2018年,全球拖拉機市場掀起了一場高功率化的熱潮。歐美和日本的幾大拖拉機巨頭紛紛推出了500馬力、600馬力甚至更高功率的產品,配備無極變速、動力換擋等先進技術,瞬間占據了市場的制高點。面對這樣的國際形勢,國內拖拉機制造商們也不甘落後,紛紛跟風生產大功率拖拉機,試圖借此在市場中分得一杯羹。然而,當國內企業忙於馬力的瘋狂增長時,真正決定拖拉機競爭力的核心技術卻被忽視了。為什麽國產拖拉機的故障率居高不下?為什麽看似強勁的大功率機型在田間地頭頻頻「趴窩」?
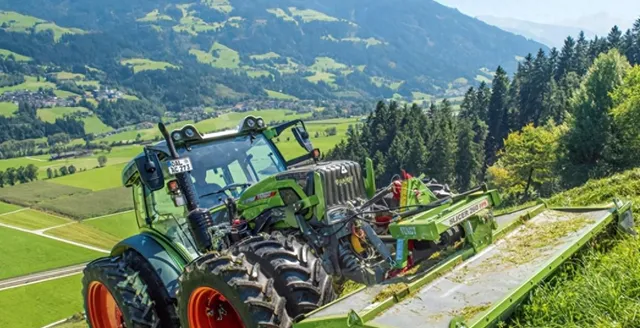
中國拖拉機產業的起步與成長
1959年,中國開始成批生產拖拉機,這標誌著中國農業機械化的初步發展。在這之前,農業生產基本依靠人力和畜力,機械化程度極低,生產效率難以提升。新中國成立初期,為了擺脫落後的農業生產方式,中國政府開始大力推動農業機械化。那個時候,國內缺乏相關技術和裝置,於是透過引進國外的先進技術和生產裝置,尤其是從蘇聯等社會主義國家引進成套技術,這成為了早期中國拖拉機生產的主要路徑。
最初引進的拖拉機型號多為蘇聯的「東方紅」系列,這些拖拉機因其強勁的動力和堅固的設計,被廣泛用於國內的農田作業。這一時期,工人們在工廠裏忙碌地組裝這些「舶來品」,從零件到整機的裝配都嚴格按照外國的標準執行。然而,在實際使用過程中,這些拖拉機並非完全適應中國的農業環境。由於土壤條件、作業習慣的不同,外國產的拖拉機在一些作業環境下頻頻出現問題,這促使國內技術人員對這些拖拉機進行試用和調整,以適應本土需求。
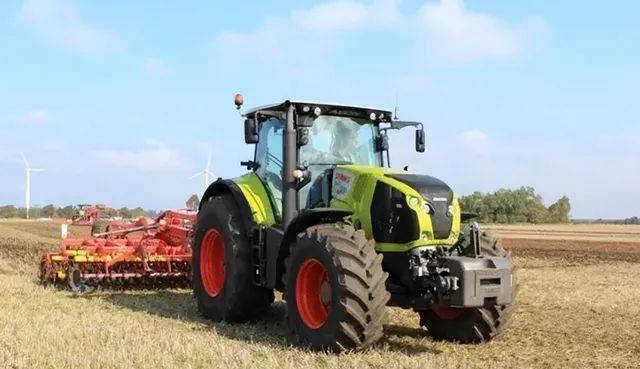
面對這些問題,國內的技術人員和工人們開始深入研究這些進口拖拉機的結構和原理。工廠裏的技術骨幹經常加班加點拆解研究,試圖從每一個零件的設計中找到改進的方向。在不斷的試用和研究過程中,他們逐漸掌握了這些拖拉機的基礎生產技術。為了提高技術水平,各地的工廠紛紛設立了技術攻關小組,許多機械工程師甚至自學外語,翻閱外國的技術手冊和資料,透過「邊學邊幹」的方式,逐漸摸索出一套適合中國實際情況的生產方法。
與此同時,國家也在不斷地鼓勵技術創新。技術人員在生產一線不斷提出改進建議,有的甚至在實驗室裏通宵達旦地進行各種新型零部件的測試和改造工作。許多老工人回憶,那段時間每天的工作都緊張而充實,拖拉機的生產和改進仿佛成了一場攻堅戰。在這些努力下,國產拖拉機的品質逐漸得到提升,工廠開始嘗試仿制國外的成熟機型,並逐步對這些機型進行適應力改良。
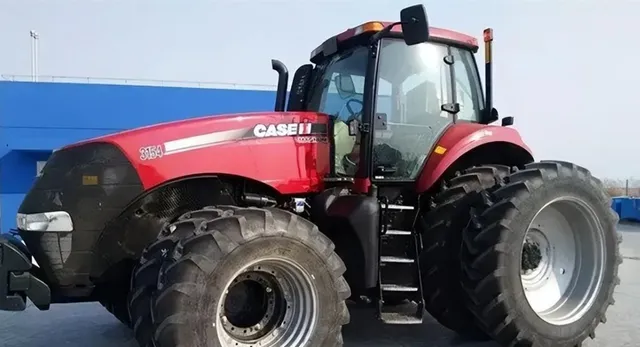
經過不斷的摸索和實踐,國產拖拉機的效能逐漸穩定,生產規模也逐步擴大。上世紀60年代,中國的拖拉機生產線已經能夠相對穩定地批次生產多種型號的產品。隨著生產規模的擴大,中國拖拉機制造逐漸實作了規模化和標準化生產。這些國產拖拉機雖然在技術上仍與國際先進水平有一定差距,但已經能夠基本滿足國內農業生產的需要,特別是在改善農田作業效率、減少農民體力勞動方面起到了不可忽視的作用。
技術差距的正視與改革開放的影響
改革開放後,中國的拖拉機產業迎來了新的發展機遇。隨著國家經濟的逐漸開放,國內企業有了更多機會與國外同行交流學習,這為中國拖拉機制造註入了新的活力。大量國外先進的機械制造技術、管理經驗和裝置被引入國內,國內拖拉機企業紛紛開始與國際知名企業進行合作,簽訂技術引進協定、進行技術轉讓,一些大型國企甚至直接從國外引進整套生產線。
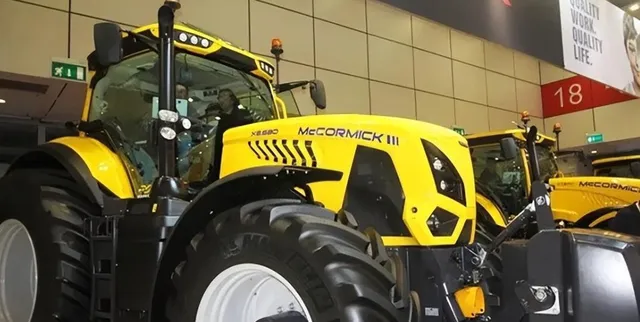
在上世紀80年代,各大拖拉機廠開始派遣技術人員前往歐美等已開發國家學習先進的制造技術。這些技術人員回國後,把學到的知識和經驗運用到生產實踐中,從產品設計、零部件加工到裝配線的最佳化,都進行了大量的改進。
然而,盡管取得了一定的進步,國內拖拉機企業在核心技術的掌握上仍顯得力不從心。尤其是在發動機、變速箱、液壓系統等關鍵部件的設計和制造上,國內企業仍依賴於進口技術和零部件。很多企業雖然能夠自行組裝拖拉機,但核心部件仍需從國外采購。這些高端零部件價格昂貴且供貨周期長,直接影響了國內拖拉機的成本控制和生產效率。同時,國產拖拉機在適應力、耐久性等方面與國外產品相比仍存在較大差距。
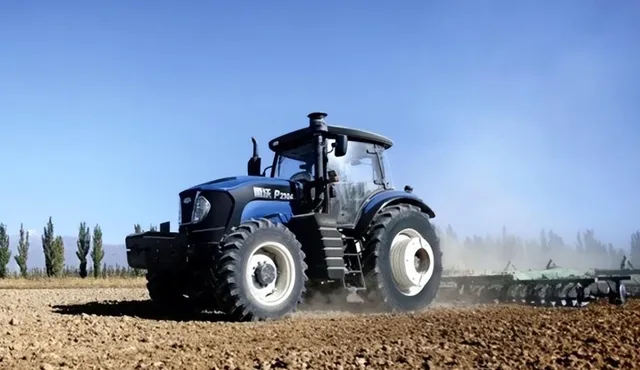
大功率化趨勢與國內拖拉機的應對策略
2018年以來,國際拖拉機市場的變化顯而易見,大型化、高功率化成為主流趨勢。歐美市場上,各大知名品牌紛紛推出了高達500馬力甚至700馬力的高端拖拉機,產品不僅在功率上遙遙領先,還配備了先進的電子控制系統、自動導航等智慧化功能,這些新技術顯著提高了作業效率和操作舒適性。
面對國際市場的這一趨勢,國內拖拉機制造商也不甘落後,紛紛跟風投入大功率拖拉機的生產。許多企業認為,只要能夠生產出高功率的產品,就能在市場上占據一席之地。於是,各家企業加大了對大功率拖拉機的投入,不少中小型制造商也開始爭相上馬高功率機型,甚至出現了多家企業幾乎同時推出200馬力以上拖拉機的現象。
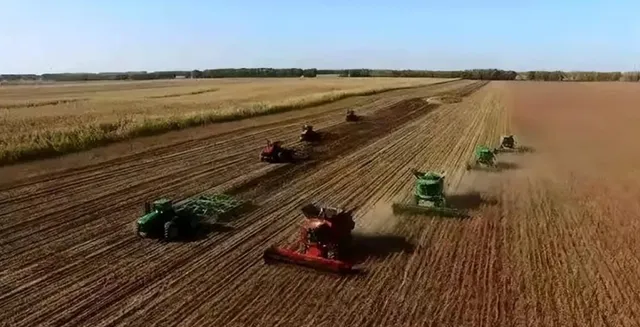
然而,問題也隨之而來。由於國內拖拉機制造商在核心技術儲備和產業鏈完善方面存在明顯不足,這種盲目追求大功率的做法很快暴露出諸多問題。首先是發動機、變速箱等關鍵部件的技術積累不足,導致國產大功率拖拉機在實際作業中故障頻發。特別是在動力輸出軸、液壓系統和傳動裝置等核心部位,問題尤為突出。這些零部件的品質和耐用性未能達到國際標準,直接影響了整機的可靠性和使用壽命。
實際使用中,拖拉機使用者反映最多的問題就是各種小毛病不斷,維修成本高昂。很多農場主在田間作業時常常遇到動力輸出軸故障或者液壓系統泄漏的問題,很多修理工表示,國產高功率拖拉機在設計和制造上存在諸多瑕疵,除了發動機效能相對穩定之外,其他部份幾乎都難以令人滿意。特別是齒輪、離合器等部件,磨損快、故障率高,嚴重影響了拖拉機的正常使用。這些問題的出現,與國內拖拉機企業的技術準備不足和產業鏈不完善密切相關。
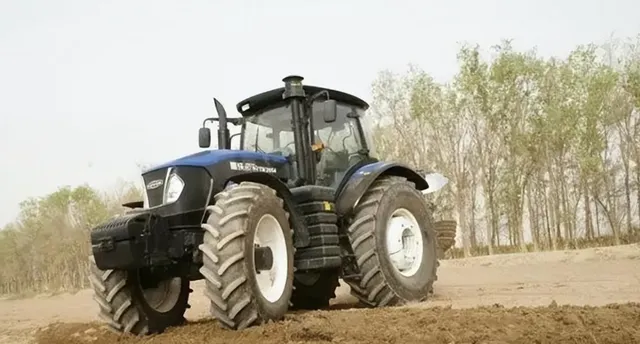
國內外技術差距的具體體現
從1990年至今,國內拖拉機的無故障使用時間一直遠低於國際標準。無論是小型拖拉機還是大中型拖拉機,國內產品的無故障使用時間雖然經過多次改進有所提升,但與國際先進水平仍存在顯著差距。根據相關數據,國內小型拖拉機的無故障使用時間大約在500個小時左右,而大中型拖拉機的無故障使用時間約為750個小時。相比之下,歐美國家的拖拉機在同一時期的無故障使用時間已經穩定在1500至2000小時之間,並且這一數位還在不斷重新整理。尤其是像美國的約翰迪爾、德國的福格爾等品牌,它們的拖拉機在各類農田作業中的可靠性和耐用性都是全球領先的,這直接反映出國際市場上拖拉機技術的差距。
歐美和日本的拖拉機不僅在基本效能上優於國產產品,在一些關鍵技術領域更是實作了突破性發展。例如,無極變速技術和動力換擋技術已經成為國際市場上的標準配置。這些在國外已經非常成熟的技術,在國內的普及和套用還處於起步階段。許多國產品牌的拖拉機仍然依賴於傳統的機械變速系統,缺乏對新技術的深入研究和套用,這使得國產拖拉機在國際市場上難以與外國高端產品正面對抗。
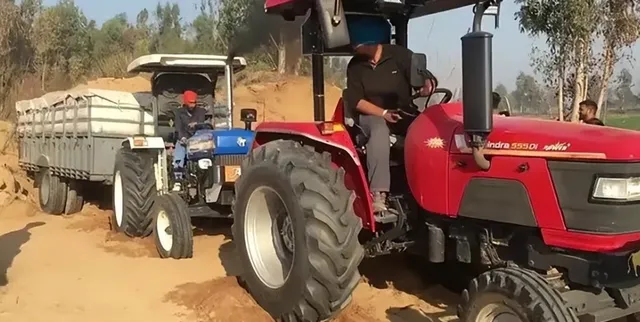
這種技術斷層直接影響了國產拖拉機的市場表現。在國際市場上,高端拖拉機產品的競爭不僅是效能和品質的比拼,更是技術水平胡創新能力的較量。國內的拖拉機制造商雖然努力透過改進設計、最佳化工藝來提高產品品質,但核心技術的缺失始終是一個難以逾越的障礙。比如,無極變速技術可以根據農田作業的需求自動調整速度和扭矩,這種智慧化的操作方式極大地提高了作業效率,同時也減少了對操作者的技能要求。但由於國內企業在這一技術領域的研究起步較晚,缺乏足夠的技術積累和人才儲備,這一技術在國產拖拉機上的套用還遠未達到國際水平。
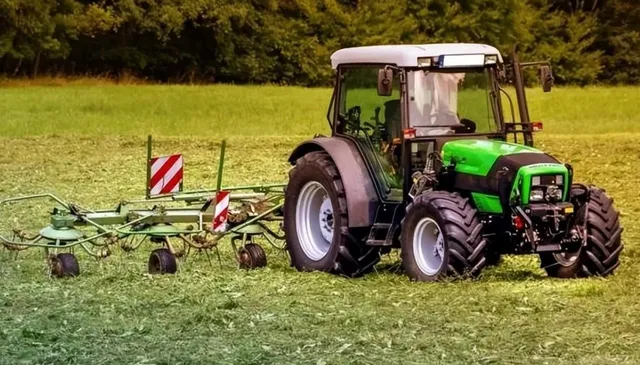
面對技術和市場的雙重挑戰,中國拖拉機制造業需要正視現有的技術差距。這不僅僅是簡單地引進國外技術或模仿先進產品能夠解決的問題,更需要國內企業在核心技術的研發上加大投入。只有不斷加大研發力度,才能逐步縮小與國際先進水平的差距。近年來,一些國內企業已經意識到這一點,開始增加研發經費的投入,同時積極引進高水平的技術人才,透過自主研發和技術引進相結合的方式,逐步提升自身的技術水平。
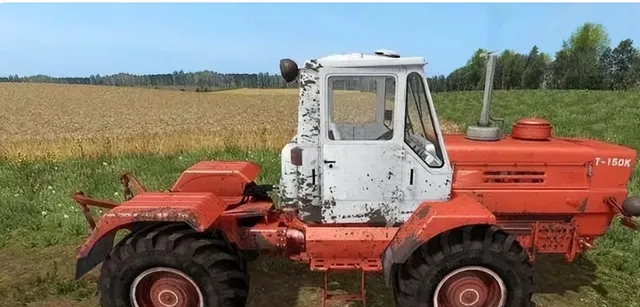
此外,市場需求的深入分析和精準定位也變得至關重要。中國拖拉機市場的特點在於農戶和農場主的需求多樣化,既需要高端大功率拖拉機,也需要適合小規模農田和丘陵山區的中小型機型。國內企業在產品開發過程中,必須充分了解市場需求,不僅要在高端領域進行突破,更要在中低端市場保持優勢。過去幾年,一些企業開始針對不同作業場景開發多元化產品,註重提升拖拉機在不同環境下的適應力,這種精準的市場定位在一定程度上提高了國產拖拉機的市場競爭力。
參考資料:[1]姚彬.從國產CVT拖拉機漢諾威首秀看中國農機強「芯」路[J].農機科技推廣,2024(1):61-63
