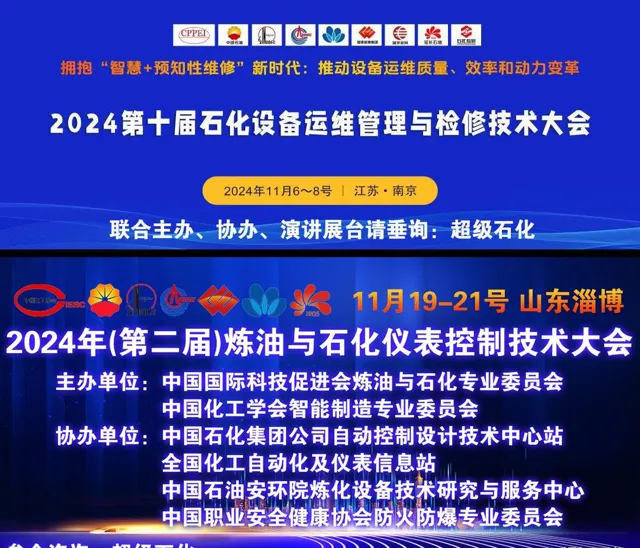
超级石化: 为了有效弥补探针监测、挂片监测和离线测厚监测等传统腐蚀监测技术的局限性,某石化公司在腐蚀程度较为严重的装置引入了在线超声测厚腐蚀监测技术,该技术具有适用于高温管道测厚、安装灵活方便、节约成本等优点。现场应用结果表明:在线超声测厚技术运行稳定可靠、数据准确,与离线测厚数据的比对误差不大于6%。该技术能够准确监测管道的剩余壁厚,真实反映其腐蚀变化趋势,并能及时发现腐蚀隐患,预防腐蚀事件的发生,未来将会成为炼化装置腐蚀监测领域广泛应用的一项新技术。
关键词: 在线测厚 腐蚀监测 石油化工装置 管道
某石化公司加工原油主要以哈萨克斯坦管输原油为主,该原油硫含量高、酸值低,属于典型的高硫低酸原油 【1】 。近年来随着原油性质的劣化,原油硫含量呈明显上升趋势,导致常减压装置高温部位和低温部位的硫腐蚀问题突显,例如「三顶」部位、转油线、常压塔和减压塔的侧线及塔底等部位的部分设备及管道出现不同程度的腐蚀损伤,继而对二次炼油装置及乙烯装置部分易腐蚀部位的设备及管道也造成了较为严重的腐蚀损伤。为了掌握关键炼化装置的腐蚀变化趋势,及时发现腐蚀隐患,并采取防护措施予以抑制,该石化公司在炼化装置采用了以挂片监测、在线腐蚀探针监测和离线测厚监测为主的传统腐蚀监测技术,为装置管理人员提供了及时、准确的监测数据,进而为装置开展腐蚀评价、采取防护措施提供了数据支持,有力地保障了装置的安全、长周期运行。然而在应用过程中,发现这些腐蚀监测技术由于自身的缺点,在使用过程中均存在一定的局限性 【2-8】 。例如,挂片监测时间长、数据滞后,拆装危险且麻烦;在线腐蚀探针监测安装时需在管道上开孔,不宜用于高温、高压及高危部位,且后期探针更换安全风险较高;人工离线测厚工作量大、成本高,由于需要耦合剂,高温部位测厚数据准确性较差,高空、高危险等人不能到达的部位不易监测。
鉴于上述传统腐蚀监测技术在炼化装置应用过程中的局限性,某石化公司对国内外石化企业应用效果较好的腐蚀监测技术进行了调研,发现BP、壳牌等公司开始使用的在线测厚腐蚀监测技术是一种适用性强、效果较好的腐蚀监测技术,其有效弥补了传统腐蚀监测技术的局限性,将成为各炼化企业未来广泛采用的一种新技术 【9-10】 。根据调研结果,某石化公司在常减压蒸馏装置、蜡油加氢装置等腐蚀程度较为严重的3套炼油装置引入了在线测厚腐蚀监测技术。
1 在线测厚技术系统组成及特点
1.1 系统组成及功能
在线测厚系统由探头、无线网关、中心服务器三部分组成,其组成及运行如图1所示。探头通过卡箍或螺柱方式固定在管道的监测部位,每个探头通过无线通讯方式将在线监测数据汇总至网关;网关通过局域网将在线监测数据传至中心服务器,局域网内的终端电脑通过访问中心服务器即可实现对在线测厚数据的浏览和腐蚀评价。
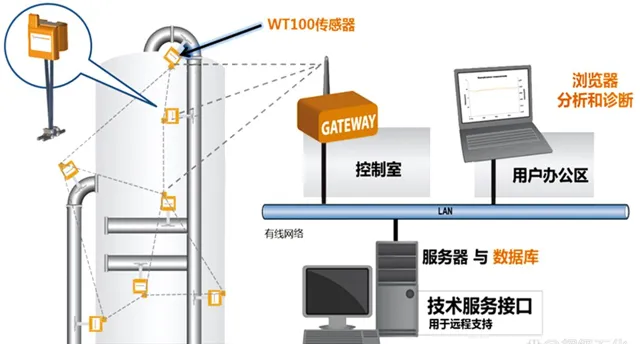
图1 在线测厚腐蚀监测系统运行
探头的主要功能为监测点壁厚测量、数据采集及无线传输,主要由传感器及波导杆组成,其中传感器包括电池、超声波测量及采集模块和无线通讯模块三部分,波导杆由两根特殊材料制成的钢片组成。传感器发出的超声波通过其中一根波导杆传递到管道金属表面,而后返回的超声波再由另一根波导杆传回到传感器。在波导杆的末端有固定螺口,通过卡箍上的螺栓就可以将探头固定在管道的监测点上,波导杆被压紧在管道金属表面上,其现场安装如图2所示。
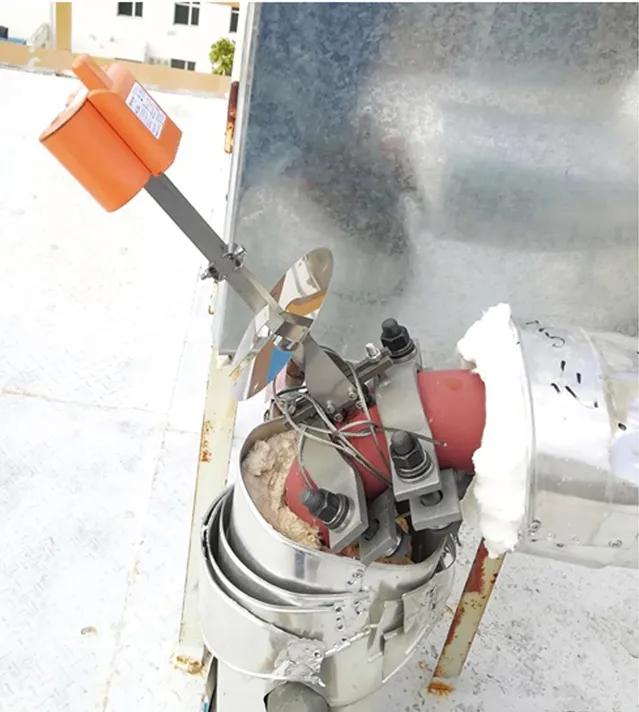
图2 探头现场安装
无线网关的主要功能为接收所有监测点探头的无线传输数据,通过电缆连接至仪表间机柜网络接口,并将数据通过有线通讯方式传输至中心服务器。无线网关采用防爆型网关设计,传输方式采用IEEE802.15.4标准协议,操作频率为2.4 GHz全球免许可证频段,网关与探头及各探头之间的距离不超过50 m,中继探头不超过7个,最远探头与网关距离不超过400 m。
中心服务器的主要功能为接收、存储、备份网关上传的数据,管理腐蚀监测数据库,向浏览站点发布腐蚀监测数据。中心服务器上安装有网关管理器、数据库软件和基于Web浏览器的数据浏览软件,其采用双硬盘冗余热备份,保障数据存储安全。为了后期维护安全,中心服务器使用了公司内部的虚拟服务器。
1.2 技术特点
1.2.1 更适用于高温部位
人工离线测厚技术采用压电超声波测厚方法,探头与管道金属表面间需使用耦合剂,在高温管道测厚过程中,一方面耦合剂极易气化、结焦,测厚数据波动较大,甚至无法测厚,另一方面探头受热极易损坏(探头与管道表面的接触时间若超过5 s,探头就会烧坏)。而在线测厚技术采用电磁超声波测厚方法,探头的波导杆前段通过卡箍与被测管道金属表面硬耦合,无需使用耦合剂,因而避免了高温测厚过程中耦合剂气化、结焦导致测厚数据波动较大或无法测厚的问题,该技术更适用于较高温度管道的定点测厚,最高测厚温度达600 ℃。在线测厚使用波导杆与高温金属管道接触,因而使探头上的传感器与高温金属管道相隔离,有效减缓了传感器受热损坏的风险,这也是其能用于高温测厚的一个重要原因。
1.2.2 更适用于高危部位
在线测厚探头使用卡箍方式安装于管道上,无需开孔、焊接等施工措施,不损伤管道的本体,即使在管道运行过程中也可安装或拆卸。这一特点使在线测厚系统更适宜于装置的高温、高压、高空等高危部位的腐蚀监测,例如减压塔的高温侧线部位、加氢裂化装置反应流出系统的高温高压管道部位、空冷管线的高空部位等,相比传统的探针监测和旁路釜监测,这是一个无法替代的优势 【11】 。因为探针监测需要将探针插入管道内部,若安装在高温、高压等高危部位,探针拆装更换的风险极大,一旦其腐蚀损耗完就只有在装置停工时才能拆装更换,探针即处于失效状态。同样,挂片监测需要在管道上设置旁路或开孔插入管道,因而拆装也十分困难,每半年甚至一个停工周期才可采集一次数据。而在线测厚监测系统的探头可随时进行安装与拆卸,而且可以实时采集并传输数据。
2 在线测厚腐蚀监测技术的应用
2.1 评选腐蚀监测部位
进行炼化装置的在线测厚腐蚀监测,首先要评选出装置的腐蚀监测部位,只有将在线测厚设备安装在正确的腐蚀监测部位,所获得的腐蚀监测数据才能准确、可靠地反映出该部位的实际腐蚀情况,这样的监测才是有效监测。以某石化公司200万t/a蜡油加氢装置为例,综合考虑各方面影响因素对装置的腐蚀监测部位进行评选,结果如表1所示。分析表1可知,腐蚀监测部位均为管道的弯头、三通、直管低点部位及设备进出口。
表1 200万t/a蜡油加氢装置腐蚀监测部位
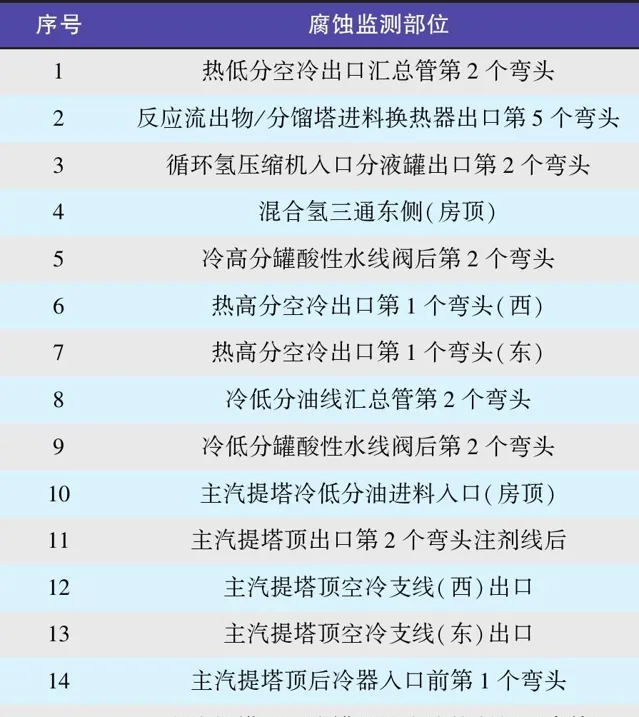
2.2 确定在线测厚点
评选出装置的腐蚀监测部位后,紧接着需要在腐蚀监测部位确定在线测厚点(即探头安装的具体位置)。在线测厚点的确定是整个在线测厚设备安装的重中之重。在线测厚点首先要能反映在线测厚部位设备及管道的腐蚀发展趋势,其次要代表在线测厚部位腐蚀最严重的那一点,如此,才可准确发现早期的腐蚀泄漏点并预防腐蚀泄漏事件的发生,因此,在线测厚点应选择在管道剩余壁厚值最小的那一点。
为了科学、准确地确定200万t/a蜡油加氢装置15处在线测厚点的位置,引入瞬磁涡流检测技术和超声波测厚技术进行精确定位,同时结合管道弯头腐蚀减薄的经验部位及计算流体动力学(Computational Fluid Dynamics,CFD)技术模拟结果,提出了在线测厚点的评选方法,具体如下:
1)首先根据常规的离线测厚经验及文献中的CFD技术模拟结果,弯头部位壁厚最薄点(即腐蚀减薄最严重的点)一般出现在弯头的背弯部位。
2)对于弯头、三通、直管采用瞬磁涡流检测技术先进行面扫查,即对于弯头沿轴向进行正背弯、正背弯两侧共三次面扫查,可确定轴向方向上厚度最薄的一块区域,而后再以该区域为中心进行环向扫查,最后确定厚度集中较薄的区域;对于三通和直管则沿管道轴向对其上、下、前、后四个面进行四次面扫查,可确定轴向方向上厚度最薄的一块区域,而后再以该区域为中心进行环向扫查,最后确定厚度集中最薄的区域。
3)针对瞬磁涡流检测确定的管道轴向最薄的区域(其大小约为5 cm×8 cm),采用离线超声波测厚技术进行密集测厚,最终确定出管道壁厚值最小的点,该点即为在线测厚点。
2.3 在线测厚系统的安装
完成上述工作,即可开展在线测厚系统的现场安装,其步骤与具体工作内容如下:
第一步,拆除保温,确定在线测厚点,现场安装卡箍,并将探头固定在卡箍上,保证探头的波导杆前端压紧在金属管道的在线测厚点上;
第二步,在15处在线测厚点的中心位置安装网关并布置仪表线,并在仪表柜间安装数据转换器;
第三步,在网关中加载各在线测厚探头,并进行现场调试;
第四步,在局域网中心服务器上安装在线测厚软件及相关插件,同时,在授权的局域网办公电脑上进行现场15处在线测厚点的数据加载,并调试在线测厚系统的整体运行情况;
第五步,完成上述工作,申请开通局域网内在线测厚系统的数据浏览权限,局域网内终端用户可浏览在线测厚数据,在线测厚系统正式上线运行。
2.4 测厚数据准确性评价
在线测厚系统上线运行后,对在线测厚数据的准确性进行了评价,即对在线测厚数值 Z 与离线测厚数值 L 进行比对,并计算两者的误差值 W 。 W 的计算方法如式(1)所示,结果如表2所示。
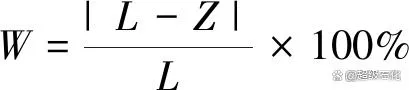
(1)
式中: W ——在线测厚数据的误差,%;
Z ——在线测厚数值,mm;
L ——离线测厚数值,mm。
由表2数据可知,15处在线测厚点的在线测厚数据与离线测厚数据相差较小,在线测厚数据的最大误差值为6.0%,73%的在线测厚数据误差值≤2.5%,由此可见,在线测厚数据还是较为准确的。
表2 200万t/a蜡油加氢装置在线测厚数据误差计算
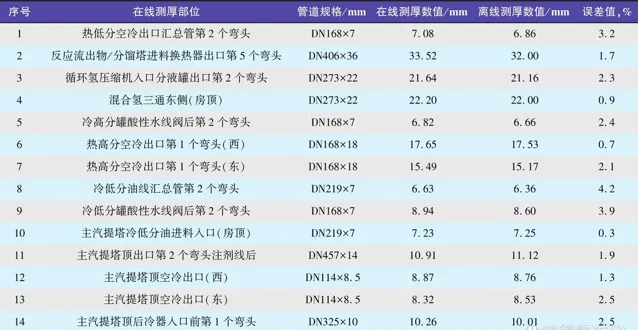
2.5 现场应用
1)实时掌握装置腐蚀变化趋势,为装置及时采取防腐蚀措施提供数据支持。
图3为某石化公司1 000万t/a常减压装置常三线的在线测厚腐蚀监测图谱。由图3可知,从2019年11月1日~2020年2月30日常三线的剩余壁厚值呈平缓的下降趋势,建立数据拟合线,测出这一监测期间的管线腐蚀速率为0.21 mm/a,腐蚀速率偏高,车间根据在线测厚腐蚀监测数据持续关注腐蚀变化趋势。装置自3月份开始加工含氯原油,该原油硫含量最高值达1.7%、平均值1.2%,较哈油硫含量明显上升,导致原油腐蚀性增强。同时,从在线测厚腐蚀监测数据来看,3月份(3月1日~3月30日)常三线的剩余壁厚值呈明显下降趋势,腐蚀速率高达0.78 mm/a,反映出装置加工高氯原油以后常三线的腐蚀较为严重的情况,这与装置的实际腐蚀情况相一致。因为高氯原油的硫含量较高,导致蒸馏装置常压塔测线硫含量上升,常三线高温硫腐蚀加剧。由此可见,常三线在线测厚腐蚀监测为装置及时采取防护措施、消除腐蚀隐患提供了可靠、准确的技术及数据支持。
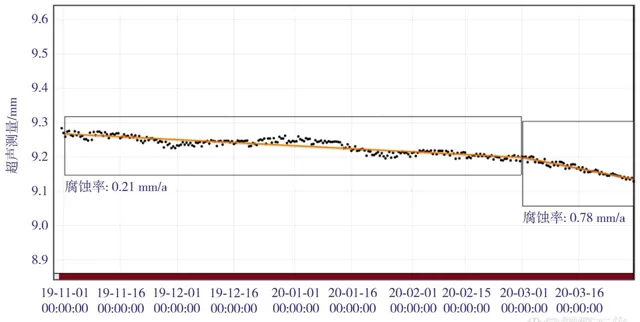
图3 常减压装置常三线在线测厚腐蚀监测图谱
2)及时发现腐蚀隐患,预防腐蚀事件发生。
图4是某石化公司常减压装置1.0 MPa凝结水线弯头部位的在线测厚数据,探头采用卡箍方式安装在管道弯头的背弯部位。由图4可见,该监测部位从2018年1月23日开始管道壁厚呈明显的下降趋势,至2018年3月1日,监测部位管道壁厚值由5.49 mm减薄至5.43 mm,其平均腐蚀速率高达0.61 mm/a,表明1.0 MPa凝结水线弯头部位管道腐蚀减薄严重。为了确保每个在线测厚数据的准确性,取关键测厚数据(位于拐点或折点的数据)的超声波图谱进行分析验证,结果显示,关键测厚数据一次波形与二次波形清晰完整,数据真实可靠。
图4 常减压装置1.0 MPa凝结水线在线测厚腐蚀监测图谱
冷油泵房顶1.0 MPa凝结水线弯头部位的腐蚀类型为冲刷腐蚀,且2018年3月1日后在线测厚数据发展趋势一直呈明显下降趋势,表明在凝结水的不断冲刷腐蚀作用下,弯头背弯部位壁厚不断减薄。为防止管道发生腐蚀泄漏,重点关注在线测厚腐蚀监测数据的变化趋势,以便采取应急防护措施。待到装置停工检修时,立即对该弯头进行了更换。检查更换下来的弯头发现,弯头背弯部位内壁冲刷腐蚀严重,局部几乎穿孔。应用效果表明,在线测厚腐蚀监测技术成功消减了1.0 MPa凝结水线弯头部位的腐蚀隐患,避免了弯头因冲刷腐蚀而导致的泄漏事件。
3)应用推广
在线测厚腐蚀监测技术主要用于监测设备及管道的剩余壁厚,其技术优势突出,适用性强,现场安装方便,非常适用于公司易腐蚀炼化装置的腐蚀监测。目前,在线测厚腐蚀监测技术已在100万t/a常减压装置、100万t/a蜡油加氢装置、200万t/a蜡油加氢装置中成功应用,可实时掌握装置腐蚀变化趋势,为装置及时采取防腐蚀措施提供数据支持,而且还可以及时发现腐蚀隐患,预防腐蚀事件发生。基于在线测厚腐蚀监测技术的适用性及应用效果,该技术可在其他15套装置的易腐蚀部位进行推广应用,如表3所示。
表3 在线测厚腐蚀监测技术推广应用装置
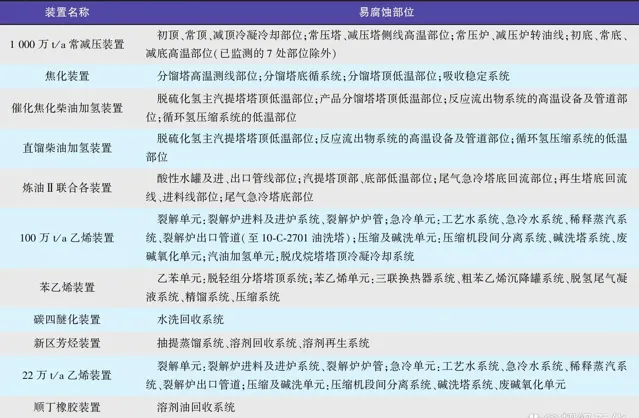
3 结语
在线超声测厚腐蚀监测技术具有适用于高温定点测厚、高危部位测厚、卡箍式安装(无需开孔)等胜于传统腐蚀监测技术的优点,该系统运行稳定,应用效果良好,能够准确监测设备及管道的剩余壁厚,真实反映监测部位的腐蚀变化趋势。装置现场应用效果表明,在线测厚腐蚀监测技术为从事腐蚀管理人员采取防腐蚀措施、及时发现腐蚀隐患、预防腐蚀事件发生提供了有力的技术及数据支持,而且可向其他炼化装置推广应用,预计其将会成为炼化企业未来几年广泛应用的腐蚀监检测技术。
「 2024 第十届石化设备运维管理与检修技术大会( 11 月 6-8 南京)」,「 2024 年 ( 第二届 ) 炼油与石化仪表控制技术大会( 11 月 19-21 山东淄博)」, 欢迎优秀技术装备服务商、检维修公司、仪器仪表自动化企业、智能化数字化服务商参加演讲和展示交流,增进合作,共创双赢局面!详情请联系:超级石化