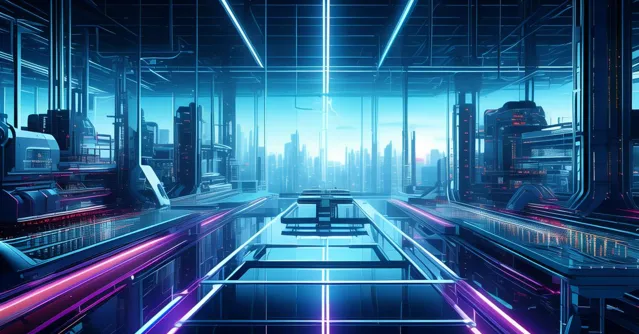
一台僅3.6公斤,60cm長的裝置,透過優秀的人體工學設計,實作舒適的使用體驗,透過簡單的在室內行走,就能形成打造數位孿生工廠的「初始數據」——距離「數位孿生」概念自2012年NASA提出已經過去十余年,如今實作三維數據采集的手段已經愈發先進,也正走出「樣板展示」的局限。
從傳統工廠到數位工廠
數位孿生是充分利用物理模型、傳感器、執行歷史等數據,整合多學科、多物理量、多尺度、多機率的仿真過程,在虛擬空間中完成對映,從而反映相對應的實體裝備的全生命周期過程。數位孿生是一種超越現實的概念,可以被視為一個或多個重要的、彼此依賴的裝備系統的數位對映系統。
硬體裝置和軟體技術共同影響著數位孿生技術的發展,尤其是在傳統制造業側,在NavVis CRO Finn Boysen看來,利用數位孿生技術,在工廠的廠房和產線沒有建造之前,就完成數位化模型。從而在虛擬的賽博空間中對工廠進行仿真和模擬,並將真實參數傳給實際的工廠建設,在國際上已經成為制造業企業建設工廠過程中,不可或缺的一個步驟。
傳統制造業工廠,透過數位孿生技術可以實作數位化轉型,同時實作降本增效的目的,但在利用數位孿生建設數位工廠的過程中,企業面臨著諸多問題。
首先,如何能夠高效率的采集和輸出高品質的三維空間數據,即如何高效的將物理世界數位化,同時數位化之後的數據品質和精度能滿足業務套用需求。
「因為所有的數位孿生,都是從將物理世界數位化開始的,即打造一個數位底座。如果這一過程所需的時間太長,或者雖然時間短但獲取的數據品質不高,對於後期進行數位孿生建設會有很大的影響。」NavVis大中華區執行總裁李自明告訴鈦媒體APP,「這也是為什麽目前的數位孿生大多是作為樣板展示,真正在業務實踐中套用的並不常見。」
其次,如何更便捷、有效的存取和管理三維空間數據也是企業在建設數位孿生工廠過程中面臨的一大挑戰。
三維空間數據量極大,需要消耗大量的算力進行處理和管理,在這個過程中,顯然雲端運算是最好的解決方案,「為了能夠讓更多的使用者可以存取和使用這些數據,最佳方案是實作基於瀏覽器的輕量化存取,這樣只要客戶會使用瀏覽器,就可以存取和管理數據,而不需要安裝和學習專用軟體知識。」李自明進一步指出。
三維移動掃描技術是底層支撐
三維移動掃描技術的出現,能夠很好的解決上述痛點,讓數位工廠建設變成了可能。回看掃描行業,由最早的數位化全站儀掃描,到傳統架站式雷射掃描器,這些儀器一方面自身占地面積較大,在寬闊的室外空間尚有發揮余地,但在相對狹窄的室內空間,就顯得捉襟見肘;另一方面,現有的小型手持掃描器器在數據精度方面也有很大的提升空間,數位工廠建設,室內掃描過程中對於數據精度的要求極高,現有的小型手持掃描器器顯然不能滿足發展需求。
移動雷射掃描在逐步取代傳統的架站式掃描TLS,以前TLS是使用者進行計畫作業的主要工具,「未來移動雷射掃描裝置將會成為主要工具,我們預計95%以上的套用場景均可采用激動雷射掃描。」李自明告訴鈦媒體APP。
得益於雷射雷達產品技術的發展,三維掃描的產品尺寸越來越小,重量越來越輕,這就讓這些產品可以在更為狹小的空間內使用,同時還能提供更為精準的數據。不僅於此,隨著技術的發展,產品的平均價格也會越來越低,因此會有更多的使用者可以有機會使用這些先進的技術。
與此同時,因為三維空間數據是海量數據,需要巨大的算力進行處理,人工智慧AI技術和雲端運算技術會被越來越廣泛的套用,在李自明看來,透過AI和雲端運算,未來可以做到對三維空間數據進行自動辨識和分類等先進的功能。
而隨著技術的發展,未來對於三維數據的存取也將變得更容易,「未來三維空間數據的存取和使用將會更加輕量化,不再需要專業知識和軟體,」李自明指出,「例如NavVis IVION三維空間數據管理平台,是基於瀏覽器模式,透過瀏覽器就可以輕鬆存取和管理海量的三維空間數據。」
基於此,NavVis提出了全新的手持移動雷射掃描系統設計理念,並且因為小巧的體積,可以在更為狹小的空間開展作業,同時更方便工作人員攜帶。
在數據精度方面,NavVis MLX是一款可以達到公釐級數據精度的手持移動掃描裝置。同時,透過軟體演算法,實作在僅有一台雷射雷達傳感器的條件下能達到5mm的數據精度。
同時還套用了點雲技術,透過點雲來還原現場圖片,對270°的圖片進行反向填充,實作360度全景圖片。
數位孿生,讓建築降本、降碳
以一個70平方米的室內空間為例,傳統的架站式雷射掃描器需要架設10~11個掃描點,消耗30分鐘時間,且還存在很多沒有掃描到的盲點;
透過三維移動掃描技術,同樣的空間條件下,僅需5分鐘就能完成掃描,且沒有掃描盲點,數據精度更高。
在寶馬的套用案例中,透過數位孿生技術,寶馬的制造工廠實作了再在虛擬環境會議中解決臨時任務,在點雲模型的基礎上,重新建立3D圖紙,進行建模,透過數位孿生工廠進行廠區分析,以及工廠長期規劃,在車間內進行虛擬測量和標記,透過虛擬化環境實作遠端支持,以及生產中斷或維護方案的數位化準備工作等目標。
據了解,目前寶馬工廠已有超過900萬平方米的廠區透過數位孿生技術,上線了虛擬化工廠,公司內部超過25000名公司員工註冊了數位孿生平台帳號。
透過全球工廠遠端存取技術,減少了50%的差旅費用,提高了20%規劃效率,並透過可信的、與現實一直的數據文件,降低了工廠變更成本5%~10%。 (本文先發於鈦媒體APP,作者|張申宇,編輯丨蓋虹達)
「關於創新場景50」
場景不是案例,它更加精準、也更加抽象。數位化就是創新場景的不斷疊加和叠代。
在此背景下,鈦媒體重磅推出「創新場景50」評選,每年遴選並解讀50個全行業與業務深度融合的創新性場景及其解決方案,並在鈦媒體年度ITValue Summit 數位價值年會上隆重頒獎、深度交流。
目前場景正在征集中,更精準的解讀、更廣泛的曝光、更強大的品牌勢能,歡迎你提出問題,更歡迎你留下解決的方法和工具。點選這裏投遞更多場景資訊