化成工序作为锂离子电池生产的关键工序之一,对电池的电化学性能有着直接的影响。电池在进行首次充电时,电池内活性物质被激活,在负极表面形成固体电解质相界面(SEI)膜。采用不同的化成工艺参数,形成的SEI膜有所不同,会导致电池的电化学性能出现差异。
针对化成压力的研究,目前大都采用恒定压力进行化成,针对化成过程不同阶段改变压力的研究相对较少。本文作者在前人研究的基础上,采用变压力进行化成,化成初期,小电流时采用高压力,化成后期,大电流化成时降低化成压力,探究在化成过程中改变化成压力对电池的最终厚度、倍率和高温存储等性能的影响。
1 实验
1.1 电池制备
将正极活性材料LiCoO2、PVDF、导电浆料CNT按照 98∶1∶1的质量比混合匀浆,喷涂于10μm厚的铝箔上;将负极材料石墨、导电炭黑、羧甲基纤维素钠CMC和丁苯橡胶SBR按照97.5∶0.5∶0.9∶1.1的质量比混合匀浆,喷涂于6μm厚的铜箔上。以聚丙烯膜为隔膜,1mol/L LiPF6/ EC+DEC+EMC为电解液,经卷绕、装配、注液、化成和分容等工序,制备额定容量为3980mAh、截止电压为4.45V的软包装铝塑锂离子电池。分容步骤为:以 1.00C充电、0.20C放电循环2次。取第2次放电容量作为电池的容量,分容最小容量为3980mAh。化成实验方案如表1所示。
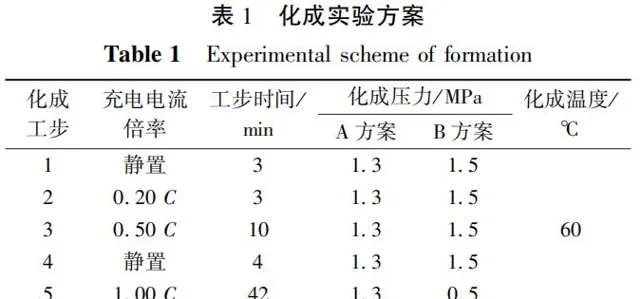
1.2 性能测试
采用数显平板测厚仪测量电池厚度;采用分容柜进行电池容量筛选;采用电池试验箱进行电芯的充放电、直流内阻及循环性能测试。
倍率性能测试:在25℃下,电池以1.00C充电至4.20V,再以0.70C充电至4.45V,转恒压充电至0.05C截止;分别以0.20C、0.50C、1.00C和1.50C放电至3.00V。
常温循环性能测试:在25℃下。电池以1.00C充电至4.45V。转恒压充电至0.05C截止;以1.00C恒流放电至3.0V,进行循环性能测试。
浮充测试:在45℃下,电池以0.80C充电至4. 45V,转恒压充电至0.05C,得到满电态电池。满电态电池以0.05C放电1h,静置10min,以0.50C充电至4.45V,转恒压充电至0.05C,在45℃下存储22.8h;重复以上流程,每7d采用数显平板测厚仪测量电池厚度,记录厚度变化率。
高温存储性能测试:将满电态电池在60℃恒温箱内,存储30d,测量厚度变化以及残余容量和恢复容量。在25℃下,以0.20C放电至3.00V,得到残余容量;以0.50C恒流充电至4.45V,转恒压充电至0.05C截止,然后以0.20C放电至3.00V,得到恢复容量。
2 结果与讨论
2.1 电池基本性能
两种化成方案电池的基本性能数据见表2。
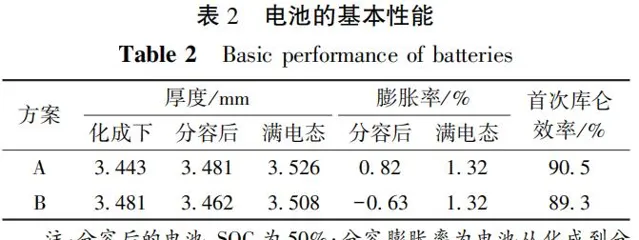
从表2可知,采用变压力化成的B方案,化成后电池的厚度较采用恒压力化成的A方案增加约40μm,但经过分容工序后,B方案电池厚度反而较A方案降低约20μm。这主要是由于B方案在化成大电流充电阶段降低了化成压力,使电池应力提前释放,厚度出现反弹,导致化成后厚度较大,而经过分容工序后,由于电池的SOC降低,厚度随之减小,因此,分容膨胀率为-0.63%。恒压力化成A方案,化成过程压力保持不变,电池厚度反弹出现在无外加压力的分容工序,因此,尽管分容后电池的SOC降至50%,但厚度反而比化成后70%SOC时的更大,分容膨胀率为0.82%。两种方案的满电态膨胀率均为1.32%,B方案的电池满电态厚度比A方案小约20μm。B方案电池的首次库仑效率较A方案低,可能是由于化成后期压力减小至0.5MPa,使得更多的电解液进入极片间参与成膜反应,导致消耗更多的活性锂,首次库仑效率略有降低。
2.2 直流内阻测试
不同 SOC 下,两种化成方案电池的直流内阻,见图 1。从图 1 可知,随着电池 SOC 从 10%增加到 100%,两种化成方案电池的直流内阻均出现先降低、后增加的趋势。同一SOC 下,两种方案的直流内阻差异较小,说明化成过程大电流下,降低化成压力对电池的直流内阻无明显影响。
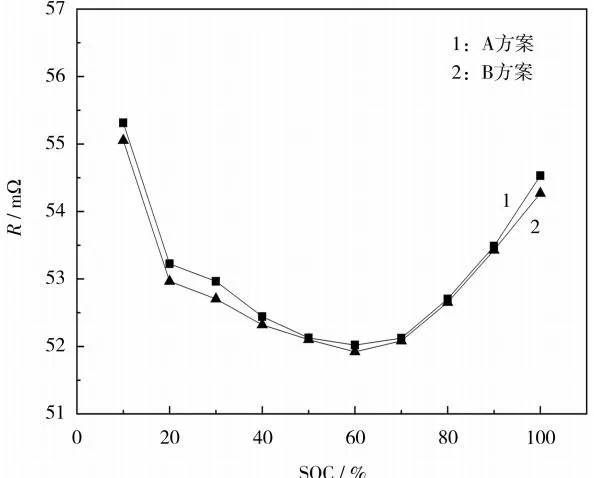
2.3 倍率放电性能
两种化成方案电池在0.20C、0.50C、1.00C、1.50C倍率下的放电性能见图2。从图2可知,在0.20C和0.50C的小倍率下,两种方案电池的倍率放电曲线基本重合。当放电倍率增加至1.50C时,B方案电池的倍率放电性能仅比A方案高0.36%,说明两种方案电池的倍率性能无明显差异。
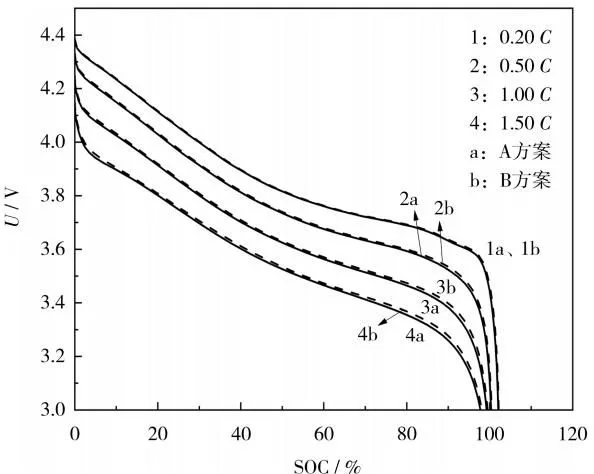
2.4 循环性能
两种化成方案电池的常温循环测试结果见图3。从图3可知,两种化成方案电池的常温循环容量保持率趋势整体一致,500次循环后,A方案和B方案的容量保持率分别为95.23%和95.95%,说明采用变压力化成对电池的循环稳定性无明显影响。B方案电池在循环过程中的厚度膨胀率仅较A方案小0.24%,变化趋势基本相同。
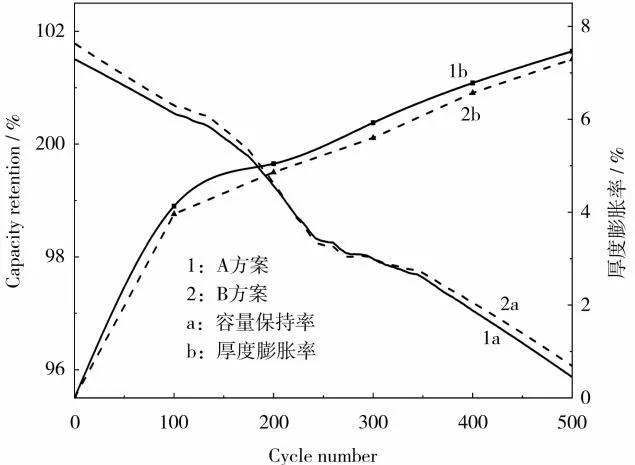
2.5 浮充测 试性能
电池在45℃下浮充测试的厚度膨胀率曲线见图4。从图4可知,在45℃条件下,经过84d浮充测试后,A方案与B方案电池的厚度膨胀率分别为6.28%和5.58%,说明化成大电流阶段减小化成压力,可降低电池在45℃浮充测试时的厚度膨胀率。
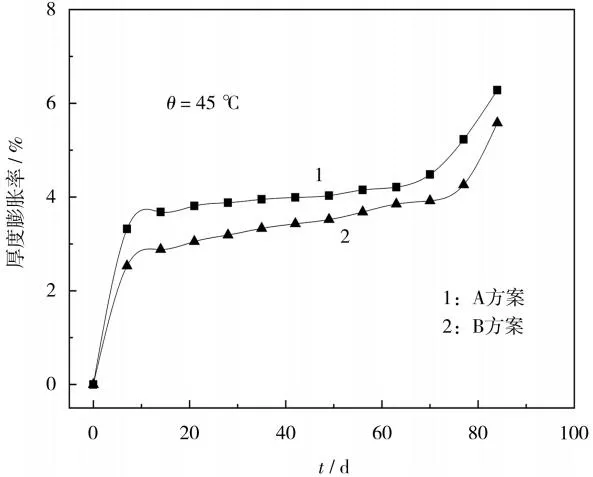
2.6 高温存储性能
两种化成方案电池在60℃下高温存储30d的厚度膨胀率曲线见图5。从图5可知,在60℃高温存储30d,A方案电池的厚度膨胀率为2.83%,而B方案电池的厚度膨胀率为1.82%,厚度膨胀率减小1.01%。这说明,电池在化成过程60℃条件下释放应力,厚度发生反弹,可以降低在高温存储时的厚度膨胀率。对于采用铝塑封装的软包装电池,由于铝塑外壳的机械强度相对较小,对电芯束缚性弱,会降低在高温环境下的膨胀率,能够提高在高温下使用的安全性。
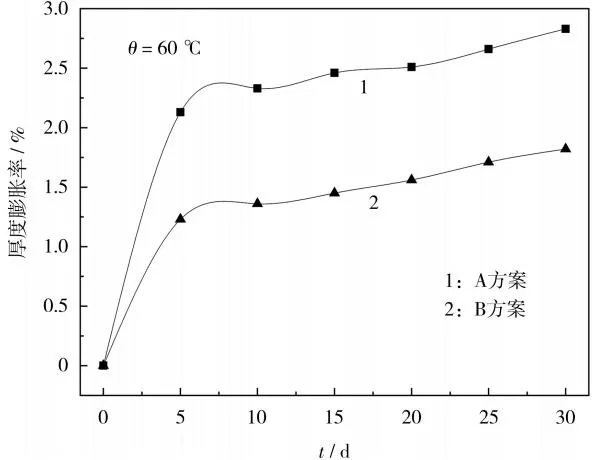
电池在60℃高温存储30d后的残余容量与恢复容量数据见表3。从表3可知,A方案电池的初始容量较B方案高12mAh,原因是A方案电池的首次库仑效率高于B方案。B方案电池的残余容量和恢复容量均高于A方案,说明化成过程大电流时降低压力使SEI膜的稳定性有所提高,在高温存储时,SEI膜的分解重组消耗的锂更少,降低了容量损失。
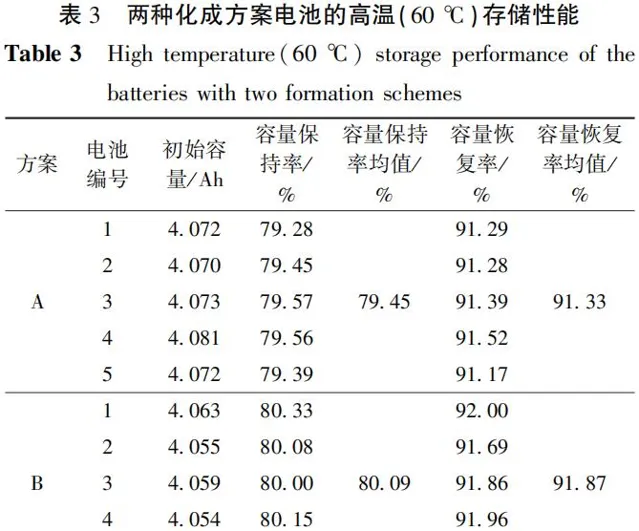
3 结论
目前,在软包装锂离子电池化成过程中均采用恒定压力进行化成,分容后电池厚度出现膨胀,导致电池厚度增加;而在化成大电流阶段将化成压力减小为小电流时的1/3,电池在化成阶段释放应力,可降低电池的最终厚度。与恒压力化成相比,采用变压力化成使得电池在浮充及高温存储时的厚度膨胀率分别降低0.70%和1.01%,提高了电池在高温下使用的安全性。