文|正经的烧杯
编辑|正经的烧杯
«——【·前言·】——»
TWIP钢由于高强度、高伸长率以及无低温韧脆转变温度等良好的性能,已成为现代汽车轻量化发展应用的主要候选材料,用其制作减震器支座,可使质量由原来的6.25kg降至2.40kg,轻量化效果显著。
TWIP钢在轧制过程中钢板的表面会生成一层较致密的氧化层,传统的清洗钢板表层氧化层的方法主要为酸洗,但该方法存在清洗效率低、易引入新的杂质元素且对环境危害性较大的缺点。
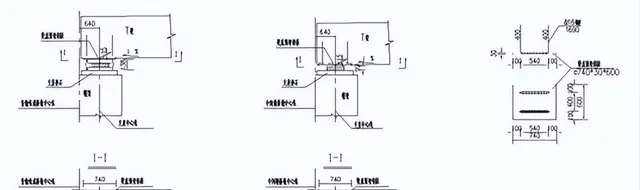
激光清洗作为新兴清洗方式,具有无接触、绿色、高效等显著优点,近年来在工业生产中已经逐渐得到应用。
河北一企业,由于大量使用WIP钢,造成企业中的表面氧化物较多,企业研究人员在使用激光清洗的方式清理表面氧化物,这也使用清洗效率增高,而且还降低了不少成本。
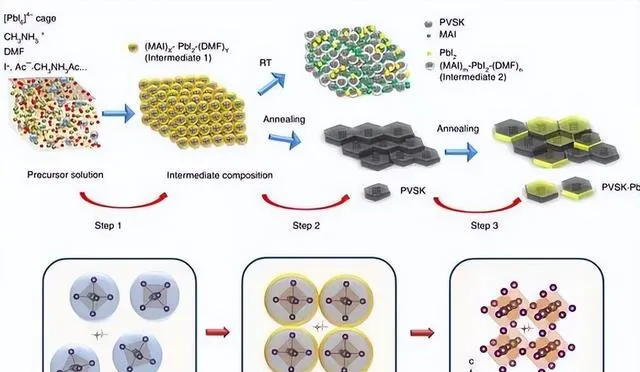
例如:在半导体和磁盘驱动器制备中,激光可以有效去除存在集成电路模具和磁盘表面的污染物和颗粒,实现微型精密清洗。
在焊接生产中,经激光清洗过的试件焊接后,也表现出优异的焊接质量,气孔率,相比其它清洗手段明显降低在造船业中,运用合适的激光参数,能够有效清洗掉钢板表面存在的污染物。
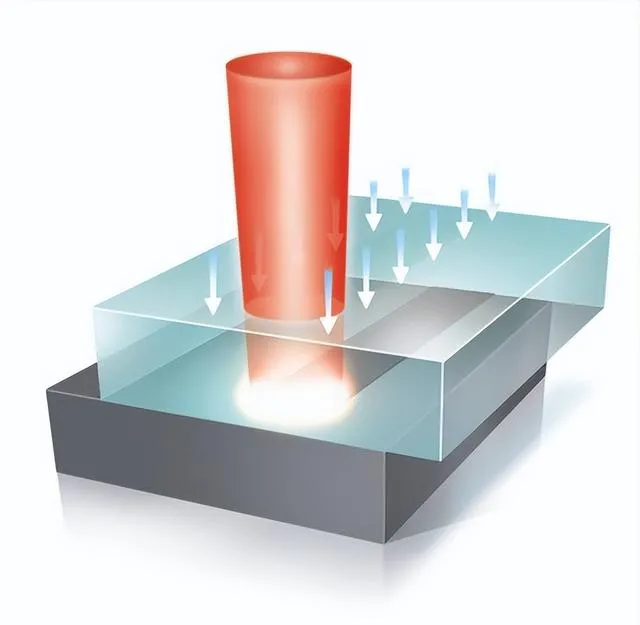
不仅如此激光清洗在去除金属材料,表面杂质方面也得到了深入研究,Sun等7采用脉冲激光实现了,45钢表面锈层的完全清洗,提出了激光束造成深层锈层的振动和激光支持,引起热冲击的除锈机理。
用脉冲激光对3mm厚的铝合金板进行清洗,采用能量密度作为变量,得到不同能量密度下氧化膜的去除机制,短和超短脉冲进行金属烧蚀研究,发现激光微结构中,精度和效率存在冲突。
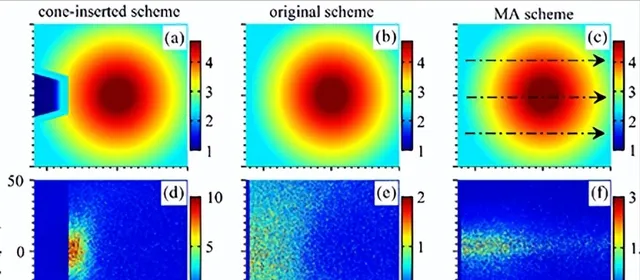
短脉冲微秒和纳秒系统允许高消融率,不可避免出现工件的热损伤;超快皮秒和飞秒系统则与其相反,波长和能量密度的激光对氧化物的去除过程,分析出激光清洗过程中发生了瞬时热氧化。
提出了光热和机械效应共同作用的热烧蚀清洗机制,得到了清洗过程中激光瞬态热效应造成表面改性的结论,以上研究结果表明:激光清洗过程涉及热、力、光等多种作用,激光清洗的工艺和机理较为复杂。
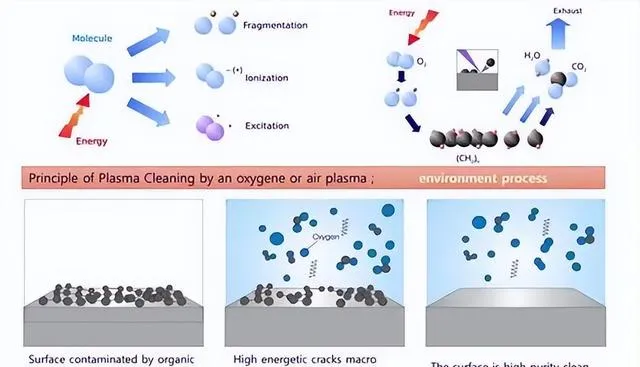
且不同金属基体,和表面污染物对应不同的清洗工艺,参数和清洗机理,而WIP钢,由于成分与普通碳钢差别较大,以及轧制钢板表面氧化层较致密的特点,其激光清洗工艺及氧化层,去除机理应与普通碳钢,以及其他合金有一定区别。
开展钛合金钢板表面氧化层,的激光清洗技术研究,对于减小经济成本,加速其在汽车工业的应用具有重要意义。
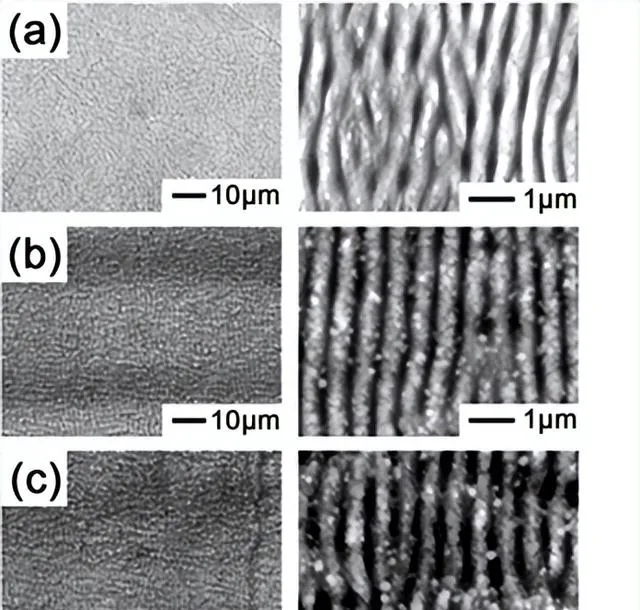
本文利用纳秒脉冲激光清洗轧制,TWIP钢板表面的氧化层,通过不同激光能量密度激光,清洗实验确定氧化层清洗阈值,及TWIP钢基体损伤阈值,借助扫描电镜,和能谱仪对清洗前后的表面,进行形貌观察和成分分析,判断清洗效果,并推测激光清洗机理。
«——【· 实验材料与方法 ·】——»
表1为熔炼所得TWIP钢的名义成分,将熔炼所得的TWIP钢在300℃下轧制为3mm厚的钢板后,用剪板机截取尺寸180mmx200mmx3mm的钢板。
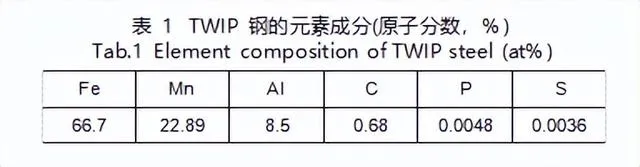
然后使用线切割机,切成若干10mmx10mmx3mm的试件,激光清洗前,用无水乙醇清洗试件表面尘土和油污并用吹风机吹干。
采用IPG公司生产的激光,清洗设备开展激光清洗实验,其配备的脉冲激光器所发射激光波长为1064nm,可提供的最大平均功率为50W,频率范围10~200kHz,表2为激光清洗设备的主要参数。
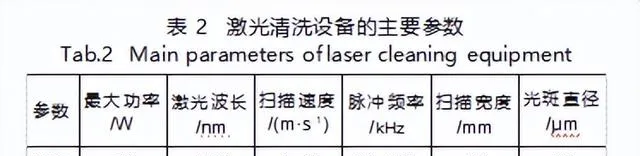
TWIP钢表面氧化层的厚度,通过COOLPIX-4500型光学显微镜观察,截面样品制备步骤包括镶样、砂纸打磨、抛光和4%硝酸酒精溶液腐蚀等。
激光清洗前后微观形貌,利用TESCANVEGA3扫描电子显微镜观察,TWIP钢表面O元素,含量则采用扫描电镜配备的能谱仪(EDS)进行测量。

«——【· 实验结果与分析 ·】——»
图1为激光清洗前后,TWIP钢样品表面以及基体本身的氧含量图,插图为激光清洗前后,TWIP钢截面样品的金相照片。
采用能谱仪,测得的TWIP钢清洗前、清洗后以及基体的0元素含量分别为38.5at%、4.2%和1.8%。
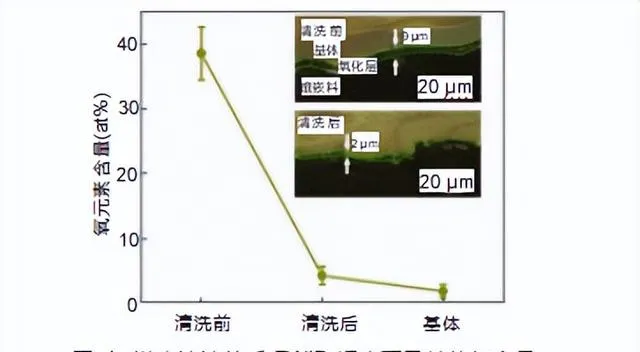
清洗后表面氧含量与基体相当,可见激光清洗能有效,去除TWIP钢基体表面氧化层,从图1(a)激光清洗前TWIP钢截面,样品金相照片可观察到镶嵌粉、氧化层、基体3层物质,且界面清晰可见。
经测量得到激光清洗前,基体表面氧化层平均厚度约为9μm,图1(b)是经功率P为20W、频率f为20kHz的脉冲激光清洗后,的TWIP钢截面照片。
可看出,激光清洗可以有效去除轧制TWIP钢表面的氧化层,但钢基体表面部分区域仍存在少量残存的氧化层,厚度约为2μm。这与EDS测得的氧含量数据一致。
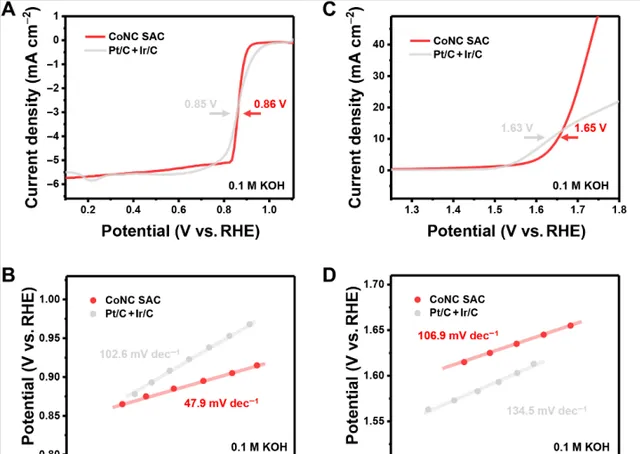
在实验过程中,通过调整脉冲频率和功率大小来调控E,图2是TWIP钢表面经不同能量密度及次数激光清洗后的扫描电镜表面形貌照片。
如图2所示,未进行激光清洗的氧化层表面高低不平,表面有明显的球状颗粒。从图2(f)氧含量看出,此时的氧含量为38.5%,氧化层较厚。
当氧化层经E=8.5J/cm清洗1遍后,材料表面的的球状颗粒消失(图2(b)),但表面的氧含量仍能达到34.1%(图2(f)。
表明此时的氧化物层仍未得到有效清洗,而当能量密度提升到12.7J/cm时,材料表面的形貌更加凹凸不平,孔的大小和数量有所增加,氧化层由于激光的光热作用发生了膨胀现象。
此时的氧含量出现大幅度下降,降为22.0%(图2(c)、(f))。这表明,此能量密度下,能够有效的清洗TWIP钢表面氧化层。
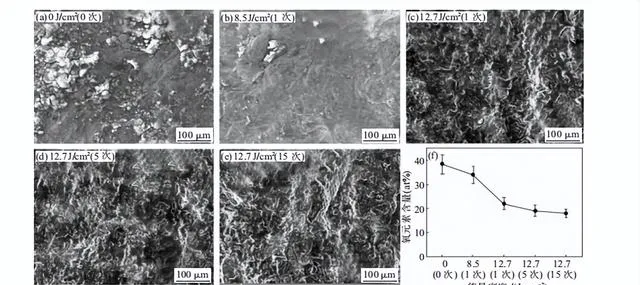
同样在E=12.7J/cm的能量密度下,清洗次数增加到5次,甚至15次,从图2(d)、(e)可看出,此时的材料表面变得更加粗糙,然而表面未观察到由材料蒸发导致的烧蚀坑。
氧含量缓慢降低(图2(f),基于此可以推出,此能量密度下,随着热量的累积,在光热作用下,材料表面仅发生由于热膨胀而导致的氧化层的移除,不会导致基体的损伤。
可得到氧化层的激光清洗阈值为12.7J/cm,图3为当能量密度E从12.7J/cm进一步时TWIP钢表面的扫描形貌图。图3(a)(d)分别
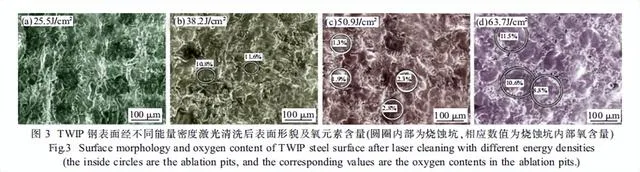
对应E=25.5、382、50.9、63.7J/cm清洗1次后,材料表面的形貌照片,可看出经能量密度为25.5J/cm的激光清洗后样品表面仍未出现明显烧蚀坑(图3(a))。
随着激光能量密度逐渐增加,样品经激光清洗后出现明显烧蚀坑。由图3(b)、(d)可看出,烧蚀坑直径逐渐从大约30μm增加至100μm左右,且烧蚀坑表面形貌逐渐变得光滑平坦。
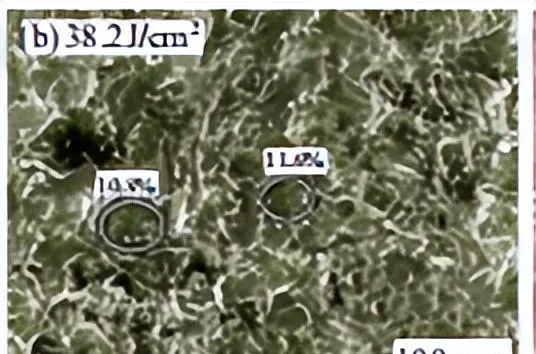
从图3(c)能量密度为50.9J/cm时激光清洗后的扫描图可看出,图中出现近圆形的烧蚀坑,同时存在沿着烧蚀坑径向方向喷射出的熔融体。
该现象产生的原因为当激光能量密度足够大时,氧化层表面蒸发被带走部分材料,但由于激光束能量呈高斯分布,烧蚀坑边缘距离光束中心较远,没有达到气化状态,材料只发生熔化,熔化的材料沿着温度梯度方向即烧蚀坑径向外流动。
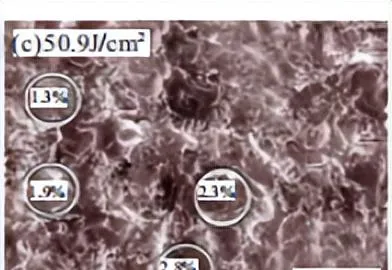
即形成中间,为烧蚀坑边缘为凝固的熔体的形貌,如图3(c)中所示的氧元素的原子百分含量,值均与基体的1.8at%非常接近,有些区域甚至低于基体氧含量值,相比之下,图3(b)能量密度为38.2J/cm时,材料表面尽管出现烧蚀坑,但氧含量明显高于基体。
以上结果说明E=38.2J/cm时钢表面氧化层未去除干净,而E=50.9J/cm时试件表面氧化层完全清洗干净。
并且可以推测当进一步增大激光能量密度,基体将损伤,当E进一步提高到63.7J/cm2时,烧蚀坑更加明显,氧含量明显增加,表明此时的表面重新被氧化(图3(d))。
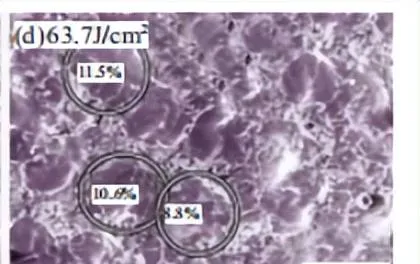
因此可认为TWP钢损伤阈值为50.9J/cm,陆思远[20]证明自然腐蚀下碳钢的清洗阈值和损伤阈值分别为8.0、237J/cm2。
将本TWIP,钢试验结果与普通碳钢研究结果对比,发现TWIP钢的清洗阈值和损伤阈值,分别高于和低于普通碳钢的清洗阈值和损伤阈值。
这是由于常温下自然腐蚀的锈层疏松、多孔,而轧制TWIP钢表面的氧化层更致密,导致TWIP钢的清洗阈值比普通碳钢的要大。
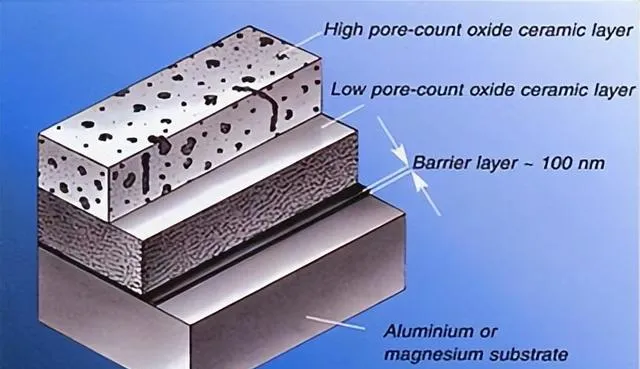
另外普通碳钢锈层厚(>30μm),而TWIP钢氧化层厚度小(<10μm。由于更高的能量密度有利于去除更厚的氧化层。
因而TWIP钢的损伤,阈值比普通碳钢的小的多;还有一部分原因可能是氧化层的成分不同导致的,因为TWIP钢的氧化层中可能含有一定的Mn的氧化物。
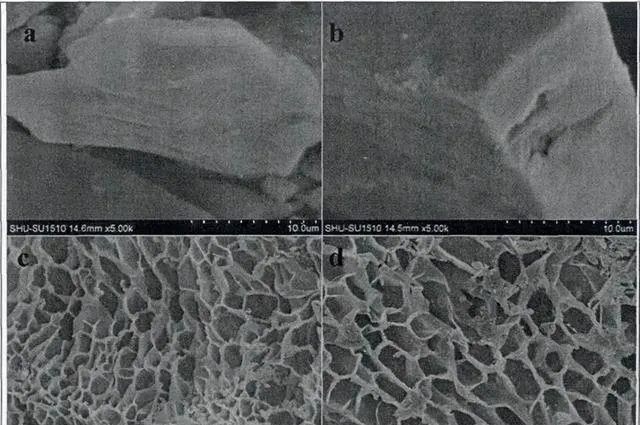
图4为能量密度由低到高的3个阶段清洗机理示意图,图中两箭头表示激光束,右边绿色箭头为已完成激光清洗的激光束。
当激光能量密度低于12.7J/cm2,吸收的能量不足以引起氧化层发生膨胀,当能量密度为12.7~38.2J/cm2时,TWIP钢表面形貌开始发生变化,由于此时能量密度值较低,表面未出现明显烧蚀坑,只是由于热效应的积累。
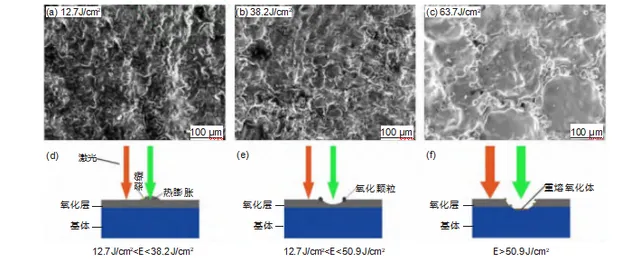
表面发生熔化,氧化层发生膨胀,局部微小区域开裂,氧化层在热膨胀的作用下脱离基体,如图4(a)、(d)所示。当能量密度达到38.2~50.9J/cm2时,烧蚀坑逐渐明显,表面吸收的热量造成的瞬时升温超过氧化层蒸发温度。
产生清晰可见烧蚀坑,烧蚀坑边缘伴随着氧化物颗粒的熔体排出,从而实现氧化物的移除,如图4(b)、(e)所示。当能量密度大于50.9J/cm2时,超过激光清洗损伤阈值,基体被重新氧化,伴随有颗粒氧化物熔体排出,如图4(c)、(f)所示。
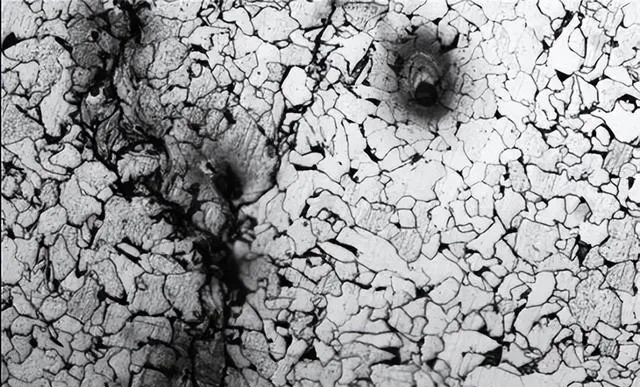
«——【·结语·】——»
采用激光清洗TWIP钢表面氧化物,发现氧化层的厚度与EDS测得氧含量数据正相关,可以采用EDS氧含量来,定性评估氧化层厚度以及清洗效果,利用扫描电子显微镜,和能谱仪对激光清洗前后TWIP钢表面,形貌和成分进行分析。
发现通过调整激光能量密度,可以有效去除TWIP钢表面氧化层,而不侵蚀基体,确定了氧化层的清洗阈值为12.7J/cm,基体损伤阈值为50.9J/cm2。
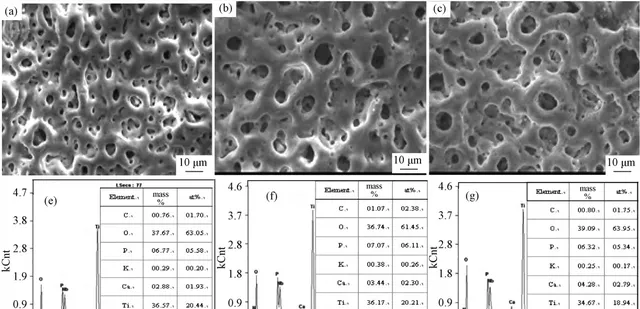
随激光能量密度的增加,TWIP钢表面先发生由于氧化层的热膨胀而从基体脱离(12.7J/cm<E<38.2J/cm2),再产生表面氧化层的蒸发、热烧蚀(38.2J/cm<E<50.9J/cm),最后出现基体的再氧化过程(E>50.9J/cm)。