(報告出品方:光大證券)
【1、 絲杠:高效能線性傳動機構】
特斯拉機器人Optimus的軀幹有28個關節,旋轉關節和直線關節各14個。每個關節都對應著1個執行器。為了能大批次生產,特斯拉最後挑了6類執行器用在這28個關節上。這6類執行器裏,旋轉執行器和線性執行器各有3類。線性執行器的重量在0.36kg到2.20kg之間不等,推力分別是500N、3900N和8000N,還配備了反向式行星滾柱絲杠,有高效率、緊湊性佳、耐用性強這些特點。
線上性執行器裏,是反向式行星滾柱絲杠把電機的旋轉運動轉變成直線運動的。跟其他直線機構比起來,絲杠在承載能力、位置的可控性、抗沖擊性等好些方面都更有優勢。
絲杠產品常見的有滑動絲杠、滾珠絲杠、行星滾柱絲杠這些。絲杠軸上有圓弧形狀的輪廓,這個輪廓順著一定的升角(導程角)在軸上盤旋。基本的原理就是,把絲杠軸的一端或者兩端沿著軸向固定住,用電機帶動絲杠轉動,螺母就會朝著絲杠軸線的方向動起來。在這之中,滑動絲杠造起來成本最低,結構也簡單,靠螺母和絲杠之間的滑動來讓螺母動,這樣就產生了滑動摩擦;滾珠絲杠和行星滾柱絲杠呢,把滑動摩擦變成了捲動摩擦,傳動效率就大大提高了。
【2、 滾珠絲杠:廣泛套用,高效精準】
2.1、 滾珠絲杠和滑動絲杠比起來更有優勢。
絲杠和螺母上都被磨出圓弧形螺旋槽的滾珠絲杠,把兩個這樣的螺旋槽對合起來就會形成螺旋線滾道。電機帶動絲杠轉動的時候,滾珠就在管道裏迴圈運動,而且螺旋槽的兩端設定有回旋引導裝置,這能讓滾珠迴圈流動。滾珠絲杠的摩擦系數是0.003到0.01,梯形絲杠的摩擦系數則在0.1到0.2。所以呢,因為滑動摩擦系數比捲動摩擦系數高得多,滑動絲杠為了不產生太多熱量,轉速通常不超過3000RPM,而滾珠絲杠卻能達到10000RPM。
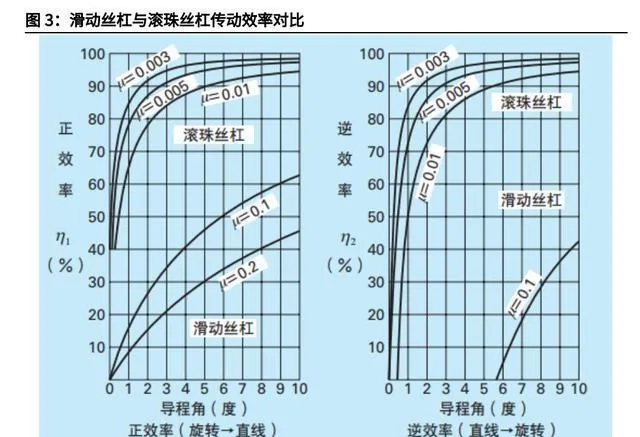
滾珠絲杠依據滾珠的迴圈方式以及是否一直和絲杠接觸,主要能分成內迴圈和外迴圈這兩種。外迴圈按照結構差異又可分為端部導流式、管迴圈式、端蓋式。和滑動絲杠比起來,滾珠絲杠有下面這些特點:1. 傳動效率高:多數滾珠絲杠傳動效率能到90%以上,可滑動絲杠的傳動效率大多在70%以下。2. 傳動精度和定位精度高:不會有爬行的情況,運動起來很平穩。3. 能預緊:給它適當預緊的話,可以把絲杠和螺母之間的螺紋間隙去掉,反向的時候能消除空行程死區,接觸剛度和傳動精度都能提高。4. 運動可逆:絲杠和螺母都能當主動件,既能把旋轉變成直線運動,也能把直線運動變成旋轉運動。5. 摩擦損失小:用的是捲動的方式,東西磨損小,使用壽命長。不過制造工藝復雜,對滾珠絲杠和螺母原件的加工精度和表面粗糙程度要求高,這樣制造成本就上去了。要說明的是,滾珠絲杠因為傳動效率比較高,一般自己沒有自鎖性,滑動絲杠有一定自鎖性。所以絲杠用在豎直方向的時候,滾珠絲杠斷電後可能會滑落,得有額外的結構或者器件來保證安全。
2.2、滾珠絲杠有內迴圈和外迴圈這兩大類別。
滾珠得無限迴圈,所以所有滾珠絲杠都至少包含絲杠軸、螺母、滾珠、迴圈部件這四大零部件。按滾珠的迴圈方式來分,有內迴圈和外迴圈這兩大類別:(1)內迴圈是在相鄰導程之間借助馬蹄狀導流器來迴圈的,這種方式適合小導程。(2)外迴圈又可以分成端部導流式、管迴圈式、端蓋式。端部導流式是在螺母端部順著絲杠螺紋槽切線方向平緩地把滾珠掬起來,再透過螺母內部的貫通孔來迴圈,這種方式適合高速靜音傳送;管迴圈式是讓滾珠在適合其大小的迴圈管裏在始點和終點之間來回迴圈,它能適用的規格(軸徑、導程)範圍很廣;端蓋式是在螺母端部設定拉起滾珠的端蓋,透過螺母內部設定的貫通孔迴圈,適合大導程。
滾珠絲杠精度等級的劃分標準是這樣的:隨便取一段300MM長的絲杠,量一量實際移動的距離和理想移動距離有多少偏差,偏差越小,精度就越高。在國內,精度等級分為P1、P2、P3、P4、P5、P7、P10;日本、南韓和中國台灣省用的是JS等級,也就是CO、C1、C2、C3、C5、C7、C10;歐洲國家采用的標準是IT0、IT1、IT2、IT3、IT4、IT5、IT7、IT10。一般來說,普通機械用C7、C10級別的絲杠就能達到加工要求了;數控器材通常得用C3、C5級別的絲杠,在國內,大部份數控機床配的是C5級絲杠。航空制造器材、精密投影還有三座標測量器材等一般用C3、C2級別的絲杠。從功能上看,絲杠分兩種,一種是傳動級絲杠,一種是定位級絲杠。傳動級絲杠的精度在C6 - C10之間,這種絲杠一般是輥軋制造的,所以也叫轉造級絲杠;定位級絲杠的精度在C0 - C7之間,它一般是用磨床制造的,所以也被叫做研磨級絲杠。
NSK披露,在數控機床裏,車床、銑床、鏜床、鉆床、沖床等常用的精度等級是C5;磨床、電火花加工機械、線切割機等常用精度等級為C3;半導體/印刷版制造裝置常用的精度等級是C1;工業機器人常用精度等級在C5 - C7之間。
2.3、滾珠絲杠市場:國內企業正在朝著中高端發展。
2020年金屬加工雜誌社做了第三屆捲動功能部件使用者調查分析報告,報告顯示數控機床仍然是捲動功能部件最大的使用者群。制造業朝著數碼化、智能化轉型升級的時候,機器人和生產線領域使用捲動功能部件的占比增長得特別快。
從市場空間來講,全球滾珠絲杠市場的規模在穩步增長,中國已經是最重要的消費市場中的一個了,長遠來看,成長的空間很可觀。據秦川機床的公告,2016 - 2021年期間,全球滾珠絲杠市場規模從13.1億美元漲到了17.5億美元;同一時期,中國滾珠絲杠市場規模從16.8億元增加到25.6億元。中國成了滾珠絲杠產品重要的消費市場之一,大概占全球規模總量的20%上下。從市場競爭格局方面看,現在全球主要的滾珠絲杠廠商有NSK、THK、SKF等。按照華經產業研究院的統計,2021年的時候,排名前五的企業銷售額的市場占有率達到了大概46%,主要是歐洲和日本的企業,日本和歐洲的滾珠絲杠企業占據了全球大概70%的市場份額。
在國內的行業供需方面,滾珠絲杠是需求量比產量大,供需缺口在行業裏很明顯。據華經產業研究院統計,2021年中國滾珠絲杠的產量是983萬套,需求量達1406萬套。從價格走勢來說,這幾年中國滾珠絲杠行業的市場競爭越來越激烈,國內的企業往中高端市場發展,外資品牌忙著搶占經濟型產品的市場份額,市場競爭明顯加劇了,這就導致行業市場價格整體上明顯下降。國內滾珠絲杠的價格,從2014年平均每套225元降到了2021年的181元每套,預計2022年市場價格會降到180元每套,下降的速度慢下來了。
國內滾珠絲杠的高端市場差不多都被德國力士樂、日本的THK、NSK把控著,中端市場呢,是被德國、日本品牌(像力士樂、THK、NSK),中國台灣的品牌(上銀、銀泰),中國大陸的品牌(漢江、南工藝)所占據的。
【3、 行星滾柱絲杠:下一代高承載產品】
3.1、行星滾柱絲杠:承載能力強、速度快、使用壽命長。
行星滾柱絲杠(Planetaryrollerscrew,PRS)和滾珠絲杠差不多,是一種能把旋轉運動和直線運動相互轉換的機械裝置。PRS在1942年最早被瑞典人CarlBrunoStrandgren發明出來。到現在還沒有被廣泛套用,主要是因為它結構復雜,加工起來很難,成本也高。現在主要用在民用方面,像精密機床、食品包裝、特種機械、測試仿真這些領域。隨著飛行器和武器裝備朝著全電化發展,還有石油、化工、機床這些領域需要大推力、高精度、高頻率、高效率、長壽命的機械裝置來當機電作動系統(Electro-MechanicalActuator,EMA)的執行機構,用來取代容易被汙染、維護成本高的傳統液壓作動系統(Electro-HydrostaticActuator,EHA)。再加上內、外螺紋加工工藝提高了,制造器材和相關材料技術也發展了,這幾年行星滾柱絲杠受到廣泛。標準的行星滾柱絲杠主要由滾柱絲杠、滾柱螺母、滾柱、內齒圈、壓蓋和擋圈構成。滾柱絲杠和滾柱螺母是齒形角為90°的多頭螺紋。滾柱的齒形是雙凸圓弧的單頭螺紋。好些滾柱在絲杠周圍均勻分布。當滾柱絲杠轉動的時候,滾柱既繞著絲杠軸公轉,又繞著自己的軸線自轉,從而帶動滾柱螺母軸向移動。所以,行星滾柱絲杠副裏滾柱和絲杠、螺母是捲動摩擦,傳動效率最高能達到90%。行星滾柱絲杠副的承載主要是靠滾柱螺紋和絲杠、螺母90°齒形角兩邊點接觸來承載的。
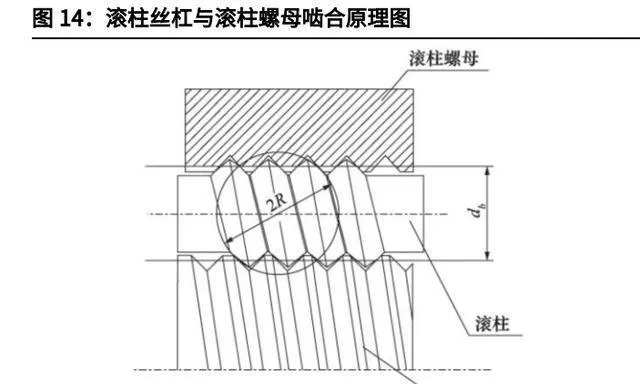
和現在廣泛使用的滾珠絲杠比起來,要是用行星滾柱絲杠來傳動的話,有下面這些好處:1)承載能力強、能抗沖擊,而且體積小。行星滾柱絲杠是線接觸的,接觸面積變大了,承載能力和剛性就大大提升了。每個滾柱的每條螺旋線都能同時和配合的部件受力接觸,一起承擔負載。這樣的設計能讓負載分散到更多的接觸點上,每個接觸點承受的最大壓力就變小了,承受沖擊載荷的能力很強,工作起來很可靠。在相同的載荷條件下,行星滾柱絲杠的體積比滾珠絲杠要小三分之一。2)速度快、噪音小。滾珠絲杠的鋼球得反復載入、解除安裝,還得在滾珠迴圈通道的兩端急劇轉彎,行星滾柱絲杠就不一樣,它的轉速能達到6000轉每分鐘,最高線速度能到2000毫米每秒,最大加速度能到3G。滾珠絲杠機構的噪音是因為滾珠在迴圈通道裏相互碰撞和急速轉彎產生的,行星滾柱絲杠的噪音是滾柱兩端正時齒輪機構嚙合產生的,這個頻率更高,而且不會隨著絲杠轉速升高而成指數級增長。所以,行星滾柱絲杠比滾珠絲杠噪音低。3)精度高、壽命長。絲杠軸是小導程角的非圓弧螺紋,這樣有利於達到更高的導程精度,能夠實作精密微進給。行星滾柱絲杠能承受的靜載是滾珠絲杠的3倍,壽命是滾珠絲杠的15倍。4)容易安裝和維護,適應環境能力強。電動缸裏的一體化螺母元件很容易從絲杠軸上分開,捲動體和相關零件不會散落,安裝和維修都很方便。電動缸對惡劣環境(像低溫、有粉塵、化學沈積和沒有潤滑等情況)的適應能力比較強。
3.2、行星滾柱絲杠大體上有五種類別。
行星滾柱絲杠發展了數十年,有了不同種類,主要包括標準式、反向式、迴圈式、軸承環式和差動式。(1)標準式行星滾柱絲杠呢,滾柱兩端有螺旋齒。這是為啥呢?為了不讓滾柱的軸線相對絲杠傾斜,消除絲杠螺旋升角給滾柱帶來的傾覆力矩,這樣滾柱就能平行於絲杠軸線正常轉動了。(2)反向式行星滾柱絲杠和標準式的不一樣。反向式是螺母旋轉輸入,絲杠直線輸出,而且絲杠螺紋兩端加工了直齒,它的好處就是便於整合。(3)迴圈式行星滾柱絲杠的滾柱螺紋是螺旋升角為零的環槽,這是它很明顯的特征。這種行星滾柱絲杠能實作小導程,位置精度高,嚙合點更多,承載能力也更高。(4)軸承環式行星滾柱絲杠的螺母不是一個單獨部件,是由軸承環、殼體和端蓋組成的。動力從絲杠傳給滾柱,再到軸承環,軸承環兩端裝著推力圓柱滾子軸承,它能在軸承裏自由旋轉,然後把動力傳給推力圓柱滾子軸承,最後傳到螺母殼體上。(5)差動式行星滾柱絲杠,它的滾柱和螺母都是無螺旋升角的環槽,滾柱有大直徑段和小直徑段。大直徑段的環槽和絲杠螺紋嚙合,小直徑段的環槽和螺母環槽嚙合。它的優勢就是能實作小導程,結構簡單又好加工。
按照ISO3408 - 3的規定,行星絲杠的公差等級是咋劃分的呢?這裏的決定因素是300mm螺紋長度上的導程誤差V300p。它的標準精度等級有G1、G3、G5這幾種,要是有更高精度等級的需求,也能按要求進行非標生產。
3.3、行星滾柱絲杠的市場情況是:國內外企業之間存在著比較大的差距。
裝備制造業的自動化和智能化在不斷發展,機電伺服作動系統慢慢取代了傳統的液壓伺服作動系統和氣壓伺服作動系統。因為機電伺服作動系統有系統重量輕、效率高、安裝和維護方便這些優點,所以它成了伺服控制領域的首選,在航空航天、機器人、汽車、高精密機床等領域已經被廣泛套用。機電作動器(electro - mechanical actuator,EMA)是機電伺服作動系統的關鍵部件,主要包含電機、減速裝置和執行機構。執行機構是EMA的核心部份,它的傳動和承載效能直接影響EMA的工作效能。EMA的執行機構常見的有滾珠絲杠和行星滾柱絲杠這兩種。行星滾柱絲杠能承載高、耐沖擊,像航空、航天、船舶、石化、電力、醫療機械這些要求承載大、精度高、壽命長的領域,行星滾柱絲杠是比較好的選擇。
這產品的行業大拿大多來自歐洲、美國還有日本這些地方。那些外國企業一直都在搞行星滾柱絲杠的研發和推廣,已經攢下了超多生產套用方面的經驗,而且有了很成熟的產品系列。現在國外能生產行星滾柱絲杠的企業主要有瑞典的SKF、瑞士的Rollvis、德國的INA、美國的Exlar、德國的Rexroth、瑞士的GSA、英國的PowerJack、德國的LTK以及日本的NTN株式會社等。和國外比起來,國內行星滾柱絲杠的生產套用發展得比較慢。現在就只有幾家企業有小批次生產的本事,像博特精工、漢江機床、南京工藝這些企業。雖說這些企業已經能單個生產了,可和國外大規模的生產套用比起來,還是差著一段距離呢。所以國內還得想法子搞校企合作,加強基礎理論方面的研究,多投入些錢搞研發,把核心技術給攻克了。在國內市場上,SKF、Rollvis、GSA這些國際品牌占的市場份額比較高,另外還有南京工藝和濟寧博特這兩家國內品牌。目前這兩家公司的產品效能和國外比還有些差距,產業化還處在早期階段。從SKF公司行星滾柱絲杠產品的成本構成來看,原材料成本大概占60%,工時和生產方面的成本占15%,工廠裏的固定成本分攤是15%,集團向法國工廠收的管理成本占10%。
IHSMarkit對滾柱絲杠的銷售做了預測,2022年全球賣了8.6萬根滾柱絲杠,銷售額是6.5億元人民幣,在中國賣了1.0萬根,銷售額是1.1億元人民幣。
【4、 滾珠絲杠與行星滾柱絲杠的對比】
套用歷程是這樣的:(1)滾珠絲杠在1874年首次取得專利,而行星滾柱絲杠首次獲得專利是在1942年,這中間隔了68年;(2)1940年滾珠絲杠首次實際套用於汽車轉向機構,行星滾柱絲杠在1987年才開始大批次生產,這中間相隔47年。液壓系統呢,1795年就被發明出來了,到1870年的時候,液壓傳動技術就被用來驅動像起重機、絞車、剪下機之類的多種器材了。
把滾珠絲杠和行星滾柱絲杠的截面拿來對比一下,行星滾柱絲杠有這麽些好處。它的結構尺寸小,接觸線長,傳動間隙也小。它的結構尺寸小、承載能力大、傳動精度還高。特別是在動載荷這種工況的時候,行星滾柱絲杠有好多根滾柱呢,這些滾柱能把沖擊分散到螺紋接觸線上,這樣它的剛度和抗沖擊能力就更好。
滾珠絲杠高速運轉的時候,裏面的滾珠會受到離心力影響而滑動,這樣機構的徑向振動就更厲害了,還會出現溫升太快、壽命縮短這些問題;要是在多載的工作狀況下,因為彈性變形和摩擦力的影響,滾珠很容易卡死,就沒辦法正常運轉了。國外的學者依據Hertz應力定律,再結合實際的測試結果發現,在結構尺寸一樣的情況下,PRS的靜承載能力是滾珠絲杠的3倍,使用壽命大概是滾珠絲杠的15倍。
依據王有雪【E公司滾柱絲杠產品行銷策略研究】的內容,在國內市場裏,行星滾柱絲杠市場份額較大的品牌有Rollvis、GSA、Rexroth這三個國際品牌,還有南京工藝和濟寧博特這兩個國內品牌。Rollvis是瑞士的企業,在世界上那可是相當有名的行星滾柱絲杠專業生產商,發展了30年之後,它的產品銷售額在全球市場能占到差不多40%。國內滾柱絲杠高端市場差不多都被德國力士樂、日本THK、NSK給占了。中端市場呢,主要是三方面的勢力。一方是德國和日本的品牌,像力士樂、THK、NSK;一方是中國台灣的品牌,比如上銀、銀泰;還有一方是中國大陸的品牌,漢江和南工藝就在其中。
【5、 絲杠加工工藝:生產效率與產品精度的 平衡】
在機電伺服這個系統裏,行星滾柱絲杠可是核心機構呢,它對整個系統的動態效能有著非常關鍵的作用。要是它傳動的精度不夠,那整個伺服系統的響應速度和精度都會直接受到影響。行星滾柱絲杠的傳動精度會被很多因素影響,像它自己的誤差、環境帶來的誤差、回程產生的誤差以及中間的誤差等等。按照【金屬加工】雜誌社第三屆捲動功能部件使用者調查分析報告裏的說法,精度是企業考核行星滾柱絲杠時的首要技術指標。
行星滾柱絲杠的關鍵技術包括這些方面:(1)設計時得同時考慮螺紋和齒的加工。要是絲杠直徑小,滾柱齒的齒數、模數也都小,那就得考慮根切變位,還要確保絲杠中心線和齒輪中心線重合等問題。(2)行星滾柱絲杠(PRS)裝配起來比較難,主要是螺紋加工和輪齒加工的相位匹配問題。得保證滾柱螺紋和螺母螺紋能嚙合,滾柱齒和內齒圈也能嚙合,還得方便多個滾柱按順序安裝。(3)要對效率、壽命和承載能力進行分析,構建完整的剛度、強度分析體系。不過,螺紋牙型角、接觸角這些參數對總體效能影響到什麽程度,還缺乏實驗研究。(4)傳動部件主要靠捲動摩擦來傳輸動力,所以摩擦、潤滑以及摩擦生熱等也是以後要研究的問題。(5)行星滾柱絲杠(PRS)作為電動機械作動器(EMA)的執行部件,在各行各業都廣泛使用,在航空、航天領域更是如此。PRS的設計要和EMA系統相匹配,在保證力學效能的同時,還得兼顧行業套用要求。(6)目前已經有5種PRS的結構形式。探索設計新的PRS結構形式也是很有意義的,比如行星齒輪系統裏的串聯、並聯結構形式等。(7)為了達到PRS傳動的工作效能和精度要求,螺紋滾道的硬度一般是HRC58 - 62,滾柱的硬度一般是HRC62 - 64。在熱處理方面,通常根據材料的選擇和實際工作環境來確定。
滾道加工的核心要素是螺紋加工,滾珠絲杠和行星滾柱絲杠(絲杠和滾柱都包括)加工的核心步驟也是螺紋加工。傳動級絲杠通常用輥軋法制造,定位級絲杠對精度要求更高,一般是車、銑、磨結合起來制造,精度由磨削環節決定。
螺紋加工的精度會直接對系統的傳動精度、使用壽命和平穩性產生影響,所以最佳化螺紋加工技術是提高PRS整體效能的關鍵。螺紋是按特定參數設計的,制造工藝主要是成型加工,像旋風銑削、磨削加工、硬態車削、滾壓成型這些。據黃祖堯【滾珠絲杠螺紋制造技術向高效、低耗、綠色方向發展】所說,在全球環保浪潮的推動下,絲杠螺紋制造從「白鋼刀挑扣」發展到高速硬車削,從螺紋磨削拓展到高速旋風銑削(軟、硬),從切削加工轉變為無屑精密滾軋成形制造,從低檔、低速、低精度朝著高檔、高速、高精度發展,高效、低耗、綠色已經成為21世紀螺紋制造技術發展的主要方向。
5.1、輥軋路徑:精密滾軋技術在提高效率、降低成本方面潛力巨大。
絲杠螺紋滾軋成形技術是基於金屬塑性變形理論的,有很多優點,像材料利用率高,產品機械強度也高(抗拉強度能提高20% - 30%,疲勞強度能提高20% - 40%,抗剪強度能提高5%),使用壽命長,絲杠螺紋的尺寸和導程精度的同一性、互換性比較高,生產周期短,制造成本也低。工業傳動和定位用到的滾軋絲杠產品有兩種:滾軋梯形絲杠副RLS(RollingLeadScrew)和滾軋滾珠絲杠副RBS(RollingBallScrew)。早時候的產品精度不高,大多用在各類工業機械的動力傳遞和快速驅動上。不完全統計的話,全球制造滾珠絲杠的專業廠家裏面,有30多家有滾軋器材生產線,按標準系列批次生產RBS和RLS產品。不過大多數企業的RBS產品精度長時間都在T7 - T10級這個水平。冷軋滾珠絲杠是用冷加工工藝模具做出來的,開模工藝自動化程度高,批次生產的時候成本低、效率高,精度一般在P7級左右,在器材裏是做傳動部件的。
HPR(HIGHPRECIDIONROLLING),也就是精密滾軋技術。
國外有一些制造RBS的知名企業,像Rexroth、Thomson、WarnerElectric、Eichenberger、NSK、THK這些企業。它們有新一代高效能的CNC精密滾軋機,而且掌握了核心技術,在大批生產的時候,能讓RBS的精度穩定在P5 - P7級,部份還能達到P3級。精密RBS從低水平發展到高水平、從量的變化發展到質的變化,總結起來有下面這些原因:(1)新一代滾軋機精度高、剛性強,數控化和智能化的水平很高,在軋制的時候,會根據金屬塑性變形的情況和滾軋力的變化,動態調整滾軋的工藝參數。(2)軋輥的進給方式變了,從一個軋輥單向進給,變成以絲杠(精胚)中心線為標準,用電腦控制一對伺服交流電動機,讓雙軋輥同步向中心做微米級的精密徑向進給。(3)對精密軋輥進行3D最佳化設計,按照材料變形的規律對導程(螺距)和齒形進行修正。使用優質合金鋼,這樣就大大提高了制造精度和工作壽命。(4)用來做RBS滾軋精胚的材料,品牌和質素都穩定可靠(由鋼廠定點供應,不混雜其他材料),材料合金元素的純凈度、塑性應變能力、延伸率,還有微量元素的含量、晶粒的球化程度等,都能滿足冷滾軋的要求。(5)那些RBS產品做得好的企業,在RBS生產線上都配有CNC中頻淬火器材、自動矯直機、螺紋滾道拋光器材,還有控制產品質素的全套檢測儀器等。
精度達到P3 - P5級的精密RBS有機會進入CNC機床和CNC工業裝備領域了。德國的Rexroth公司在精密RBS方面很有成績,這個公司已經決定全力批次生產RBS。據博世力士樂(中國)有限公司業務總經理說,在他們銷售的BS總量裏,RBS能占到80% - 90%,磨削BS只占10% - 20%。要是把規格和精度等級相同的RBS和磨削BS作個比較,就會發現RBS有「同級質優」這種「芯裏美現象」。冷軋滾珠絲杠軸端有三種加工方法:退火後車制、磨削、硬車削。冷軋滾珠絲杠軸端加工時,材料硬度高,加工余量也大。很多企業用傳統工藝加工,就是軸端先退火,再車削,然後軸端淬硬。這種方法因為軸端要反復進行軟化和硬化熱處理,會讓冷軋滾珠絲杠效能不穩定。還有企業用磨床對冷軋滾珠絲杠軸端進行大余量磨削加工。隨著刀具材料和制造技術不斷進步,硬車削大余量加工淬硬鋼這一工藝變得簡單高效了。可以選擇CBN這種高硬刀具,它適合加工硬度在HRC45 - 79之間的材料。這個工藝省掉了退火和淬火熱處理環節,避免了退火後二次淬火的問題,也徹底解決了用砂輪大余量磨削加工的難題。
5.2、先車後磨這種經典工序精度挺高的,不過生產效率還有待提高。
如今,大多數滾珠絲杠制造廠家都是采用先車削後研磨的方式來加工生產的。先把原材料車削到一定的精度,接著用專門的絲杠磨床先粗磨再精磨到要求的尺寸。這種加工方式的優點是精度不錯,成本也低,國內的專用絲杠磨床就能做到。不過它也有缺點,就是加工效率低,單只螺母單道磨削工序要花13 - 15分鐘,而且磨削產生的大量粉塵和油煙對操作工的身體健康有很大危害,對環境的汙染也很嚴重。
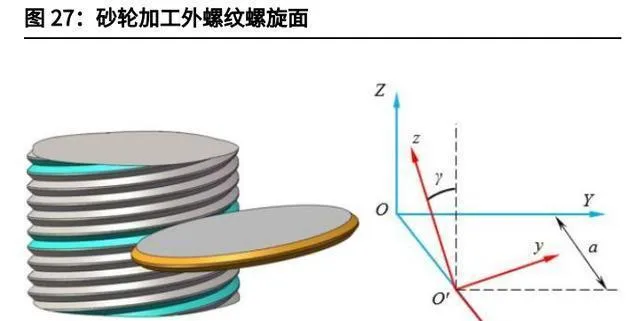
砂輪磨削:第12道工序是對滾珠絲杠工作滾道進行淬硬熱處理,所以工作滾道粗加工時,最常用砂輪磨削來制出90°V型槽。不過,這種工藝經磁力探傷檢測後,會發現滾珠絲杠滾道的圓弧上有沿軸線方向或者網狀的裂紋。可以用「小磨量多次進給」的工藝方法,或者「磨——工作滾道表面溫度穩定——磨」的技術方法來解決,這樣能最大程度降低滾珠絲杠工作滾道表面的磨削應力和磨削熱量,盡量避免出現磨削裂紋或者燒傷現象。
磨削滾珠絲杠的加工工藝大概有20多道工序呢,這得花30到45天的時間,耗時很長,效率又低,成本還高。在加工工藝裏,材料熱處理和工作滾道粗加工是兩個重點。砂輪磨削、硬車削、旋風銑削是磨削滾珠絲杠工作滾道粗加工常用的方法。
5.3、熱處理:這是個隱形壁壘,精度得控制好。
滾珠絲杠成品零件的制造質素和精度受材料及熱處理方式的影響很大。滾珠絲杠常用GCr15高碳鉻軸承鋼這種材料。軸承鋼淬火加低溫回火後,硬度高、組織均勻、耐磨、接觸疲勞強度也高,不過它塑性一般、切削效能中等、焊接效能差還存在回火脆性。所以在磨削滾珠絲杠粗加工前,得先對軸承鋼材料做預先熱處理,透過球化退火讓GCr15材料裏的碳化物球化,形成在鐵素體基體上均勻分布的球狀或顆粒狀碳化物組織,這樣能降低材料組織硬度,提升材料塑性,改善材料的金屬切削加工效能。軸坯加工完後,要把磨削滾珠絲杠工件的工作表面(滾道)和加工基準(中心孔)淬硬,為後面滾珠絲杠開滾道把材料的力學效能準備好。每次金屬切削加工都會產生應力變形,為了消除應力變形對工件的不良影響,關鍵的質素控制點都得進行時效去應力處理,這樣才能控制好工件的加工質素。合理安排滾珠絲杠的材料選擇、熱處理內容和順序,就能最大程度保證磨削滾珠絲杠零件的表面接觸強度、整體剛性、耐摩擦性等工程力學效能指標,滿足它在尺寸精度、幾何公差、表面粗糙度方面的零件工作配合技術要求。
滾珠絲杠中頻淬火之後,金相組織有了改變,軸向尺寸也就跟著變了。在螺紋粗加工的時候,得摸清楚淬火時這種變化的規律,這是個必須解決的難題。不同鋼廠的GCr15軸承鋼,冶煉爐號(批次)不一樣,即便尺寸規格和淬火工藝是相同的,軸向變形量也還是不同,所以掌握變形規律很不容易。要是淬火前導程修正量不對,磨削余量就會偏移,滾道表面硬化層的厚度就不均勻了,產品的摩擦特性、接觸剛度和使用壽命最終都會受到影響。
5.4、旋風硬銑:這是一種新興工藝,生產效率和產品精度都能兼顧。
高速旋風銑削硬度在HRC60以上的淬硬絲杠,這是一種新的高效綠色加工法。加工的時候,工件一次銑削就能搞定,也不用切削液,加工效率差不多是磨削加工的5 - 8倍呢,國外捲動部件加工行業裏用得挺多的。高速硬切削這種加工技術是基於高速切削理論的,就是直接對HRC55 - 65的高硬度金屬材料進行車削或者銑削加工。它的理論根據是Salomon博士的理論,這個理論說當切削速度提高到一定程度的時候,切削溫度不但不上升,反而會下降。
在數控車床上安上高速銑削螺紋動力頭,對於硬度在62 - 65HRC的淬硬軸承鋼GCr15工件,用刀盤上6把或者8把均勻對稱分布的高強度成型銑刀來加工。刀盤旋轉軸線和工件軸線有個偏心距e,銑刀就借著這個偏心距依次進行切削,而且這兩個軸線的夾角就是螺紋的螺旋角。旋風銑削的時候,刀盤和工件朝著同一個方向轉,這就是順銑。工件轉速低,每分鐘就轉4 - 10圈,刀盤轉速高,每分鐘能轉600多圈。工件每轉一圈,刀盤就沿著工件軸線移動一個螺紋導程那麽長的距離,這樣就能把整個螺紋滾道加工出來了。
國內這邊,漢江機床自己研發出了HJ092型九軸三聯動CNC絲杠硬旋銑床(6米、8米)。這台機床用咱們國家自己產的CBN磁碟機銑刀,對硬度達到62HRC的滾珠絲杠進行硬旋銑之後,精度能達到P4級,表面粗糙度Ra在0.4到0.6μm之間。
旋風硬銑能達到現在的精度,靠的是下面這些方面:(1)高速硬旋銑是以德國切削物理學家薩洛蒙(Carl Salomon)的高速切削理論為基礎的。按照「Salomon曲線」,切削速度一旦超過「臨界速度」,單位切削力會下降30%還多,而且95%以上的切削熱還沒來得及傳給工件,就被很多呈「,」狀的小切屑迅速帶走了。切削力小,工件溫度又低,這對減小絲杠的徑向和軸向變形很有好處。(2)新一代的CNC硬旋銑床大大增強了「機床—旋風銑頭及刀具——工件(安裝、支承定位)」這個系統的動剛度。高速旋銑的時候,機床的激振頻率特別高,這個範圍遠遠超出工藝系統的固有頻率。所以振動小,工作平穩,有助於降低Ra,提升加工表面的質素。(3)高檔CNC硬旋銑機床在控制技術、旋銑刀盤電主軸直驅技術、誤差適時補償技術還有智能化水平等方面都有很大的提高。(4)在刀具系統上,采用先進的刀片材料(像CBN、PCBN)以及高精度的CNC刀片刃磨(修復)技術和機床,並且提高刀片在刀盤上的安裝和對刀的精度。
高乃坤等人檢測了大量旋銑加工的滾珠絲杠的螺紋精度,還測試了其裝配後的產品效能,對磨削加工與旋風硬銑加工的滾珠絲杠各項質素參數進行了分析對比,得出如下結論:(1) 用成形刀具加工的絲杠,其滾道截形穩定性和中徑一致性,比磨削加工的絲杠明顯要好。(2) 統計精度檢測數據後發現,旋風硬銑絲杠在有效行程內的行程變動量(線性),相比磨削加工的絲杠明顯更優。(3) 旋風硬銑絲杠加工時溫升低,徹底消除了螺紋磨削後滾道表面可能出現的退火現象,所以絲杠效能質素比磨削加工的絲杠好。(4) 對旋風硬銑滾珠絲杠裝配後的綜合效能進行測試,其動態預緊轉矩的波動值和運動平穩性都比磨削加工的絲杠好。(5) 統計精度檢測數據可知,現在只有極少數絲杠能達到P2級精度,所以在高精度絲杠加工方面,和磨削加工的絲杠相比還有差距。
在中國,很多機械制造公司都用旋風銑削,20世紀60到70年代推廣了旋風銑削技術,主要是用於一般鋼材各種螺紋軟銑的旋風銑頭。之後,大連機床廠、北京機床研究所、濟寧博特、南京工藝這些地方開始用旋風銑床來高效粗加工精密滾珠絲杠。2004年,南京工藝裝備廠第一次買了德國Leistritz公司的PW160型CNC硬旋銑機床,2009年又買了這個公司新出的PW300HP型10mCNC硬旋銑機床,用這個機床能精銑出整體800mm以上的大型滾珠絲杠副。山東濟寧博特精工股份有限公司也引進了螺紋旋風硬銑削器材。國內生產滾珠絲杠副的大連高金、濟寧博特、南京藝工都有旋風銑加工器材,可旋風硬銑機床在國內沒快速推廣開,主要是以下原因:(1)旋風硬銑對滾珠絲杠的原材料和刀具要求高,國產的材料和刀具達不到加工要求,這就使得加工成本比較高,所以滾珠絲杠原材料和刀具國產化是降低硬銑加工成本的關鍵。(2)旋風硬銑機床是精密器材,技術附加值高,8m的旋風硬銑機床售價折合人民幣大概1200萬。(3)旋風硬銑削的加工精度受很多因素影響,而且中國數控技術比較落後。
5.5、硬態車削:螺紋滾道的半精加工方案
硬態車削呢,就是用超硬的刀具對硬度超過50HRC的材料進行精密加工的工藝。一般來說,刀片材料會用硬質合金、陶瓷、PCBN還有金剛石。把淬硬材料的車削當成粗加工或者最後加工、精加工的新方法、新工藝,這樣就不用磨削加工技術了。用PCBN刀具精車的話,表面粗糙度能達到0.32μm,這就和半精磨的水平差不多了;在一台機床上就能把毛坯加工成成品,加工效率提高了不少。
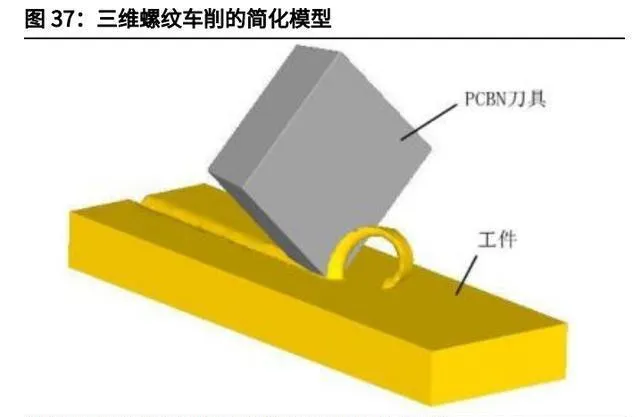
有些企業會直接運用硬車削這種先進技術,來對滾珠絲杠工作滾道做開粗加工,從而車出90°V型槽。它有這些好處:(1) 硬車削一般都是高轉速、大切深,金屬切除的效率能達到磨削加工的3倍還多。(2) 硬車削加工時,零件裝夾一次就能把多個表面加工好,像車外圓、車內孔、車槽之類的。可磨削加工得多次安裝才能完成,這樣就會有二次安裝誤差。(3) 硬車削產生的熱能一半以上都被切屑帶走了,不會像磨削加工那樣出現表面裂紋和燒傷的情況。所以硬車削能讓工件有不錯的加工精度和表面粗糙度,能符合形位公差技術要求,比如圓度、位置精度這些。
在高剛性硬車刀具系統和硬車機床系統有了突破性發展,並且市場環境對滾珠絲杠高品質、低成本的要求不斷提高的時候,以車代磨的硬車技術就出現了。螺紋滾道硬車削是一種新的螺紋滾道粗加工技術,它最大的好處就是在粗加工螺紋滾道時,不會像磨削那樣因為切削熱讓絲杠硬度降低,從而出現可靠性差的問題,而且加工效率高,沒有油煙粉塵汙染,很環保。海外的滾珠絲杠制造廠家大量采用以車代磨螺紋滾道的粗加工技術,在國內因為技術有限,目前用得比較少。硬車粗加工的滾珠絲杠,圓弧滾道的圓度在0.008mm以內,圓柱度在0.01mm以內,表面粗糙度值Ra≤1.6μm,這是符合滾珠絲杠加工技術要求的。而且,它的生產效率比磨制高不少。像直徑40、導程10、長度1M的滾珠絲杠,磨削大概要花70到100分鐘,要是用硬車的話,只要30到45分鐘就夠了。滾珠螺紋滾道硬車不只是在效率上比螺紋滾道硬磨削提高了很多,生產制造成本也降低了不少,因為不需要那麽多昂貴的專用外螺紋磨床了。所以,滾珠螺紋滾道硬車會被越來越廣泛地使用,越來越多的滾珠絲杠廠家會把滾珠螺紋滾道硬車當作螺紋滾道半加工的最好工藝方法。
張廣明在【滾珠絲杠滾道硬車加工技術研究】裏提到,歐洲和日本對於高精度的滾珠絲杠螺紋,都是淬火前軟車補償、淬後磨削。國內有些廠商也試著用這種淬火前軟車補償、旋銑補償,淬火後磨削的加工法,還做了好多工藝驗證試驗,就盼著能解決、打通這個主要瓶頸呢。不過,因為國內滾珠絲杠用材的穩定性不行,淬火前後滾珠絲杠變形沒規律,這就使得軟車補償、旋銑補償工藝有一定技術風險。硬車加工能代替傳統工序裏滾珠螺紋滾道的粗磨和半精磨工序。日本和中國台灣地區,以車代磨螺紋滾道的粗加工技術用得比較多。國內的大連高金數控集團最先打破這種技術壟斷,和大連機床集團一起研制開發了滾珠絲杠專用的高剛性數控硬車機床。經過長時間試驗,得到了滾珠絲杠硬車的一手數據,形成了完整、獨立自主的硬車技術體系。滾珠螺紋滾道硬車削的效率雖然比不上硬旋銑加工,但比螺紋滾道硬磨削效率能提高2到3倍,而且還省了好多外螺紋磨床,大大降低了生產制造成本。一般來說,滾珠螺紋滾道硬車削的生產制造成本是螺紋滾道硬磨削成本的三分之一到二分之一,是螺紋滾道硬旋銑加工成本的四分之一到三分之一。從成本和效率綜合來看,滾珠螺紋滾道硬車削工藝發展前景很廣闊,會是未來滾珠螺紋滾道半精加工的首選工藝方案之一。
要完整地加工出螺紋,得靠刀具多次進刀車削才行。螺紋車削加工有三種進刀的法子,就是徑向進刀、側向進刀還有互動式進刀。這三種法子都能加工出輪廓一樣的螺紋,不過受到的切削力、刀具的磨損情況、切削形貌以及工件的表面質素是不一樣的。
車螺紋的時候,進刀量咋分配,這對工件加工質素和刀具能用多久有影響。最後那一次進刀,可是決定了螺紋面最後的表面質素呢。所以,把進刀量分配得合理些,螺紋車削的效率就能大大提高。
【6、 工藝路線對比:精度、成本、效率、環 境】
在精密螺紋磨削、精密硬旋風銑削、精密滾軋成形這三種工藝路線裏:精密螺紋磨削的好處是對絲杠材料沒特殊要求,精度最高能到P0級,不好的地方是磨削效率低、生產工序多、制造成本高,一般用於高規格精度絲杠螺紋的精加工;精密硬旋風銑削對絲杠材料的要求處於中等水平,精度最高可達到P3級,Ra等於0.4μm,表面質素比螺紋磨削要好,不足之處在於關鍵器材前期投入大,對刀調整比較麻煩,適合加工有一定批次的產品,效率比磨削高但比冷滾軋低;精密滾軋成形對絲杠材料要求最高,精度最高能達到P3 - P5級,Ra等於0.5 - 0.8μm,表面光滑,處於壓應力狀態,能夠實作標準化、系列化的大批次生產,適合單機快速出庫存供貨。
在環境影響這塊兒:精密螺紋磨削是濕切削,能耗、油耗還有水耗都挺高的,並且得想辦法消除磨粒、金屬粉塵和油霧對工人健康的影響。精密硬旋風銑削是幹切削,工序少,能耗、油耗和水耗都比磨削低,在封閉的環境裏高速旋銑,噪音小,沒多少油屑還方便集中處理,對環境的汙染也小。精密滾軋成形屬於低耗無屑的加工方式,材料利用率能達到80%以上,沒有油霧和粉塵,對環境的汙染小。
成本對比:滾珠螺紋滾道硬車削的效率比不上硬旋銑加工。不過,它的效率要比螺紋滾道硬磨削高出2 - 3倍,而且還省了好多外螺紋磨床,生產制造成本也大大降低了。一般來說,滾珠螺紋滾道硬車削的生產制造成本是螺紋滾道硬磨削成本的三分之一到二分之一,是螺紋滾道硬旋銑加工成本的四分之一到三分之一。從成本和效率這兩方面來看,滾珠螺紋滾道硬車削工藝的發展前景很廣闊,會是以後滾珠螺紋滾道半精加工的首選方案中的一個。
6.1、國內在專利、經驗和原材料方面存在差距。
6.1.1、專利:國內一直在持續追趕呢。
行星滾柱絲杠技術的相關專利在20世紀40年代就有了。1988年之後的專利申請趨勢能分成兩個階段,一個是萌芽期(2009年之前),另一個是成長期(2010年到現在)。萌芽期的時候,每年申請專利的數量都不超過15項。這時候的技術主要是行星滾柱絲杠總體結構設計技術,還有行星滾柱絲杠和螺母螺紋的加工制造技術。主要的申請人有日本豐田公司(TOYOTA)、德國舍弗勒技術公司、瑞典滾珠軸承制造公司(SKF)、日本精工株式會社(NSK)等。成長期裏,專利數量總體上是快速增長的,這個時期又能分成兩個階段。第一階段是2015年之前,這個階段專利數量增長的動力主要來自德國、瑞典、法國、日本這些國家,技術主要是行星滾柱絲杠總體結構設計方面的。第二階段是2016年之後,中國專利數量在總申請量裏占的比重一年比一年大,技術主要涉及行星滾柱絲杠總體結構設計、行星滾柱絲杠和螺母螺紋加工制造、行星滾柱絲杠副傳動精度和效率測量、剛度特性試驗這些方面。
在行星滾柱絲杠螺紋加工工藝研究的專利方面,有螺紋硬態車削工藝研究、螺紋磨削用砂輪的廓形修整和保持技術研究、深孔內螺紋制造技術研究、大長徑比外螺紋制造技術研究。在深孔內螺紋制造技術研究方面,專利數量比較多,其技術主要是關於內螺紋采用磨削、研磨、車削、銑削的加工方法與裝置,還有加工過程中磨削力預測、監測的方法與裝置。行星滾柱絲杠副的總體結構設計技術、螺紋磨削用砂輪的廓形修整和保持技術、深孔內螺紋制造技術研究、傳動效率測量試驗研究,這些方面每年的專利申請數量較多,而且是呈增長趨勢的,在當下高精度行星滾柱絲杠副技術領域,這些都是熱點。
6.2、經驗得不斷積累,這樣精度才能提高。
國內有些生產廠家也陸續購置了旋風硬銑機床,不過,滾珠絲杠的加工精度和國外相比,差距還很大。主要是下面幾個原因:其一,對旋風硬銑的機理和實驗研究不足;其二,國內外生產企業的工件材料不一樣,在控制工件熱變形誤差這方面沒有能參考的數據。關於硬車:滾道硬車削工藝的效率關鍵在於控制滾道的留量,而滾道留量的大小是由導程、鋼球大小、滾珠絲杠的長度以及滾珠絲杠自身的綜合情況等因素決定的。滾道硬車削得考慮車削後的工藝走向,一般來說,滾道硬車削之後還要做低溫時效處理,絲杠會出現彎曲變形以及長度方向的伸縮,這些變形會因為滾珠絲杠的長徑比、導程、鋼球大小、絲杠材質的純凈度等因素的不同而不一樣。
補償:(1)硬件補償的原理是,用機械方法得出絲杠全行程的螺距誤差分布曲線,然後在絲杠累積螺距誤差值達到一個脈沖當量之處安裝擋塊。機床工作台移動時,機床控制開關會給控制電路發送誤差補償訊號。(2)軟件補償的原理是,把理想加工和用螺距誤差測量儀這兩種狀態下得到的絲杠螺距誤差值進行對比,得出螺距誤差分布情況與補償檔,把補償數據輸入數控系統後,就能為下次銑削加工提供補償值了。這種定點補償法能提高定位精度。
6.2.1、原材料方面,上下遊得協同起來,提高純凈度。
6.3、發展走向:針對量產任務,器材和原材料都要升級。
華經產業研究院的數據顯示,2022年中國滾珠絲杠的需求量是1555萬根,我們估算全球需求量在7700萬根左右;IHSMarkit的數據表明,2022年中國行星滾柱絲杠銷售了1.0萬根,全球銷售8.6萬根。滾珠絲杠現在已經被廣泛運用了,可行星滾柱絲杠的使用範圍比較小。朝著人形機器人「百萬級」量產這個目標去看,行星滾柱絲杠要量產,壓力可不小。從實作高效規模化生產的角度來講,絲杠制造技術的發展趨勢有下面幾點:(1)生產器材專業化。國內滾珠絲杠生產企業現在用的加工器材大多是常規通用器材,專有器材、工具和技術特別少。為了應對市場競爭越來越激烈的需求,會有很多專業化生產器材、工具被研發和套用。比如說,會研發套用專用磨具、刀具和夾具,研發套用螺母加工專用車銑中心和磨削中心,研發套用硬加工機床,還有自動生產線等。(2)銑制、軋制滾珠絲杠將逐漸取代磨制的中等精度等級滾珠絲杠。因為數控系統補償技術進步發展得很快,對滾珠絲杠精度不像以前那麽苛求了,中等精度等級滾珠絲杠會被更廣泛使用,銑制、軋制滾珠絲杠在滿足中等精度等級要求的情況下,會占據更大的市場份額。(3)對於高精度等級滾珠絲杠,對其磨削技術的要求會越來越高,不但要更精密,而且要更高效。在航天、航空和軍工這些電子系統容易受幹擾的領域,高精度的磨制滾珠絲杠有著不可替代的地位。(4)滾珠絲杠專用材料會被研發和套用。隨著滾珠絲杠企業轉型升級不斷推進,滾珠絲杠專業化生產會達到前所未有的程度,原材料作為滾珠絲杠的根本,肯定會被重視和研究。
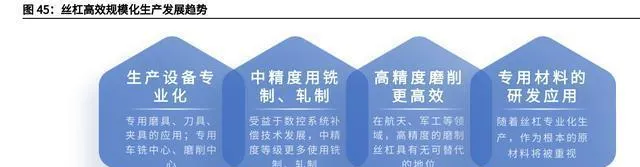
(這篇文章只是用來參考的,不代表我們的任何投資方面的建議。要是想使用相關資訊的話,請檢視報告原文。)
精選報告來源:【未來智庫】。未來智庫 - 官方網站