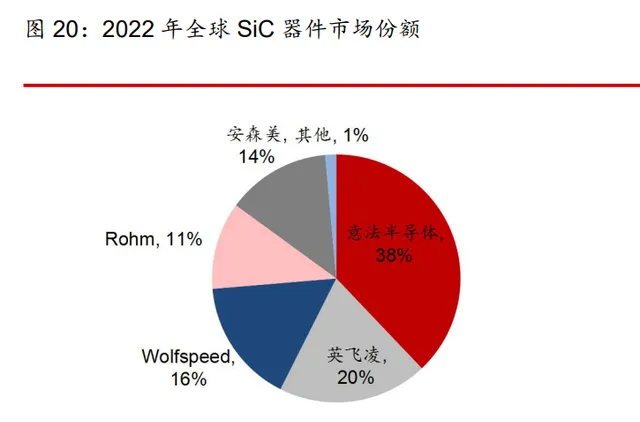
海外頭部大廠一體化趨勢明顯,透過自建或收購或合作等方式加快上下遊整合。頭部五家大廠除英飛淩外,均采用垂直整合的方式自建襯底產能。2023 年英飛淩與ResonacCorporation簽署了全新的多年期供應和合作協定,並於天科合達、天嶽先進簽訂了供應協定,充分保障襯底供應。其他大廠透過自建或收購或合作等方式加快上下遊整合,根據Evertiq的數據,近年來 SiC 行業內並購數量明顯增加,以美國為例,2006-2022 年間共發生9 起SiC企業並購案件,其中 7 起發生於 2018 年及以後。
國內廠商不斷跟進,相比海外大廠還有一定差距。目前,國產碳化矽二極體已經能夠穩定交付,整體產業鏈也較為完善,國內廠商在二極體、MOS 單管已具備一定價效比優勢。透過國產廠商的勤奮努力,碳化矽二極體成本不斷下降,在工業、光伏儲能等行業形成了廣泛地國產替代。根據碳化矽芯觀察調研,國內 SiC SBD 產品 2017 年的價格在4.1元/A左右,2020年下降到了 1.58 元/A,2023 年上半年國內廠家普遍報價在0.5-0.6 元/A。但在器件方面,仍與海外廠商有較大差距,器件技術水平要求最高的就是新能源汽車主驅逆變器,目前僅斯達半導、比亞迪半導體、芯聚能有碳化矽主驅功率模組成功上車,其他器件廠商上車的多為在OBC、DC/DC 上的套用及技術儲備。
4.3. 國產化上主驅還要經歷一段嚴苛漫長的歷程
國產碳化矽模組上車需要經過多輪嚴苛的可靠性測試,最短需要26 個月時間。一般碳化矽模組上車要經過兩個階段,第一個階段是產品在大量工業場景的驗證打磨,工業場景的要求相對沒有新能源車要求嚴苛,透過在大量工業場景,如充電樁、光伏逆變器等的大面積套用,透過小電流碳化矽 MOSFET 在工業化領域的規模化套用獲得反饋不斷打磨改進,而後進入新能源車的 OBC、DC/DC 等場景,積累大電流的碳化矽 MOSFET 的技術經驗,有技術成熟的大功率碳化矽 MOSFET 模組產品後才進入第二個階段的主驅逆變器的驗證上車,這又需要經歷拿到可靠性測試標準及多輪效能測試。目前備客戶所認可的功率半導體器件可靠性測試標準有兩種,即 AQG-324(針對模組)與 AEC-Q101(針對晶圓),分別代表著模組與單管兩種器件的測試要求;根據泰科天潤,效能測試要經歷 3 輪效能測試,保守估計最短也需要26個月時間,且毫無「僥幸」透過的可能。
盡管國內企業在 SiC 器件領域起步較晚,但面對全球市場快速增長,疊加國內企業在新能源車、光伏逆變器等終端品牌市場份額的逐步提升,中國企業已經切入了SiC二極體或較高導通電阻的 MOS 產品,滿足消費類產品、工業電源、車載充電機及小功率光伏組串式逆變器領域套用,之後逐步將產品叠代至低導通電阻 MOS,並補足模組封裝實力,未來有望逐漸透過低端車到高端車定點或深度繫結車企或幫助車企代工等方式,逐漸成為新能源汽車主逆變器碳化矽功率器件的供應商。
5. 全產業鏈齊心協力推進低成本、高品質、大批次的產業化
碳化矽材料、工藝、套用突破難度高,國內產業鏈尚未形成完整的閉環,需要全產業鏈齊心協力推進低成本、高品質、大批次的產業化。上遊材料層面產能不足、良率不足、產品缺陷多,又會影響到器件的可靠性和良率,這又會造成套用層面使用困難,套用層面沒有足夠的需求和數據能夠為上遊材料器件降本和技術工藝改進提供支撐。目前國內進展較快的在襯底和外延材料端,頭部廠商已進入海外大廠的材料供應鏈,但良率、高品質導電型、大尺寸等方面與海外廠商仍有一定差距;下遊晶圓、器件模組端相對進展較慢,國產廠商在工業領域已獲得較大突破,而進入新能源汽車主逆變器仍有一段距離,這需要全產業鏈齊心協力來推進低成本、高品質且大批次的產業化,這離不開上遊材料提高良率改進工藝,更離不開下遊器件模組,也離不開裝置廠的國產化降本。
碳化矽是產業趨勢:我們認為碳化矽的產業趨勢確定性不斷加強,隨著純電滲透率的提升,高壓快充技術逐漸成為中高端車的標配且向更低價格帶延申,一方面碳化矽功率器件在高壓快充等套用場景上本身具有更大耐高溫、耐高壓、耐高頻的效能優勢,同時碳化矽功率器件在消費者心中獲得了一定的產品認知;另一方面隨著各大廠商的加速擴產及提升技術水平,上遊襯底和外延材料端成本不斷下降,技術進步及規模效應帶來的價格的下降才是刺激碳化矽市場滲透的核心要素。
落實到投資層面:結合產業進展, 1) 從估值方面,我們認為可以按照市銷率進行估值。碳化矽產業是從0到1發展的行業,市場空間巨大,從拿到大批次客戶訂單開始,到確認營收,企業在這個過程中透過獲得訂單-叠代工藝-提高良率-提高盈利能力-獲得訂單的正迴圈反饋。2) 從各環節進展來看,我們認為各個環節的發展特征、目前水平、關註要點有所區別,核心關註產業趨勢和企業訂單情況。襯底及外延環節關註在下遊放量及盈利能力的提升,現在頭部襯底廠商已經進入了海外碳化矽大廠的材料供應鏈,說明國產襯底產品效能已經得到客戶的認可,後續追蹤訂單情況,但落實到自身盈利上,還要更加關註工藝改善、良率提升;外延國內廠商集中度較高,但有諸多上下遊企業切入後續關註競爭格局的變化及頭部企業的規模優勢;晶圓制造環節的核心關鍵在於高溫離子註入機的保有量,高溫離子註入機是限制晶圓制造產能的瓶頸;器件模組環節進入新能源車主逆變器供應的進展情況。
(本文僅供參考,不代表我們的任何投資建議。如需使用相關資訊,請參閱報告原文。)
精選報告來源:【未來智庫】。未來智庫 - 官方網站