(报告出品方/作者:华宝证券,胡鸿宇)
1. 碳化硅产业链包括上游衬底和外延、中游器件、下游应用
以碳化硅材料为衬底的产业链主要包括碳化硅衬底材料的制备、外延层的生长、器件制造以及下游应用市场。从工艺流程上看,碳化硅一般是先被制作成晶锭,然后经过切片、打磨、抛光得到碳化硅衬底;衬底上生长单晶外延材料。外延片经过光刻、刻蚀、离子注入、沉积等步骤制造成碳化硅功率器件和碳化硅射频器件。将晶圆切割成die,经过封装得到器件,器件组合在一起放入特殊外壳中组装成模组。
碳化硅产业链附加值向上游集中,衬底和外延的成本占比最高。根据CASA整理的数据,产业链中,碳化硅衬底和外延的成本分别占整个器件成本的47%和23%,为产业链中价值量最大的两个环节,相比硅基器件、价值量显著倒挂。
2. 衬底:产业链价值量占比高,良率和订单是胜负手
2.1. 技术及资本密集型产业,是碳化硅降本的关键环节
衬底在碳化硅产业链中价值量最高,高达 47%。碳化硅产业链附加值向上游集中,衬底和外延的成本占比最高。根据 CASA 整理的数据,产业链中,碳化硅衬底和外延的成本分别占整个器件成本的 47%和 23%,为产业链中价值量最大的两个环节,相比硅基器件、价值量显著倒挂。
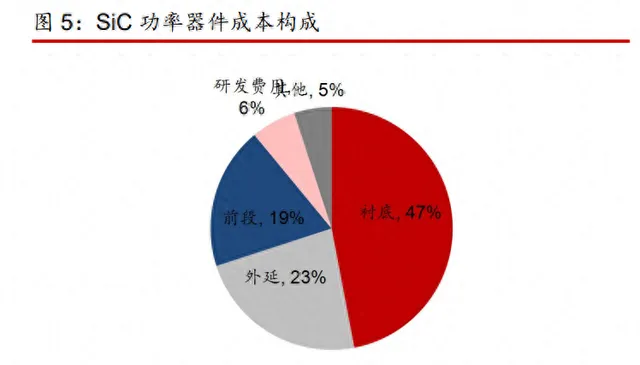
衬底属于技术密集型行业,生产工艺水平直接影响良率。从生产工艺来看,以高纯碳粉、高纯硅粉为原料合成碳化硅微粉,在碳化硅单晶炉中进行碳化硅单晶生长,再经过晶碇切磨抛及清洗等工序,产出碳化硅衬底。衬底的质量影响下游外延和器件的质量,优质的衬底可以抑制外延生长缺陷和器件性能退化,但衬底的控制难度又较大,其生产过程中的每个环节都具有较高技术要求,当每个环节都具有一定良率损耗时,合在一起就会产生指数级递增的损耗,碳化硅衬底龙头 Wolfspeed 良率也仅为 65%,这其中技术难度最高的又是长晶环节:
原料合成:获得高纯度碳化硅粉难度高。将高纯硅粉和高纯碳粉按一定配比混合,在2,000℃以上的高温下反应合成碳化硅颗粒。再经过破碎、清洗等工序,制得满足晶体生长要求的高纯度碳化硅微粉原料。难点在于碳化硅粉料合成过程中的环境杂质多,难以获得高纯度的粉料;作为反应源的硅粉和碳粉反应不完全易造成 Si/C 比失衡;碳化硅粉料合成后的晶型和颗粒粒度难控制。 晶体生长:长晶是技术难度最高的环节,工艺水平决定良率。长晶技术包括 PVT 法(物理气相传输法)、溶液法和高温气相化学沉积法等,目前商用碳化硅单晶生长均采用 PVT 法。具体原理为将高纯碳化硅微粉和籽晶分别置于单晶生长炉内圆柱状密闭的石墨坩埚下部和顶部,通过电磁感应将坩埚加热至2,000℃以上,控制籽晶处温度略低于下部微粉处,在坩埚内形成轴向温度梯度。碳化硅微粉在高温下升华形成气相的Si2C、SiC2、Si 等物质,在温度梯度驱动下到达温度较低的籽晶处,并在其上结晶形成圆柱状碳化硅晶锭。
长晶有以下难点: 1) 热场控制难:密闭高温腔体监控难度高不可控制。区别于传统硅基的溶液直拉式长晶设备自动化程度高、长晶过程可观察可控制调整,碳化硅晶体在2,000℃以上的高温环境中密闭空间生长,且在生产中需要精确调控生长温度,温度控制难度高;2) 晶型控制难:生长过程容易发生微管、多型夹杂、位错等缺陷,且相互影响和演变。微管(MP)是尺寸为几微米到数十微米的贯穿型缺陷,是器件的杀手型缺陷;碳化硅单晶包括 200 多种不同晶型,但仅少数几种晶体结构(4H 型)才是生产所需的半导体材料,生长过程中易产生晶型转变造成多型夹杂缺陷,因此需要精确控制硅碳比、生长温度梯度、晶体生长速率以及气流气压等参数;此外,碳化硅单晶生长热场存在温度梯度,导致晶体生长过程中存在原生内应力及由此诱生的位错(基平面位错BPD、螺旋位错 TSD、刃型位错 TED)等缺陷,从而影响后续外延和器件的质量和性能。3) 掺杂控制难:必须严格控制外部杂质的引入,从而获得定向掺杂的导电型晶体;4) 生长速度慢:碳化硅的长晶速度非常慢,传统的硅材料只需3 天就可以长成一根晶棒,而碳化硅晶棒需要 7 天,这就导致碳化硅生产效率天然地更低,产出非常受限。
结合密闭生长,容易发生诸多缺陷,因此很难在生长过程中及时发现并进行调整,需要等到每一次生长完成后再不断改进工艺,这不仅仅需要原理的认识,更需要时间的积累,是一个非常漫长且艰难的过程。 碳化硅衬底由于加工环节复杂且耗时,设备投资额较高属于资本密集型产业。从碳化硅衬底的制备流程来看,需要碳化硅粉料合成设备、长晶炉、切片机、研磨机和抛光机、量测仪器等,其中最为关键的核心设备就是长晶炉,由于晶体生长速度非常慢且良率低,长晶过程需要大量的单晶炉,要获得一定规模效应以降低成本就需要大量设备投入。单晶炉国产化率较高,国内有外采和自研两种形式。那些技术积累水平较深发展时间较长的衬底厂商大多自研长晶炉,大多数后进入者采用外采的方式。国内的碳化硅单晶炉设备供应商主要有北方华创和晶升股份,两者在国内占有的份额超过 70%,国产化程度较高。全球范围看,国际主流半导体材料厂商经过数十年积累,其工艺和产品远领先于业界同行,多通过自研以锁定设备从而保持领先水平(如日本信越化学和日本胜高),部分选择向 S-TECH Co, Ltd.等公司采购设备。由于设备认证周期较长、厂商更换成本、稳定性风险等因素,国产供应商尚未实现国际主流碳化硅厂商的设备供应。
晶锭加工:将碳化硅晶锭使用 X 射线单晶定向仪进行定向,之后通过精密机械加工的方式磨平、滚圆,加工成标准直径尺寸和角度的碳化硅晶棒。对所有成型晶棒进行尺寸、角度等指标检测。 晶棒切割、研磨抛光及清洗:容易发生翘曲、表面划伤、表面粗糙度高等问题。碳化硅硬度与金刚石接近,切割、研磨、抛光技术难度大,加工过程中存在易开裂问题,加工完成后的衬底易存在翘曲等质量问题;为了达到下游外延开盒即用的质量水平,需要对碳化硅衬底表面进行超精密加工,以降低表面粗糙度、表面平整度并达到严苛的金属、颗粒控制要求。根据英飞凌的数据,在传统的往复式金刚石固结磨料多线切割方法下,在切割环节对整体材料利用率仅有 50%,经过抛光研磨环节后,切损耗比例则高达 75%,可用部分比例较低。
2.2. 国产厂商进展不断加速,良率和订单是胜负手
2.2.1. 国产厂商顺应产业趋势,加速释放产能
供给端,海外厂商在 SiC 衬底赛道具备先发优势,国产厂商加速释放产能。根据Yole的数据, 2022 年全球碳化硅衬底市场中,美国 Wolfspeed、美国Ⅱ-Ⅵ和日本Rohm(收购德国 SICrystal)三家企业合计占据全球约 72%的市场份额。中国公司天科合达、天岳先进努力追赶,2022 年导电型衬底合计实现营收 1.04 亿美元,合计占比15%,同比+5pct。
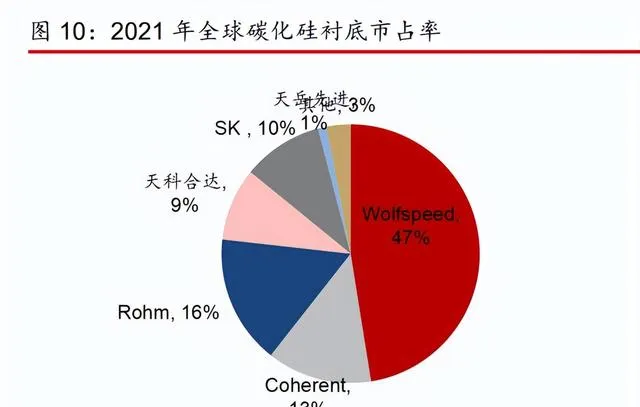
目前海外厂商加速碳化硅扩产进程,并大力布局 8 英寸。在碳化硅市场的全球格局中,海外企业由于早期投入和技术研发等优势,占据了主导地位。国际大厂产能加速扩张,积极布局碳化硅市场,争先恐后加码扩产。当前国际大厂仍以 6 英寸晶圆为主,为进一步提升产能,降低单个器件的成本,如英飞凌、Wolfspeed、ST、罗姆半导体等几年前就开始布局8寸碳化硅晶圆,并计划逐渐实现向 8 英寸晶圆的过渡。2015 年 Wolfspeed 便对外展示了8英寸碳化硅衬底,2019 年投入 10 亿美元进行 8 英寸晶圆厂建设,并于2022 年宣布投资13亿美元建设8英寸碳化硅衬底工厂,罗姆、意法半导体等诸多大厂均宣布投资建设8 英寸碳化硅衬底。虽然海外市场扩产脚步已纷纷转向 8 英寸,但实际大规模量产仍需到2025 年之后。
国内厂商加快扩产打造规模优势,8 英寸正在突破技术。下游应用市场庞大,无论是在新能源汽车还是光伏太阳能行业,国内都具备领先优势,在市场需求快速爆发的背景下,国内企业一方面加快对技术差距的追赶,另一方面也在积极投入大量资源进行产线的建设来满足市场需求和提供技术迭代的产业土壤,如天科合达、山东天岳等头部厂商持续加大投入进行扩产。国产 SiC 衬底厂商积极扩产,积极把握碳化硅市场窗口期。根据CASA统计,2022年我国衬底产能达到 94 万片/年。根据我们的不完全统计,预计 2023 年底我国衬底产能已超过130万片/年,增速迅猛。虽然扩产规模及速度较快,但能够规模化量产出货的只有天岳先进、天科合达、山西烁科、同光晶体、南砂晶圆五家,其他公司均处于研发或小批量阶段,而8英寸衬底量产出货的也仅山西烁科一家。
2.2.2. 良率和订单是企业盈利的关键
关注有效产能,企业需要平衡规模提高盈利能力。尽管各国产厂商规划产能增速极高,但由于碳化硅衬底存在降低缺陷密度等技术门槛,因此并非所有规划产能均能如期实际交付。核心设备目前大多都已实现国产化,单台设备投资额也不超过200 万,因此设备和资本并非关键卡点,更为重要的是工艺——掌握能够大批量生产的工艺,获得规模效应且提高良率,能够低成本、高质量、大批量供应才是真正的产业化。规划布局的投资规模并不等于实际能够达到的生产能力,并不等于能够实现的供货能力,更不对于能够获得的市场收入。由于目前技术工艺的不完善,衬底良率水平较低,需要通过打造规模效应打磨工艺、降低成本、获得客户从而形成正循环,但若布局的规模过大,投资量过大,包袱过重,运高成本极高,若盈利能力差更会造成失血过快,现金流断裂的风险;若布局的规模不够,则又会缺乏规模效应,市场竞争力不够。因此最核心的关键还是打磨工艺、投入研发、提升技术从而提高良率和盈利能力。
落到最后,更为直观且核心的就是能否拿到客户订单。衬底厂商关键在于盈利性,而盈利性又是由良率和订单决定的,能卖的出去产品且能盈利才是硬道理。目前国内厂商天岳先进、天科合达已成功供应英飞凌、博世等国际大厂。以天岳先进为例,2021 年及之前,天岳先进主要向无线电探测、信息通信行业厂商供应半绝缘型 SiC 衬底,2022 年公司实现将部分产能转移至导电型衬底后,陆续与国家电网等多个国内客户建立合作关系,并与英飞凌、博世集团等海外大厂签订长期合作协议,国内厂商进展飞速。
3. 外延:技术工艺设备相对成熟,国产化进展较快
3.1. 外延技术相对较为成熟,外延炉是核心设备
外延生长技术是碳化硅器件必不可少的环节。碳化硅外延晶片是指在碳化硅衬底的基础上,经过外延工艺生长出晶格一致、高纯度、低缺陷的特定单晶薄膜。由于采用升华法制备的单晶衬底无法实现对载流子浓度的精密控制,且无法有效降低晶体缺陷,因此需要在衬底上生长高质量的外延层,可以消除衬底中的某些缺陷,使晶格排列整齐,即外延生长技术是碳化硅器件必不可少的环节,外延质量对器件性能影响极大。 现阶段碳化硅外延制备主要通过化学气相沉积(CVD)方法,核心设备为CVD外延生长炉以进口为主。现阶段 SiC 薄膜外延的方法主要包括:化学气相淀积(CVD)、分子束外延(MBE)、液相外延法(LPE)、脉冲激光淀积和升华法(PLD)等。目前化学气相沉积(CVD)是最为普及的 4H-SiC 外延方法。其优势在于可以有效控制生长过程中气体源流量、反应室温度以及压力,改变成膜环境,可以精准控制外延生长参数,具有重复性良好,设备体积适中的优良特点。
高品质的碳化硅外延晶片生长受到外延生长过程中使用的CVD 外延炉、衬底等上游设备及材料的影响。国际上已经商业化量产的 SiC-CVD 设备有意大利LPE、德国Axitron和日本NuFlare 产品,这三家公司也占据了国内市场。由于起步晚和产业化水平低,国产设备在使用方便性、可调性、稳定性以及运行维护性方面与国外先进设备相比存在较大的差距,重点需要提升温场和流场的均匀性方面的技术。以芯三代、晶盛机电为代表的国内SiC-CVD设备厂家,产品各项指标已经达到甚至领先国际先进水平,国产 SiC-CVD 设备目前的重点是进入生产线接受大批量生产考验。
碳化硅衬底缺陷较多,需严格控制缺陷工艺难度较大。碳化硅衬底缺陷较多,主要包括微管缺陷 (Micropipe) 、多型缺陷、划痕缺陷包裹物缺陷、层错缺陷、贯穿螺型位错(TSD)、贯穿刃型位错(TED)和基平面位错(BPD)等。许多衬底缺陷会随着外延生长延伸到外延层中,部分缺陷会转换成外延缺陷,导致器件性能退化或直接失效。通过外延工艺优化可以有效降低或消除这些外延缺陷,从而改善器件良率。优质的碳化硅外延生长工艺不仅可以改进碳化硅衬底缺陷,还可以减少外延自身生长缺陷,大幅提升下游器件良率。
3.2. 外延环节国产化水平较高,有上下游向外延延申的趋势
全球来看外延环节呈现双寡头垄断,国内来看我国碳化硅外延国产化率水平不断提高。头部企业主要有 Wolfspeed(Cree)、DowCorning、II-VI、Norstel、ROHM、三菱电机、Infineon等,其多数是 IDM 公司,CR7 占据市场 90%份额。国内纯外延产业化比较成熟的企业有天域半导体和瀚天天成,其已研制成功 6 英寸碳化硅外延片,且基本实现商业化。国内外在碳化硅外延水平上的技术差距相对较小,均满足 3-6 英寸各种外延片的生产。目前各大厂商均在扩产8 英寸衬底产能。
国内外厂商纷纷扩产,且有上下游向外延环节延申的趋势。一方面,外延环节技术及工艺相对衬底较为成熟;另一方面,相较纯外延厂商,衬底厂商向下游外延延申可以直接为客户提供外延产品,具有更强的客户优势,晶圆厂商向上游外延延申可以缩短验证周期,具有更强的验证优势。目前碳化硅产业链已经呈现出了上下游纷纷向外延环节延申的趋势。但我们认为长期来看,当碳化硅产业链具有一定产业规模时,纯外延厂商作为代工厂为客户提供代工服务,那些具有规模优势的厂商仍然具备显著的成本优势。外延作为技术密集型和资本密集型行业,行业对技术和工艺要求较高,所需固定资产投入较大,固定成本分摊较大,因此规模优势有望带来成本优势。
4. 器件及模块:「上车方显英雄本色」
4.1. 晶圆制造环节技术难度仅次于衬底,需要使用特定设备
碳化硅材料特性导致的器件制造难度高,仍需要不断改进生产工艺。与硅基器件类似,碳化硅仅需要部分特定设备的升级或新开发,但这些新增设备又具有一定技术难度,可以这样理解,硅基器件发展超过 70 余年技术水平十分成熟,而碳化硅产业化也不过20余年,没有指路人可以参考,而其自身材料特性又造成了工艺改进慢的问题,我们此处所指的工艺是指能够达到批量生产的水平。碳化硅器件制造环节与硅基器件的制造工艺流程大体类似,主要包括光刻、清洗、掺杂、蚀刻、成膜、减薄等工艺。不少功率器件制造厂商在硅基制造流程基础上进行产线升级便可满足碳化硅器件的制造需求。在此,我们仅对其需要改进或新开发的设备进行探讨:由于碳化硅硬和化学稳定性高的材料特性,需要对干法刻蚀机进行升级。由于碳化硅具有很高的硬度和化学稳定性,碳化硅器件图形的加工较为困难。一般采用具有较高的刻蚀分辨率、选择性比较高的干法刻蚀方法加工,同时采用较大的刻蚀功率。碳化硅干法刻蚀机主要技术难点包括高洁净抗腐蚀工艺腔体设计与制造、高性能等离子体源技术等。目前国产化率水平较低,以海外厂商为主,海外厂商主要包括 Sentech、TEL、AMAT、Oxford 等;国内主要单位包括北方华创、中微半导体、中科院微电子所等。
由于碳化硅晶格难扩散的材料特性,需要新增高温离子注入机,产业化难度较大。区别于硅可以采用扩散或离子注入实现掺杂,碳化硅晶格难扩散,掺杂需要采用更高的注入能量,一般注入能量在 300KEV,基至需要到 700KEV 以上,高能量的离子注入的工艺制造成本高、流片效率低。高能量的离子注入会造成注入区域的损伤,为了解决注入离子激活问题,减少注入损伤,碳化硅注入一般需要在 500℃以上高温条件下进行。目前主要厂商以海外为主,包括ULVAC、NISSIN、AMAT 等,国内设备注入能量、束流大小、注入晶片温度等技术指标与国外相差不大,在产能等方面有待提高。根据泰科天润,高温离子注入机的保有量是衡量碳化硅晶圆产能的关键,目前国内 20 台左右,价格在千万级别,设备交期十分漫长,需要10个月到1年的时间,因此国内部分厂商也是由于缺少高温离子注入机而选择代工模式。
此外高温离子注入会造成损伤,因此需要高温退火炉。离子注入后仍需进行高温退火,才可以激活注入离子。N 型掺杂的退火温度一般需要大于 1200℃,P 型掺杂的退火温度一般需要大于 1600℃。实现碳化硅高温退火炉主要技术难点包括高温炉膛热场设计制造工艺,快速升温、降温与控温技术等。国外主要厂商主要包括 Centrotherm、日本真空等。由于碳化硅具有双元素,需要使用高温氧化炉来制备栅极氧化层。栅氧工艺不得不面对碳原子的反应,会形成碳相关杂质,需要高温氧化工艺,被业内成为皇冠级难度。与硅栅氧化工艺不同,碳化硅高温氧化时需要通入特定工艺气体促进碳原子的析出,增加了工艺的复杂性。主要技术难点包括无金属加热技术、抗氧化无污染高温炉膛设计与制造、高温氧化工艺等。因此面临硅产业无法借鉴,工艺需要摸案、设备配套较局限,高湿炉易受污染、长期稳定性差的难点。国外主要厂商包括 Centrotherm、东横化学等。国内主要厂商为北方华创等。由于碳化硅材料较硬且脆,需要使用更为坚硬的背面减薄机。背面减薄机主要技术难点包括高硬度材料减薄厚度的精确测量及控制,磨削后晶圆表面出现损伤层、微裂纹和残余应力,SiC 晶圆减薄后产生比 Si 晶圆更大的翘曲现象等。国外主要厂商包括日本不二越、Disco等,国内设备主要差距在于产业化程度有待进一步提高。
4.2. 器件仍以海外厂商为主,国内厂商不断跟进
目前,碳化硅器件的市场份额以海外厂商为主。2022 年意法半导体仍然居首,碳化硅功率器件营收增加到 7 亿美元;英飞凌次之,Wolfspeed 居于第三(仅包括器件),安森美以2.6亿美元的营收,超过了日本厂家罗姆晋级第四。部分原因在于安森美从碳化硅衬底、外延、裸片,再到单管和模块封装测试完全垂直整合,而罗姆在单价更高的碳化硅模块,特别是车规产品较少。按照 CR5 中部分企业公布的数据,以及 01 芯闻公众号的统计,2022年意法碳化硅功率器件的市占率低点为 37%,高点为 40%。英飞凌和 Wolfspeed 则占据了20%左右的市场。安森美紧随随后,份额为 14%。最后,根据数据来源的不同,罗姆市占率在7%-11%之间。
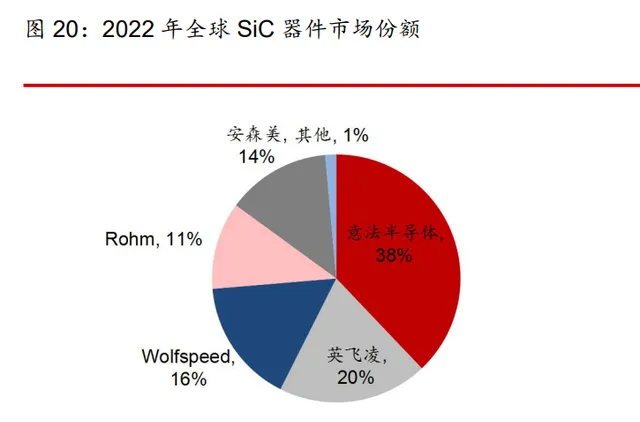
海外头部大厂一体化趋势明显,通过自建或收购或合作等方式加快上下游整合。头部五家大厂除英飞凌外,均采用垂直整合的方式自建衬底产能。2023 年英飞凌与ResonacCorporation签署了全新的多年期供应和合作协议,并于天科合达、天岳先进签订了供应协议,充分保障衬底供应。其他大厂通过自建或收购或合作等方式加快上下游整合,根据Evertiq的数据,近年来 SiC 行业内并购数量明显增加,以美国为例,2006-2022 年间共发生9 起SiC企业并购案件,其中 7 起发生于 2018 年及以后。
国内厂商不断跟进,相比海外大厂还有一定差距。目前,国产碳化硅二极管已经能够稳定交付,整体产业链也较为完善,国内厂商在二极管、MOS 单管已具备一定性价比优势。通过国产厂商的勤奋努力,碳化硅二极管成本不断下降,在工业、光伏储能等行业形成了广泛地国产替代。根据碳化硅芯观察调研,国内 SiC SBD 产品 2017 年的价格在4.1元/A左右,2020年下降到了 1.58 元/A,2023 年上半年国内厂家普遍报价在0.5-0.6 元/A。但在器件方面,仍与海外厂商有较大差距,器件技术水平要求最高的就是新能源汽车主驱逆变器,目前仅斯达半导、比亚迪半导体、芯聚能有碳化硅主驱功率模块成功上车,其他器件厂商上车的多为在OBC、DC/DC 上的应用及技术储备。
4.3. 国产化上主驱还要经历一段严苛漫长的历程
国产碳化硅模块上车需要经过多轮严苛的可靠性测试,最短需要26 个月时间。一般碳化硅模块上车要经过两个阶段,第一个阶段是产品在大量工业场景的验证打磨,工业场景的要求相对没有新能源车要求严苛,通过在大量工业场景,如充电桩、光伏逆变器等的大面积应用,通过小电流碳化硅 MOSFET 在工业化领域的规模化应用获得反馈不断打磨改进,而后进入新能源车的 OBC、DC/DC 等场景,积累大电流的碳化硅 MOSFET 的技术经验,有技术成熟的大功率碳化硅 MOSFET 模块产品后才进入第二个阶段的主驱逆变器的验证上车,这又需要经历拿到可靠性测试标准及多轮性能测试。目前备客户所认可的功率半导体器件可靠性测试标准有两种,即 AQG-324(针对模块)与 AEC-Q101(针对晶圆),分别代表着模块与单管两种器件的测试要求;根据泰科天润,性能测试要经历 3 轮性能测试,保守估计最短也需要26个月时间,且毫无「侥幸」通过的可能。
尽管国内企业在 SiC 器件领域起步较晚,但面对全球市场快速增长,叠加国内企业在新能源车、光伏逆变器等终端品牌市场份额的逐步提升,我国企业已经切入了SiC二极管或较高导通电阻的 MOS 产品,满足消费类产品、工业电源、车载充电机及小功率光伏组串式逆变器领域应用,之后逐步将产品迭代至低导通电阻 MOS,并补足模块封装实力,未来有望逐渐通过低端车到高端车定点或深度绑定车企或帮助车企代工等方式,逐渐成为新能源汽车主逆变器碳化硅功率器件的供应商。
5. 全产业链齐心协力推进低成本、高质量、大批量的产业化
碳化硅材料、工艺、应用突破难度高,国内产业链尚未形成完整的闭环,需要全产业链齐心协力推进低成本、高质量、大批量的产业化。上游材料层面产能不足、良率不足、产品缺陷多,又会影响到器件的可靠性和良率,这又会造成应用层面使用困难,应用层面没有足够的需求和数据能够为上游材料器件降本和技术工艺改进提供支撑。目前国内进展较快的在衬底和外延材料端,头部厂商已进入海外大厂的材料供应链,但良率、高质量导电型、大尺寸等方面与海外厂商仍有一定差距;下游晶圆、器件模块端相对进展较慢,国产厂商在工业领域已获得较大突破,而进入新能源汽车主逆变器仍有一段距离,这需要全产业链齐心协力来推进低成本、高质量且大批量的产业化,这离不开上游材料提高良率改进工艺,更离不开下游器件模块,也离不开设备厂的国产化降本。
碳化硅是产业趋势:我们认为碳化硅的产业趋势确定性不断加强,随着纯电渗透率的提升,高压快充技术逐渐成为中高端车的标配且向更低价格带延申,一方面碳化硅功率器件在高压快充等应用场景上本身具有更大耐高温、耐高压、耐高频的性能优势,同时碳化硅功率器件在消费者心中获得了一定的产品认知;另一方面随着各大厂商的加速扩产及提升技术水平,上游衬底和外延材料端成本不断下降,技术进步及规模效应带来的价格的下降才是刺激碳化硅市场渗透的核心要素。
落实到投资层面:结合产业进展, 1) 从估值方面,我们认为可以按照市销率进行估值。碳化硅产业是从0到1发展的行业,市场空间巨大,从拿到大批量客户订单开始,到确认营收,企业在这个过程中通过获得订单-迭代工艺-提高良率-提高盈利能力-获得订单的正循环反馈。2) 从各环节进展来看,我们认为各个环节的发展特征、目前水平、关注要点有所区别,核心关注产业趋势和企业订单情况。衬底及外延环节关注在下游放量及盈利能力的提升,现在头部衬底厂商已经进入了海外碳化硅大厂的材料供应链,说明国产衬底产品性能已经得到客户的认可,后续追踪订单情况,但落实到自身盈利上,还要更加关注工艺改善、良率提升;外延国内厂商集中度较高,但有诸多上下游企业切入后续关注竞争格局的变化及头部企业的规模优势;晶圆制造环节的核心关键在于高温离子注入机的保有量,高温离子注入机是限制晶圆制造产能的瓶颈;器件模块环节进入新能源车主逆变器供应的进展情况。
(本文仅供参考,不代表我们的任何投资建议。如需使用相关信息,请参阅报告原文。)
精选报告来源:【未来智库】。未来智库 - 官方网站