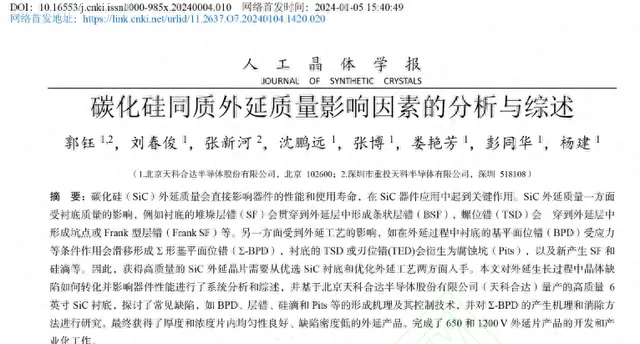
全文速览
目前常见的SiC外延技术有化学气相沉积(CVD)、液相外延生长(LPE)、分子束外延生长(MBE)等,当前,CVD是主流技术,具备较高生长速率、能够实现可控掺杂调控等优点。CVD外延生长通常使用硅烷和碳氢化合物作为反应气体,氢气作为载气,氯化氢作为辅助气体,或使用三氯氢硅(TCS)作为硅源代替硅烷和氯化氢,在约1600℃的温度条件下,反应气体分解并在SiC衬底表面外延生长SiC薄膜。2022年美国Wolfspeed公司已成功实现8英寸SiC外延产品的量产。市场上主流的量产产品主要是650、1200、1700V金氧半场效晶体管(MOSFET)器件用6英寸外延产品。
天科合达团队基于十多年在SiC底材料制备技术研究和产业推广经验的积累,2022年开始启动SiC外延技术研发,重点针对1200V车规级MOSEET器件用SiC外延材料进行研发和产业化工作。 近日,天科合达团队在【人工晶体学报】发表了题为【碳化硅同质外延质量影响因素的分析与综述】的综述论文。 文章对外延生长过程中晶体缺陷如何转化并影响器件性能进行了系统分析和综述,并基于北京天科合达半导体股份有限公司(天科合达)量产的高质量6英寸SiC衬底,探讨了常见缺陷,如BPD、层错、硅滴和Pits等的形成机理及其控制技术,并对Σ-BPD的产生机理和消除方法进行研究,最终获得了厚度和浓度片内均匀性良好、缺陷密度低的外延产品,完成了650和1200V外延片产品的开发和产业化工作。
图文导读
1. SiC外延层的掺杂浓度控制
本团队采用水平式外延生长方法,三氯氢硅和乙烯作为反应气源,氮气作为掺杂气体,氢气作为载气,氢气和气作为驱动托盘旋转的气源,生长厚度适用于1200V的SiC基MOSFET用SiC外延层。通过调整掺杂氮气在中心和边缘分布比例、托盘旋转的速度以及旋转气体中氯气与氢气的比例,优化外延工艺的C/Si比等生长参数,实现SiC外延层掺杂浓度以及均匀性的有效控制,图1是量产1000片的厚度和浓度均匀性统计数据,C/Si比在1.0~1.2、温度在1600~1650C和压力在100mbar的工艺条件下,统计的外延产品100%达到厚度均匀性小于3%、浓度均匀性小于6%。
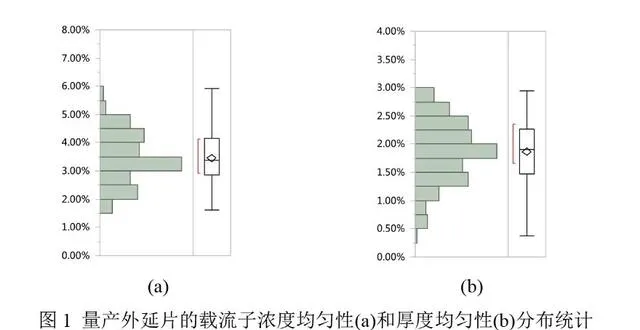
2. SiC 外延层的缺陷控制研究
根据晶体缺陷理论,SiC外延材料的主要缺陷可归纳为4大类:点缺陷、位错(属于线缺陷)、层错(属于面缺陷)和表面缺陷(属于体缺陷)。
2.1 点缺陷
SiC外延材料的点缺陷主要有硅空位、碳空位、硅碳双空位等缺陷,它们在禁带中产生深能级中心,影响材料的载流子寿命。在轻掺杂的SiC 外延层中,点缺陷产生的深能级中心浓度通常在5E12~2E13 cm-3,与外延生长条件特别是C/Si 比和生长温度相关。
2.2 位错缺陷
SiC 材料的位错包括螺位错(TSD)、刃位错(TED)和基平面位错(BPD)。微管是伯氏矢量较大的螺位错形成的中空管道,可认为是一种超螺位错。SiC 外延层的位错缺陷基本都和衬底相关,大部分微管和螺位错会复制到外延层中,在合适的工艺条件下,部分微管分解为单独的螺位错,形成微管闭合,只有一小部分TSD(通常<2%)转为Frank 型层错;衬底TED基本都会复制到外延层中。
BPD位错主要源于衬底中BPD向外延层的贯穿,通常偏4º 4H-SiC衬底中大部分BPD位错(>99%)在外延过程中会转化为TED位错,只有少于1%左右的BPD会贯穿到外延层中并达到外延层表面。在后续器件制造中,BPD主要影响双极型器件的稳定性,如出现双极型退化现象。在正向导通电流的作用下,BPD可能会延伸至外延层演变成堆垒层错(SF),造成器件正向导通电压漂移。由于刃位错对器件性能的影响要小得多,所以提高SiC外延生长过程中BPD转化为TED的比例,阻止衬底中的BPD向外延层中延伸对提高器件的性能十分重要。
在生长过程中,在应力等条件作用下,BPD很容易在衬底和外延层界面上沿着台阶流法线方向发生滑移,形成界面位错(interfacial dislocations,滑移方向取决于BPD的伯氏矢量及应力方向。特定条件下,成对BPD同时发生滑移,会形成Σ-BPD。在研发过程中也观察到过该缺陷,其典型形貌如图2所示,Photoluminescence 检测BPD形貌如图3(a),对外延片进行KOH腐蚀后形貌如图3(b)所示,可以看到一个Σ-BPD包含两条界面位错,其长度可以达到毫米级,在其尾部存在两个BPD。Σ-BPD形成机理示意图如图3(c)所示,其起源于衬底的BPD对,其伯氏矢量方向刚好相反,滑移过程中形成两条界面位错和2个半环位错(half-loop arrays,HLAs)。半环位错的长度不一,决定于其驱动力大小,影响滑移的驱动力主要是温场的不均匀性。
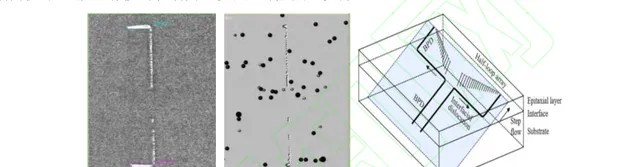
图2 Σ-BPD 形貌图(a)、氢氧化钾腐蚀坑图(b)和形成机理示意图(c)
针对外延BPD,研究团队在快速外延生长的基础上优化外延层缓冲层工艺窗口,目前可以实现BPD 密度小于0.1 cm-3 的外延层批量制备,如图3所示。
图3 外延片的BPD分布及其控制
2.3 层错缺陷
SiC外延层中的层错包括两大类,一类来源于衬底的层错和位错缺陷,衬底的层错会导致外延层形成Bar-shaped SFs,衬底的部分TSD会形成Frank SFs;另一类层错为生长层错(in-grown SFs),是外延生长过程中产生的,与衬底质量没有关系。目前,大多数外延层错属于第二类,这些层错中绝大部分为Shockley SFs,是通过在基平面中的滑移产生的。
降低外延生长速率、原位氢气刻蚀优化、增加生长温度、改善衬底质量都可以有效降低层错数量,天科合达已经可以提供Shockley SFs 密度小于0.15 cm-2的6英寸SiC衬底。
2.4 表面缺陷
SiC外延层表面缺陷尺度比较大,一般通过光学显微镜可以直接观察到,包括掉落物、三角形缺陷、「胡萝卜」缺陷、彗星缺陷、硅滴和浅坑。
表面缺陷与器件性能的影响目前也已经有了较多的研究报道,除浅坑缺陷外,其他表面缺陷基本都会对器件的性能产生一定的不利影响,导致器件击穿电压降低或者反向漏流增加。浅坑(Pits)是4H-SiC外延层表面出现在TSD位错顶端的小凹陷或小坑状的形貌缺陷,其宽度尺度小于10 μm。TED在外延层表面引起的小坑尺寸远小于TSD诱发的小坑尺寸,很难被观察到。图4是典型的浅坑AFM 形貌。
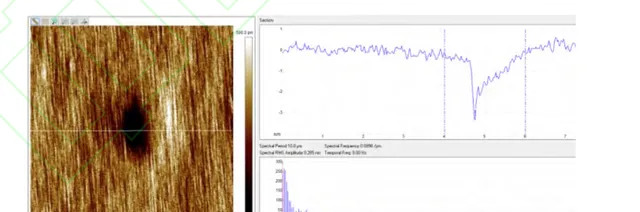
图4 外延表面宽度和深度分别为2和4 nm的浅坑的AFM形貌
Ohtani、Noboru等则利用TUNA技术研究了Pits和Large Pits的产生机理,认为宽度在几微米、深度在14 nm左右的Large pits是由TSD产生,而宽度在1 μm、深度在3-4 nm的Pits由TED产生。
降低Pits的主要途径包括:优选TSD数量较少的优质衬底、降低碳硅比和降低外延生长速率。目前市场上主要的商业化衬底中TSD的密度为小于1000/cm-3。本研究团队已经可以提供TSD密度小于300/cm-3的6英寸SiC衬底。通过采用优质衬底,调整外延工艺,可以将Pits数量从103降低到50以内。
综合来看,SiC外延层缺陷一方面取决于衬底结晶质量以及表面加工质量,另一方面受制于外延生长工艺窗口的优化,需要综合考虑各种缺陷的调整方案。基于研究团队量产的高质量6英寸SiC衬底,通过大量的实验研究,可以有效控制住SiC外延的各种缺陷,完成650V和1200V外延片产品开发和产业化工作。图5是典型的650V和1200V外延片产品缺陷mapping图,3mm×3mm良品率分别为98.9%和97.3%。
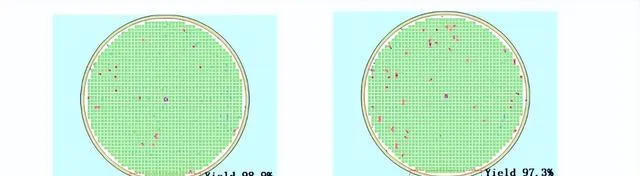
图5 650 V和1200 V外延片,3 mm×3 mm良品率分别为98.9%和97.3%
展 望
SiC外延在产业链中起着承上启下的重要作用,一方面通过不断积累对SiC材料的性能认知和改良,一方面通过器件的不断迭代验证,最终提升外延品质,推动SiC器件的应用。本文采用天科合达自有的商业化6英寸衬底,在4H SiC同质外延过程中,研究了外延层中BPD、层错、硅滴和Pits缺陷的控制,并对Σ-BPD的产生机理和消除进行研究, 最终获得厚度均匀性小于3%、浓度均匀性小于6%、表面粗糙度小于0.2m、良品率大于96%、BPD密度小于0.1cm的外延产品。 目前从本团队的研发进度来看,通过对工艺温度、C/Si比和长速等参数优化使得浓厚度分别控制在3%和2%以内,BPD的密度可以控制在0.075cm以内,但仍需要大量的外延数据进行工艺稳定性验证。
论文链接:https://link.cnki.net/urlid/11.2637.07.20240104.1420.020