(报告出品方:招商证券)
【一、工业机器人——自动化的明珠】
工业机器人,那可是智能制造的代表呢。
工业机器人呢,是在工业领域使用的多关节机械手,或者是有多个自由度的机器装置。它主要的作用就是替代人工,去做那些柔性生产环节里的工作。它是一种凭借自身的动力以及控制能力来实现各种功能的机器。
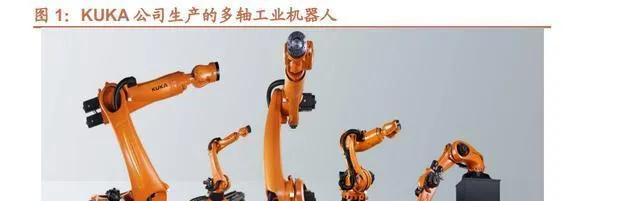
工业机器人现在已经有比较完整的产业链了,大概能分成原材料、核心零部件、本体制造、系统集成服务这些环节:最上游的原材料呢,主要是钢材、铸铁、铝合金,还有少量塑料制品和各种各样的电子元器件。核心零部件包含控制系统、伺服电机、精密减速器以及传感器等。工业机器人本体制造就是机器人结构和功能的设计与实现。系统集成就是依照客户的需求,进行生产线的设计和组装。
工业机器人有三大核心零部件,分别是控制器、伺服电机和减速器。工业机器人的性能和稳定性,在很大程度上取决于这三大核心零部件的性能与稳定性。核心零部件的生产技术壁垒比较高,很多关键技术都被少数公司垄断了,这样一来,机器人生产商在采购的时候,议价能力就不强,采购价格也就比较高。控制器就好比工业机器人的「大脑」,它负责把动作指令发布出去,再传递给执行机构。控制器由硬件和软件这两部分组成,硬件就是工业控制板卡,这里面包含一些主控单元、信号处理部分之类的电路;软件主要是控制算法、二次开发这些东西。伺服系统是工业机器人的「动力源」,通常是由伺服电机和伺服驱动器组成的,主要的任务就是把接收到的电压信号变成转矩和转速,从而驱动控制对象。减速器就像是工业机器人的「关节」,在核心零部件里,它的技术壁垒是最高的,在工业机器人的成本里占比也是最大的,主要的作用就是匹配转速和传递转矩。减速器有谐波齿轮减速器、摆线针轮行星减速器、RV减速器、精密行星减速器和滤波齿轮减速器这些类型,其中工业机器人主要用的是谐波减速器和RV减速器。
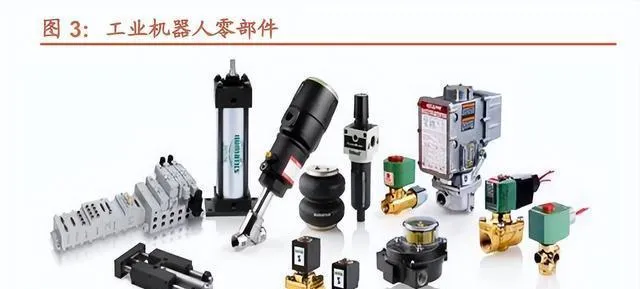
工业机器人能够依据机械结构、坐标形式还有程序输入方式等来分类。按照坐标形式的差异,工业机器人可被分成直角坐标型、圆柱坐标型、球坐标型、多关节型以及平面关节型等类型。在这些类型里,多关节型(也就是六轴工业机器人)和平面关节型(即SCARA型机器人)是最为常见的,在汽车、3C行业中被广泛运用。
2、工业机器人起源于美国,在日本繁荣发展。
工业机器人起源于美国,在日本得到蓬勃发展。1959年的时候,发明家德沃尔和约瑟夫·英格伯格合作造出了第一台工业机器人。这台机器人的结构和功能都特别简单,就只能搬搬重物。可是呢,美国失业率高,还有工会从中阻挠,工业机器人在美国就没能发展起来。日本呢,有着各方面的优势,就接了美国的班,成了工业机器人产业的带头人。现在日本已经有了完整的产业链,从上游的核心零部件,到中游的机器人本体制造,再到下游的系统集成。这里面最出名的公司,就要数「工业机器人四大家族」里的发那科和安川了,还有减速器方面的龙头企业哈默纳科和纳博特斯克。
中国工业机器人产业开始得比较晚。20世纪70年代的时候,科技部就把工业机器人列进科技攻关计划了,原机械工业部也带头在点焊、弧焊、搬运这些工业机器人相关的领域进行攻关。可那时候国内人口红利正旺呢,市场对工业机器人需求不大,所以工业机器人产业停滞了很长时间。到了2010年之后,市场又开始这个领域了,这时候日德这些制造强国已经有很完备的产业链了,在市场竞争里占了先。国内工业机器人不管是本体还是核心零部件,和国外大企业比都差得老远了。2010年之后,国内工业机器人产业才全面发展起来。现在呢,国内工业机器人还是以本体制造组装为主,很多零部件还得大量进口,产品主要也是在中低端市场。
3、协作机器人、特种机器人还有人形机器人。
协作机器人更安全,也更适合未来商用、家用的环境。工业机器人因为技术发展慢慢变得小型化,于是就分化出了协作机器人,这种机器人安全、灵活,还能与人协作。在机器人应用的下游行业里,汽车行业是20kg以上的应用场景,家电和3C行业大概是4kg,半导体行业在12kg左右。在轻负载的工作条件下,安全性有了保证,这样就能让机器人和人在同一个空间协同工作,协作机器人就这么出现了。
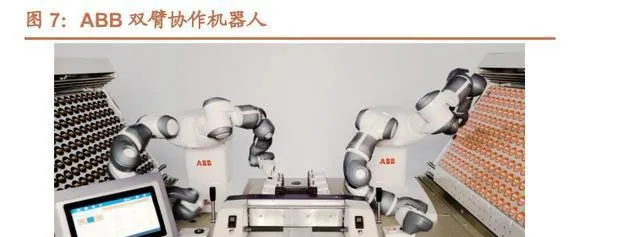
协作机器人和工业机器人,最大的差别就在安全性上,碰到障碍物的时候它能自己停下来。现在好多公司都在研发环境感应技术呢,已经有试用的机型能够做到在碰撞之前就停止运行了。还有其他的不同之处,像应用场景不一样,工业机器人的精度更高,末端速度是7.8m/s,负载也大;协作机器人呢,更看重灵活性,对编程的要求比较低,还能进行拖拽示教(不过精度低一些)。
特种机器人:特殊高危场景的应对之策。特种机器人就是除了工业机器人、公共服务机器人和个人服务机器人之外的机器人,主要用在专业领域,通常由经过专门训练的人员操作或使用,用来辅助和/或代替人完成任务。2021年,特种机器人的销售额在全球机器人市场占比为28.17%,在国内机器人市场占7.93%。特种机器人的分类:(1)按行业分:农业机器人、电力机器人、建筑机器人、物流机器人、医用机器人、护理机器人、康复机器人、安防与救援机器人、军用机器人、核工业机器人、矿业机器人、石油化工机器人、市政工程机器人以及其他行业机器人。(2)按功能分:采掘、安装、检测、维护、维修、巡检、侦察、排爆、搜救、输送、诊断、治疗、康复、清洁等。(3)按使用空间分:地面机器人、地下机器人、水面机器人、水下机器人、空中机器人、空间机器人和其他机器人。(4)按运动方式分:轮式机器人、履带式机器人、足腿式机器人、蠕动式机器人、飞行式机器人、潜游式机器人、固定式机器人、喷射式机器人、穿戴式机器人、复合式机器人以及其他运动方式机器人。
人型机器人是那种想要模仿人类的样子和行为的机器人,被看作是机器人领域里最顶尖的存在。大家都知道,人型机器人的研发挑战难度是最高的,对规划、控制和感测这三个基础要素所对应的设备要求特别高。特斯拉的首席执行官马斯克说,Tesla Bot有希望在2023年开始生产,它会被用来弥补劳动力不足的情况。人型机器人现在主要有这么几种技术路线:(1)以本田Asimo为代表的传统电控加上控制方法。在控制这一块呢,是通过力控和位置控制来实现的,用的是传统电机驱动和传统机械结构,本质上就和意大利IIT的iRonCub与力控结合起来差不多。(2)以波士顿动力Altas为代表的液压驱动加上控制方法。液压驱动能让人型机器人的运动能力达到极致,目前在运动能力方面是最强的。(3)以Agility的Cassie为代表的新方式,这种方式是重心往上移,腿很细,上半身比较大,能够节省功耗。
【二、安装量已居第一,自主品牌正迎头赶上】
我国成了机器人生产和消费的大国,2021年全球机器人市场规模超千亿。
2011年到2020年,工业机器人的安装量每年增速都能保持在10%以上。有劳动力被替代和制造业升级这两个因素支撑着,所以长期来看,向好的趋势不会改变。中国在这十年里,复合增速超过了25%。2013年的时候,中国就超过日本,成了世界上使用机器人最多的国家。在将近20年的时间里,中国的机器人安装量占全球的比例从0%涨到了44%。要是按照我国机器人单台价格中位数15万元来估算,2021年全球的市场规模有1200亿元。2020年疫情被控制住之后,国内外制造业的需求一下子爆发了,我国的机器人行业就进入了一个为期两年的增长期,月产量平均超过了3万台。不过在2022年4月之后,因为长三角地区有疫情,就陷入了负增长状态。
我国的机器人密度在逐步提高,不过和发达国家比起来还是有差距的。IFR的数据显示,2019年全球工业机器人平均每万人的保有量是113台,在这当中,新加坡的数量是最高的,达到了每万人918台,日本是每万人364台,中国是每万人187台。从每万个制造人员的使用量来看的话,要达到日本的水平,还有一定的空间呢。
机器人下游应用还是以电子和汽车为主,锂电和仓储的增长速度比较靠前。从绝对数值来讲,工业机器人在早期主要被用在汽车制造业的焊接、喷涂线上,后来小型工业机器人(包括SCARA、DELTA)因为成本低,在3C行业很快就替代了人力做重复劳动。最近几年,受「双碳政策驱动」,锂电池板块迅速扩大生产规模,在锂电池生产工艺里的叠片、焊接、封装这些工序,由于对一致性有要求,所以用机器人的情况比较多,后面的检测、组装和PACK环节主要依靠机器人来做比较重的负载抓取、搬运工作,以此提高自动化水平。仓储环节主要是由AGV、中大型堆垛机器人构成的。
我国工业机器人进出口的均价差距很大,在高端机型上这种差距更显著。现在,国产机器人的核心零部件,像控制器、伺服系统、减速器之类的,其精度和一致性都比进口品牌差。单个小细节上的误差累积起来就成了整体的误差,这样一来,国产品牌很难跟外资机器人竞争,只能在价格上妥协。22Q1的时候,喷涂机器人进出口差价有4.1万美元,多功能机器人进出口差价达4500美元。
2、高端市场被四大家族把控着,国产的双星最先冲出来了。
「四大家族」在全球的市场占有率超过了50%,在国内也超过40%,而自主品牌埃斯顿和汇川技术各自占4%。「四大家族」延续着之前在机床、伺服系统、焊接设备方面的技术优势,在机器人领域依然处于领先地位。国内的埃斯顿和汇川技术这两个品牌发展得很快,2021年的销量都突破了1万台,进入了中国工业机器人销量的前十名。埃斯顿以6关节机器人为主,汇川技术以SCARA机器人为主,现在它们都朝着多种负载、全产品系列的方向发展,很有希望成为真正能替代「四大家族」的国产机器人品牌。
实际积累know - how应用方面是一道难关。机器人行业有自身周期和成长这两种属性,其周期属性和通用自动化以及中国自身的信用周期有关,而成长性主要源于制造业升级和劳动替代。后疫情时期,下游各细分行业里的龙头企业不会因短期经济周期的波动就暂停内部产线的升级,像宁德时代这样的锂电池厂商扩大生产也正搞得红红火火,现在「四大家族」机器人的订单已经排到2023年中之后了。「四大家族」机器人供不应求,这就给国产龙头品牌提供了进入高端下游应用场景的机会。以前国产机器人品牌的应用场景比较单一,都是些长尾的,缺乏长时间完整生产线自动化know - how的积累,在高端应用场景常常难以满足全方位的需求,所以只能以工作站的形式在特定工位进行人力替代。拿锂电池行业来说,这个行业既涉及焊接,又涉及小工件的高速节拍搬运,还涉及大工件的重负载搬运,这就需要全品类的焊接机器人、堆垛机器人、SCARA机器人来配套。就拿电池盒焊接工序来说,铝合金焊接得用搅拌摩擦焊,这就需要重型负载机器人搭载径轴搅拌器,施加很强的压力,配合高温把材料融化然后再进行摩擦焊,而且在自身做圆周运动的时候还要保持整体路径是直线。
埃斯顿和汇川技术有着相似的发展轨迹,埃斯顿靠控制器,汇川技术靠伺服系统,它们的快速响应能力有助于国产替代。埃斯顿在机器人发展方面和发那科类似,它有20年折弯机床数控系统的开发经验,还有15年折弯机床伺服系统的经验,后来收购了Trio和Cloos,完善了控制系统和焊接相关技术。汇川技术有变频器、伺服系统、编码器、PLCHMI、视觉系统等一系列产品,能全面理解运动控制,而且具有很高的一致性和稳定性。除了能自主生产机器人的核心零部件,在与客户配合的时候,埃斯顿和汇川技术在可支持的人员数量和反应速度上,比外资品牌更有优势。国产品牌一直在丰富自己的技术和产品种类,从那些比较小众的非标准场景慢慢向大批量的标准化场景应用转变,取代外资品牌。(报告来源:未来智库)
【三、控制器、伺服电机、减速机,三核心零部件决定机器人性能】
三核心零部件的成本占比达70%。
工业机器人有控制器、伺服系统、减速器这些核心零部件,这些零部件决定了工业机器人的精度、稳定性、负荷能力等关键性能指标。在产业链里,核心零部件的壁垒是最高的,它在机器人成本里占了70%。控制器就好比工业机器人的「大脑」,大概占总成本的15%;伺服系统如同工业机器人的「动力源」,通常占总成本的20%;减速器就像是工业机器人的「关节」,它一般占总成本的35%左右。
2、控制器,这可是工业机器人的大脑啊。
控制系统是机器人性能的关键所在。它接收别的组元传来的信号,按照编好的程序处理之后,再给各个组元发指令,这样就能控制各个组元运行了,它可是工业机器人达成特定功能的核心单元呢。
控制系统在结构上常用的有三类,一是以单片机为核心的,二是以可编程控制器(PLC)为核心的,还有就是基于工业个人计算(IPC)+运动控制器的机器人控制系统。IPC+运动控制器这种控制系统有运行稳定、通用性强、抗干扰能力强等优点,正在慢慢变成工业机器人控制系统里的主流。
工业机器人的控制系统,主要有硬件和软件这两部分。硬件说的就是工业控制板卡,软件主要包含控制算法、二次开发这些。本体厂家自产核心技术的情况比较多。控制系统咋样,能集中体现一家工业机器人厂商的设计理念。那些比较成熟的机器人厂商,一般都是自己开发控制器和伺服系统的,这么做是为了确保机器人的稳定性和技术体系。所以啊,全球控制系统的市场份额跟工业机器人本体的情况差不多。
未来工业机器人发展肯定会越来越智能化,各本体制造商之间的差异以后也会越来越大,这种差异主要就表现在控制系统上。国内厂商的技术慢慢积累、不断进步,现在控制系统和国外产品的差距在逐渐变小。国内比较有名的工业机器人生厂商,像埃斯顿、华中数控、新时达、广州数控、汇川技术这些公司,都自己研发了控制系统。而且还出现了一批专业做控制系统服务的企业,像固高科技、英威腾、卡诺普等。
3、工业机器人的动力来源是伺服系统。
工业机器人主要的动力来源是伺服系统,它主要包含伺服电机、伺服驱动器、编码器这三个部分。「伺服」的意思是「跟随」,就是根据指令信号对位置、速度或者转矩进行跟随控制。2021年的时候,我国伺服系统的市场规模大概是189亿元,正处于快速发展当中。
伺服电机:每个关节都会安排一个电机。现在小型交流伺服电机用得比较多,也有一些用的是直流电机。直流电机功率更大,这是它的优势,不过交流电机结构更简单,后续的保养和维修也更便利,所以越来越受人喜爱。伺服驱动:伺服驱动器的主要作用是接收编码器信号来修正调整,接着按照指令发出对应的控制电流。驱动器和伺服电机组成闭环控制系统,驱动器依靠编码器送回的数据来进行控制和修正工作。伺服驱动器由位置控制单元、速度控制单元和驱动单元这三部分组成。编码器:为了实现闭环控制,要在电机输出轴的同轴位置安装编码器,电机和编码器同步转动,电机转一圈编码器也转一圈,在转动时把编码信号送回驱动器,驱动器依据编码信号判断伺服电机的转向、转速和位置是否正确,从而调整驱动器输出电源的频率和电流大小。
伺服系统这块,日系占主导地位,欧美排在后面,国产的跟在后面发展。在我国,工业机器人用的伺服系统还是日系占主导,不过国产的也有了些小突破,汇川、禾川、埃斯顿加起来占了18.5%。
伺服电机的市场规模一直在扩大,国产品牌所占的份额也在快速增加。现在,外资品牌在我国伺服电机市场占了65%的份额,主要是日本和欧美品牌。以前外资品牌长时间把控着市场,近年来,随着我国工业自动化进程加快,不少国产品牌迅速发展起来。2021年上半年,国产品牌汇川技术的市场份额占比首次排到第一,达到了15.9%。中国台湾的台达和德国的西门子在光学仪器方面的占有率也比较高。
我国的伺服电机和日系、欧美品牌相比还是有差距的,主要体现在这几个方面:大功率的产品少、小型化程度不足、信号接插件不稳定、没有高精度的编码器。而这些方面正是国内伺服系统以后需要攻克的主要方向。
4、减速器呢,它能减速还能增矩,以此来确保精度。
工业机器人的「关节」是减速器,它主要的作用就是匹配转速和传递转矩。在核心零部件里,减速器的技术壁垒是最高的,主要也是用来匹配转速和传递转矩。减速器有多种分类方法:按传动类型来分,有齿轮减速器、蜗杆减速器、行星减速器、摆针减速器等;按传动级数分,有单级减速器、两级减速器、多级减速器;按布局方式分,有展开式减速器、分流式减速器、同轴式减速器等。
要减速并且增加距离,把转速和扭矩协调好,这样才能保证精度。工业机器人是靠伺服电机来驱动的,不过呢,伺服电机转速快、扭矩小,这和工业机器人关节所要求的转速慢、扭矩大是相互矛盾的。伺服电机自己虽然能调速,但在低频运转的时候容易发热,还会有低频振动的情况,这样就没办法确保工业机器人高精度地工作了。减速器能让伺服电机在合适的速度下运行,还能把转速精确地降到工业机器人各个部位所需要的速度,在提高机械体刚性的同时,输出更大的力矩,提高重复定位的精度,从而执行那些重复又精准的动作。
谐波减速器是咋工作的呢?把波发生器放到柔轮里的时候,柔轮就会跟着波发生器的形状变成椭圆。波发生器一转起来,柔轮开口的地方就会有径向的变形,为啥呢?因为这时候柔轮是椭圆的,而且柔轮的齿数比钢轮少(一般少2个齿),柔轮就只会在两个长直径的地方咬合。波发生器转的时候,柔轮和钢轮咬合的地方会移动,由于柔轮和钢轮齿数不一样,波发生器每转180度,柔轮和钢轮咬合的位置就会变一个齿。减速比的计算公式是:(柔轮齿数 - 钢轮齿数)/柔轮齿数,要是结果是负的,就说明是反向运动,要是正的,就是同向运动。比如说,有个谐波减速器,柔轮是100齿,钢轮是102齿,那这个减速器的减速比就是 -1/50,也就是说输入端的波发生器和电机转50圈,柔轮输出端就会反向转1圈。
RV减速器是咋工作的呢?外壳的内环圈里装着圆柱形滚针(Pin),RV齿轮做偏心运动的时候,滚针就会跟摆线形的RV轮齿啮合或者脱离,这样能让多组RV轮齿和滚针同时啮合,负载能力就提高了。RV齿轮的齿数比滚针少1个,要是偏心轴转一圈,外壳(Case)固定住的话,RV齿轮就会和输入轴同向转1个齿的角度。输出端可以是传动轴(Shaft)或者外壳。外壳固定的时候,传动轴就是输出端,输出方向是同向;传动轴固定的话,外壳就是输出端,输出方向就相反了。把固定部件和输出部件换一换,传动比就不一样了。谐波减速器适合小臂,RV减速器适合大臂,它们相互补充。谐波减速器有不少优点,单级传动比大,体积小、重量轻,运动精度高,在密闭空间和有介质辐射的工作环境里也能正常工作,所以在机器人小臂、腕部、手部这些地方优势比较明显。RV减速器的传动比范围大,精度比较稳定,疲劳强度高,刚性和扭矩承载能力也更高,在机器人大臂、机座这些负载重的部位有优势。现在这两种减速器适用的领域不一样,还不能互相替代。一般来说,一套六轴多关节机器人得有4套RV减速器和2套谐波减速器;一套SCARA机器人包含4套谐波减速器;一套直角坐标机器人需要3套RV减速器和1套谐波减速器;DELTA机器人的电机装在固定基座上,需要1套谐波减速器。
和其他三种减速器比起来,谐波减速器个头最小,分量最轻,减速比是最高的。跟传统的斜齿轮减速器、行星齿轮减速器作比较的话,要是输出力矩一样,谐波减速器的体积能少2/3,重量能轻一半;在相同的空间里,谐波减速器最多能把减速比提高差不多30倍。所以给设备挑减速器的时候,得先看重精度,再根据需要的负载能力、空间、成本之类的条件来筛选。拿机器人来说,机器人对定位和重复定位的精度要求很严格,差不多只用RV和谐波减速器。常见的工业机器人在基座和大臂上用RV减速器(它能承受的力矩负载最多到8000N·m),在中小臂上用谐波减速器(能承受的力矩负载在1500N·m以内);负载比较轻(20kg以下)的机器人都用谐波减速器。目前RV减速器和谐波减速器适用的范围不一样,还不能相互替代。
日本厂商占据了全球超过85%的减速器市场份额:全球工业机器人减速器的市场集中程度很高,在RV减速器方面,日本的纳博特斯克处于垄断地位;在谐波减速器领域,日本哈默纳科处于垄断地位,这两家企业加起来占全球市场的75%左右。因为技术壁垒非常高,所以在工业机器人本体制造环节,对减速器环节的议价能力很弱。
【四、机器人行业发展的宏观背景】
日本,这个被称为「机器人王国」的国家。
日本有着完整的工业机器人产业链,从核心零部件,到本体,再到系统集成,整个产业链完备,而且在每个环节都位居世界前列。日本有好些世界著名的机器人公司,像哈默纳科和纳博特斯克,那可是减速器行业的绝对老大。这两家公司分别制定了谐波和RV的行业使用标准,在机器人领域,它们加起来的市场占有率超过75%,纳博特斯克的市占率超60%,哈默纳科在15%左右。发那科是数控系统方面的世界第一,和伺服电机的龙头企业安川电机,在工业机器人「四大家族」里占了两席。日本掌握着最多的工业机器人技术专利,在工业机器人的关键技术上绝对领先。除了像涂装轨迹规划技术等少数小方面,中国能和日本不相上下外,其他的技术基本上都被日本紧紧掌控着,在谐波减速器、RV减速器、电焊钳以及焊缝追踪这四个领域,超过70%的专利都归日本所有。
日本的机器人发展是从模仿开始的,后来慢慢走向引领地位。工业机器人最早出现在美国,而且在很长时间里,美国在技术方面一直是绝对领先的。1967年,川崎重工引进了日本第一台尤尼梅特(Unimate)工业机器人,到了1968年就仿制出了自己的工业机器人。由于国内劳动力不足、下游产业需求强劲、有政策扶持等原因,日本工业机器人行业在30年里就从模仿发展成了引领者。
。
经济快速发展,人力不够用了。
二战之后,日本的经济开始起飞了。国内搞了民主改革,石油价格又低,再加上美国在战略上扶持等因素,日本经济很快就恢复了,1951年就恢复到战前的水平了。1960年到1980年这段时间,日本经济发展得特别快,GDP增长速度最高的时候能达到25%呢。1965年的时候,日本的国民生产总值在世界上排第五名了,1968年又超过了西德,成了仅次于美国的经济大国。不过,这时候日本的劳动力开始不够用了。1960年到1980年,日本名义GDP的复合增长速度达到了14.6%,实际GDP复合增长速度是6.7%,可是劳动人口的复合增长率只有1.1%。经济发展得快,产业又不断扩张,对生产力的需求很旺盛,可劳动人口数量满足不了这么大的生产需求。当时日本的失业率特别低,60年代很长时间里,失业率甚至比自然失业率(1.5% - 2.5%)还低,而且在60 - 80年代一直都保持着比较低的失业率。当时日本招工的岗位比找工作的人还多,劳动力不够就大大提高了劳动者讨价还价的能力。同时呢,日本的人口增长率从70年代开始就一直比较低,人口增长率低就意味着劳动力短缺这种情况会一直持续下去,如果还一直用劳动密集型的生产方式,以后劳动力的供应就会一直不足。
用人成本因为劳动力短缺而快速上涨,机器人就随之发展起来了。按照经济学原理来说,市场上供不应求的话,直接就会让卖方的价格升高,日本制造业在1955年到1980年期间平均薪资大幅增长,这也从侧面证明了这个原理。要注意的是,在1965年到1975年期间,制造业薪资的复合增长率达到了16.55%。就在这个时期,日本的工业机器人从摇篮期发展到了实用期。
汽车行业来推动。
日本的汽车行业发展得特别快。在20世纪60年代,日本汽车业就进入快速发展阶段了。1960年的时候,日本一年生产的汽车才48万辆,这个产量跟美国、西欧那些主要的汽车生产国比起来,差得可远了。等到1967年,日本汽车年产量就超过300万辆了,一下子就超过德国,成了世界第二大汽车生产国。到了1980年,日本汽车年产量达到1000万辆,这就成了世界第一大汽车生产国了。20年的时间,汽车产量增长了20多倍,复合增长率达到16%。
工业机器人早期应用靠汽车行业撑着。汽车行业里,工业机器人用得最早、最广泛,应用能力也最强,其机器人密度常常是其他行业的4倍还多,就算到现在,汽车行业还是工业机器人使用最频繁的行业。汽车产品对尺寸、质量、精度和组装要求高,得有高质量、大规模的生产力,而且生产过程中会有危险、高温等让人受不了的工作环境,工业机器人就能很好地取而代之。汽车生产厂家规模大,现金多,有经济实力搞「机器换人」。另外,当时汽车行业竞争很激烈,用工业机器人能大幅降低人力成本,提高产品质量,竞争力也更强。日本的汽车厂商跟其他厂商比起来,又想快速扩张,又面临劳动力不够用的矛盾,所以更愿意引入工业机器人。日本的汽车行业和工业机器人行业互相成全。1970年到1980年这10年,日本汽车产量的复合增长率是7.6%,工业机器人产量的复合增长率是30.8%,这两个行业的高速发展时期基本是重合的。汽车厂商有钱,就像「金主」一样,解决了工业机器人行业发展初期缺钱、入不敷出的问题。工业机器人呢,也回报了汽车行业,提供了高效的生产力,解决了汽车行业劳动力不够的问题。发那科就是靠和美国通用合作,用它的投资完成了技术升级的。
(3)政策帮扶。
日本弄出好多扶持政策来鼓励工业机器人行业发展。一说到政策扶持,大家就容易想到中国,咱们国家常常因为有不少市场扶持政策而被人挑毛病。可实际上呢,差不多所有的都会对本国重要产业采取一定的保护和扶持措施。日本在工业机器人产业发展的早期就出台了不少政策来扶持:银行会给优惠的低息资金,鼓励大家集资成立长期租赁机器人的公司,这公司买了机器人之后长期租给用户,使用者每个月只要付很少的租金,这就大大减少了企业买机器人要花的钱;把计算机控制的示教再现型机器人当作有特别折扣优惠的产品,企业除了能享受新设备通常的40%折扣优惠之外,还能再得到13%的价格补贴。另外,国家还出钱给小企业做机器人知识培训和技术指导啥的。
工业机器人行业很需要适当的补贴,这意义可不小。在日本,工业机器人刚起步的时候,技术还没成熟呢,实际用的时候问题不少,像美国通用公司第一次用工业机器人就失败了。所以刚发展的时候,这个行业特别需要包容和照顾,适当补贴能让这个产业信心大增。从采购工业机器人的企业角度说,有补贴就降低了使用机器人的成本,投资回本的时间也缩短了,这样就刺激了工业机器人的消费。从生产机器人的企业角度看,补贴能给工业机器人带来比较稳定的收入,解决了前期研发投入大的问题,还能推动行业技术发展进步。我们简单算了下补贴力度对投资回报周期有啥影响。因为没有1980年工业机器人的价格数据,我们就用1996年日本进口工业机器人的均价(1500万日元/台)来代替1980年的价格计算。按照当时汽车行业的工作效率,每台工业机器人能替代6个劳动力,当时工人平均年薪是80万日元。经计算,如果没有补贴,工业机器人的投资在8年使用年限里收不回来,也就是说买工业机器人来换人是不理智的。通过敏感性分析发现,人均工资越高、补贴力度越大,投资回收周期就越短,买工业机器人的意愿就越强。当机器人能替换6个劳动力、补贴达到40%的时候,机器人的投资年限能缩短到6年。补贴的存在直接影响了人们购买工业机器人的意愿。
在中国当下,机器换人的性价比和当年日本比起来已经提高了很多。一个普通的6轴焊接机器人大概15万元,再加上系统集成配套的话,最多30万元。通常一个焊接机械臂能顶3个熟练焊工,熟练焊工工资8到10万元。简单算一下就知道,企业投一个6轴机器人,差不多1年就能回本,性价比相当高。(报告来源:未来智库)
(4)外在因素
日本制造业在生产效率上追求极致是被石油危机逼的。1973年「石油危机」爆发,原油价格一下子从每桶3美元涨到10.6美元。日本缺石油资源,石油危机一来,制造业的生产成本猛增。石油价格和人工成本都在疯涨,在这种两边夹击的情况下,提高生产效率成了唯一的办法。这个时候,工业机器人正好能满足制造业的需求。
美国对日本存在贸易逆差,这使得日元贬值。就像现在一样,20世纪80年代初,美国财政赤字猛增,对外贸易逆差也大幅上升。美国打算让美元贬值,好提升产品的出口竞争力,从而改善国际收支不平衡的状况。1985年,美国、日本、联邦德国、法国和英国的财政部长以及中央银行行长在纽约广场饭店开了个会,达成了有名的「广场协议」。之后,不到3个月,美元兑日元从1:250降到1:200,跌幅达20%。1987年时,美元兑日元贬值到1:120。日元大幅升值后,日本出口的价格优势就没了。
贸易战对制造升级的需求影响不大。「广场协议」前后,美国搞了好些贸易保护措施,像钢铁、彩电、汽车还有半导体行业都涉及到了。日本应对的方式基本就是消极地限制出口。但美国这些贸易保护手段,没挡住日本工业机器人产业发展起来。20世纪70年代美国针对彩电、1981年针对汽车行业的贸易战,对日本工业机器人没产生实质影响。能发现,1987到1990年的时候,日本工业机器人的订单量还在快速增长呢。我们觉得,这是因为日本的工业机器人大多是在本国用,出口到美国的比较少。再有,工业机器人属于资本投入,买方想不想买主要看投资回报率。要是工业机器人单位产出成本比人工成本低,那对工业机器人的需求就比较固定。贸易战对生产成本影响小,对企业购买工业机器人的意愿影响也不大。
中国,是「后起之秀」。
就像70年代的日本似的,中国现在也有劳动力不够、成本提高等不少问题,这两者特别相似。正是这些相似的情况,使日本成了现在的「机器人王国」,也让中国工业机器人产业有了无限的潜力。
(1)劳动力短缺,经济快速增长遇阻。
自改革开放以来,我国经济发展就驶入了快车道。1979年到2013年期间,我国GDP的平均增长率是9.8%,可世界同期只有2.8%。这几年,我国经济的增长速度跟前些年比是慢了些,但还是保持着比较高的增速呢,2019年我国GDP增速达到7.31%,2020年因为疫情影响,增速降到了2.74%。在经济高速增长的时候,我国制造业劳动力相对不足的问题慢慢就显现出来了。单从制造业从业人员的数量来看,2013年起我国制造业从业人数就开始减少了,从最高时候的5258万降到了3806万,少了1452万人。近年来不断增加的老龄人口比例是未来劳动力人口短缺的一个先兆。2020年,我国老龄人口比例达到13.5%,而且这个数据以后还会随着时间不断上升。同时,国内的人口增长率这几年一直保持在0.5%左右。老龄人口比例持续上升和人口增长率长期较低,这就意味着国内劳动力短缺的问题会变得更严重。
制造业里干活的人所占的比例在下降呢。国内劳动力不够用了,制造业还有个麻烦事:大家受教育的程度变高了,新成长起来的劳动力就不想进制造业了,为啥呢?因为在制造业干活又脏又累,还挣不到多少钱。制造业的平均工资虽然一直在涨,可制造业干活的人的比例还是开始下降了。
GDP高速增长的时候要是遇到劳动力短缺的情况,工业机器人就是最好的解决办法。在简单重复、劳动强度大、工作环境差的情况下,工业机器人比人干活更有效率。还有啊,数控技术、感应能力这些技术不断进步,工业机器人「替代人」的效率也就越来越高了。现在,工业机器人不光能「替代人」,而且生产任务完成得比人又快又好。咱们国家处于高增长、低劳动力供给的状况,这给工业机器人的发展提供了非常好的条件。
汽车和电子产业的需求很旺盛。
工业机器人在汽车和电子行业的应用是最多的。日本工业机器人产业之所以能快速发展,就是因为它有庞大的汽车产业作为应用基础,这两者其实是相互促进的。工业机器人帮日本车企解决了劳动力不足的问题,而车企提供的大量订单和资金流,又解决了日本机器人产业起步时的难题。即便到现在,汽车行业仍然是机器人应用数量多、范围广的行业中的一个,2020年用于汽车行业的机器人数量占总量的27%。50年前,工业机器人的应用差不多完全依靠汽车行业,现在不一样了,随着工业机器人技术不断成熟,它的应用范围扩大了很多。近年来,电子行业在工业机器人应用方面成了「新宠」。2020年,用于电子行业的机器人销量达到了机器人总销量的37%,和2011年的23%相比,提高了14个百分点,已经远超汽车行业,成了工业机器人应用最多的领域。
汽车行业是传统的应用大户,给工业机器人的发展打牢了基础。国内经济发展得很快,还有国家政策扶持,咱们国家汽车的产销量在2009年开始就一直是世界第一。2001年的时候是233万辆,到2017年最多达到了2902万辆,复合增长率有17.06%。2020年,咱们国家汽车产量占世界总产量的32.5%。这么大的产业规模给工业机器人发展铺好了路。咱们国家汽车行业在国内自动化率是最高的,2019年汽车工业机器人密度是938台/万人,这可比制造业187台/万人的密度高多了。不过,和日本、美国、德国这些工业强国比起来,咱们国家还有提升的空间。
国内新能源汽车行业发展得特别快。中国汽车工业协会的数据显示,2013年的时候,我国新能源汽车才卖出去1.8万辆。可是到了2021年呢,新能源车的销量一下子就达到了352.1万辆,跟去年比增长了157.5%,在市场上占的份额也提高到了13.4%。国家统计局也有数据,截至2021年底,我国新能源汽车保有量有784万辆,这个数量占世界总量的一半还多呢,咱们国家是世界上新能源汽车保有量最多的国家,也是全球新能源汽车产量最大、市场最大的国家。新能源汽车用的能源更干净、更高效,有节能、环保这些优点,这就是以后的发展方向。中国是世界上最大的新能源汽车市场,接下来的几年里,各个厂商都会把这里当成主要的进攻市场。新能源汽车给国产工业机器人带来了新的机会。新能源汽车行业发展起来以后,有可能打破国外工业机器人巨头在汽车制造行业的垄断局面。以前啊,制造传统汽车的厂商大多是国外独资或者合资的企业,这些企业更乐意跟国外那「四大家族」合作。但是现在国内新能源汽车行业起来了,这不但能让国产车企有弯道超车的机会,还能给国产工业机器人的发展创造机会,像新松机器人的产品已经进到华晨宝马、上汽、长城这些国内厂商的生产线里了。国产工业机器人有望和国产新能源汽车一起成长。
汽车行业的总营收和人均营收都在往上走。2021年,我国汽车行业总营收有8.7万亿元,和上一年比增长了6.3%;人均营收是208.7万元,同比增长4.9%。产能不断升级,才让人均营收持续增长。以前汽车生产线靠很多人干活,生产效率低,工作环境也不好。加了工业机器人这些自动化设备之后,生产员工慢慢从「劳动型」变成「技术型」了。我国汽车生产线搞自动化生产已经有了些成绩。自动化程度越来越高,再加上引入工业互联网,生产效率还会再提高。
电子行业是工业机器人发展的新动力,在行业里算得上是新贵了。老百姓生活水平提高了,对电视机、电脑、智能手机这些电子设备的需求也越来越大。咱们中国生产成本低,所以就成了世界电子产品的制造工厂,全球七成以上的电子产品都是中国制造和装配的。从1998年开始,我国电子产业的营业收入就在各大制造行业里排第一。2021年,我国电子制造业主营收有14.13万亿元,占GDP总量的12.35%。
电子行业搞「机器换人」,经济效益特别明显。就拿外观件的龙头企业长盈精密来说吧,它把生产线改造了一下之后,效果非常好。生产线的工人数量从一开始的600人减少到了还不到50人,每年光人工成本就能节省2800万还多。产品综合良率从不到70%提高到了95%以上,单日的产能也从8000提升到了25000。
智能手机大多在中国生产。中国是全球智能手机普及率排在前列的国家之一。根据中国通信院的数据,2021年中国手机出货量有3.51亿部,其中智能手机出货量是3.41亿部,在总出货量里占比97.7%。因为市场庞大,中国出了像华为、小米、OPPO这些有名的厂商。而且,中国是世界最大的智能手机生产地。虽说这几年手机产量的增长速度有点下滑,可产量的数值还比较高呢,2021年全年中国智能手机产量达到了12.7亿台。智能手机制造方面,「机器换人」的空间很大。手机生产属于劳动密集型产业。以前,靠着人力成本低,中国的手机制造工厂越来越多,还出现了富士康这个全球最大的电子产品代工厂。2013年的时候,富士康的员工人数就达到了120万,差不多是一个地级市的人口数。随着人口红利慢慢没了,人力成本不再是优势,「机器换人」就成了这些代工企业仅有的出路。实际上,有些公司已经开始这么做了。仅富士康昆山园区就通过「机器换人」裁掉了6万名员工。
(3)政策支持。
中央出台了不少政策来鼓励工业机器人发展。【中国制造2025】率先开启制造升级之旅,提到2025年国产工业机器人的市场占有率要达到70%,核心零部件国产化率要达到80%。之后国家又出台了好些相关政策,给工业机器人发展指明了方向。中央的这些明确政策让工业机器人行业发展更有信心,目标也更坚定了。
各地都在积极扶持工业机器人。广东省会在「工业与信息化发展专项资金」里安排工业机器人发展的专项资金,还会按一定比例补贴采购价格;深圳市每年拿出5亿元专项资金,补助工业机器人等智能产业;东莞市给企业购买国产工业机器人补助15%,镇里还有20% - 50%不等的配套补贴;浙江省财政累计安排了将近6亿资金来支持「机器换人」技术改造,出台了工业机器人购置奖励补贴政策,购置工业机器人按价格的10%补贴。(报告来源:未来智库)
【五、重点公司分析】
工业机器人。
(1)埃斯顿
埃斯顿是中国最早自主研发交流伺服系统的企业。其工业自动化系列产品有全系列的交流伺服系统、变频器、PLC、触摸屏、视觉产品、运动控制系统,还有以Trio控制系统为核心的运动控制与机器人一体化的智能单元产品,能给客户提供从单轴到单机再到单元的个性化自动化方案。在自主核心部件的支持下,埃斯顿的工业机器人产品线发展得特别快。它的产品以六轴机器人为主,负载范围在3kg - 600kg之间,有54种以上的完整规格系列,在新能源、焊接、金属加工、3C电子、工程机械、航天航空等细分领域有头部客户,市场份额也比较大。
汇川技术。
汇川技术是国内工控领域的龙头企业,业务范围包括通用自动化、电梯电气大配套、新能源汽车、工业机器人、轨道交通这些领域。现在它的伺服在国内排第一,变频器在国内能排到前三,SCARA机器人在内资里份额是第一。2014年的时候公司就开始涉足机器人产业了。到了2017年,机器人有了视觉跟踪、飞拍这些技术,「核心部件 + 整机 + 视觉 + 工艺」都布局好了,这有助于走向高端化。
(3)凯尔达
公司的实际控制人是从工业焊接设备这个领域开始发展起来的。2002年的时候,他成立了凯尔达电焊机有限公司,就开始做工业焊接设备方面的业务了。2009年呢,又成立了杭州凯尔达焊接机器人股份有限公司。到了2012年,完成了基于PLC运动控制器的工业机器人研发工作。2013年,公司把机器人专用的超低飞溅焊接电源研发出来了。2017年,公司推出了伺服焊接机器人以及配套的设备。也是在这一年,开始研究基于工业PC机 + EtherCAT总线技术的第三代工业机器人。2020年,公司薄板焊接机器人的销售量在国内排第三,排在前面的是OTC和松下这两家。
2、特种机器人
亿嘉和
公司刚成立的时候,主要做电子网络设备的销售工作。从2014年开始,慢慢推出室内和室外巡检机器人产品。到了2018年,又推出消防机器人、物流机器人这些产品。2019年,室外带电作业机器人Z100被推出。2020年开始,公司收购佗道医疗并且定向增发股票,重点在医疗机器人领域和消防搜救机器人领域布局。公司最后以特种机器人为核心,主要有操作类机器人、巡检类机器人、消防类机器人这三大类产品。操作类机器人的批量生产和使用,给公司带来了新的发展机会,也让公司的技术门槛变得更高了。
3、关键零部件
「绿的谐波」
公司第一个突破了谐波减速器技术上的难题,不管是实现量产,还是打破垄断,在国内都是头一份,在国内谐波减速器这个领域,那就是妥妥的龙头老大。2003年的时候,董事长左昱昱就开始仔细钻研谐波啮合理论了,到了2013年,公司的第一台谐波减速器就开始上市售卖了。这家公司是国内第一个做到谐波减速器量产并且批量销售的企业,现在它的产能在国内是最大的,一年能生产30万台呢,在自主机器人品牌里,它的渗透率超过了80%。它还是国内第一家成功冲破国际谐波减速器品牌在这个领域垄断的企业,现在给很多大客户提供配套产品,像在全球协作机器人领域市场占有率排第一的UR机器人,还有ABB、GE这些国内外的重要企业。
(2)双环传动
双环传动一门心思扑在齿轮及其组件的研发、制造和销售上,现在已经是全球最大的专业齿轮产品制造与服务企业之一了。它现在的产品主要是乘用车齿轮、商用车齿轮以及工程机械齿轮。由于技术是相通的,双环传动从2013年就开始研究RV减速器,自己研发出了德高精密摆线减速器。目前,双环传动的RV减速器已经顺利进入像埃斯顿这样的国内顶尖机器人本体厂商的供应链,而且还在积极地配合外资品牌送样测试呢。现在公司RV减速器的产能差不多有6万台,并且打算在年底把产能扩大到10万台。
(本文仅供参考,不表示我们有任何投资建议。如果想要使用相关信息,请查看报告原文。)
精选报告来源:【未来智库】。未来智库 - 官方网站