化成工序作為鋰離子電池生產的關鍵工序之一,對電池的電化學效能有著直接的影響。電池在進行首次充電時,電池內活性物質被啟用,在負極表面形成固體電解質相界面(SEI)膜。采用不同的化成工藝參數,形成的SEI膜有所不同,會導致電池的電化學效能出現差異。
針對化成壓力的研究,目前大都采用恒定壓力進行化成,針對化成過程不同階段改變壓力的研究相對較少。本文作者在前人研究的基礎上,采用變壓力進行化成,化成初期,小電流時采用高壓力,化成後期,大電流化成時降低化成壓力,探究在化成過程中改變化成壓力對電池的最終厚度、倍率和高溫儲存等效能的影響。
1 實驗
1.1 電池制備
將正極活性材料LiCoO2、PVDF、導電漿料CNT按照 98∶1∶1的品質比混合勻漿,噴塗於10μm厚的鋁箔上;將負極材料石墨、導電黑碳、羧甲基纖維素鈉CMC和丁苯橡膠SBR按照97.5∶0.5∶0.9∶1.1的品質比混合勻漿,噴塗於6μm厚的銅箔上。以聚丙烯膜為隔膜,1mol/L LiPF6/ EC+DEC+EMC為電解液,經卷繞、裝配、註液、化成和分容等工序,制備額定容量為3980mAh、截止電壓為4.45V的軟包裝鋁塑鋰離子電池。分容步驟為:以 1.00C充電、0.20C放電迴圈2次。取第2次放電容量作為電池的容量,分容最小容量為3980mAh。化成實驗方案如表1所示。
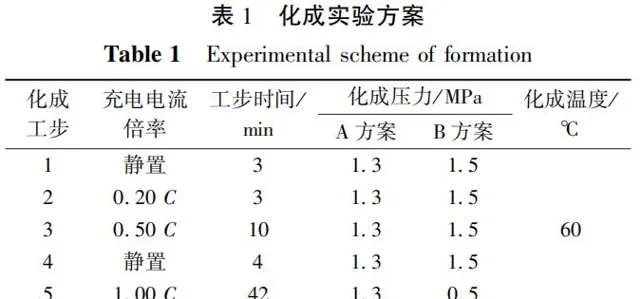
1.2 效能測試
采用數顯平板測厚儀測量電池厚度;采用分容櫃進行電池容量篩選;采用電池試驗箱進行電芯的充放電、直流內阻及迴圈效能測試。
倍率效能測試:在25℃下,電池以1.00C充電至4.20V,再以0.70C充電至4.45V,轉恒壓充電至0.05C截止;分別以0.20C、0.50C、1.00C和1.50C放電至3.00V。
常溫迴圈效能測試:在25℃下。電池以1.00C充電至4.45V。轉恒壓充電至0.05C截止;以1.00C恒流放電至3.0V,進行迴圈效能測試。
浮充測試:在45℃下,電池以0.80C充電至4. 45V,轉恒壓充電至0.05C,得到滿電態電池。滿電態電池以0.05C放電1h,靜置10min,以0.50C充電至4.45V,轉恒壓充電至0.05C,在45℃下儲存22.8h;重復以上流程,每7d采用數顯平板測厚儀測量電池厚度,記錄厚度變化率。
高溫儲存效能測試:將滿電態電池在60℃恒溫箱內,儲存30d,測量厚度變化以及殘余容量和恢復容量。在25℃下,以0.20C放電至3.00V,得到殘余容量;以0.50C恒流充電至4.45V,轉恒壓充電至0.05C截止,然後以0.20C放電至3.00V,得到恢復容量。
2 結果與討論
2.1 電池基本效能
兩種化成方案電池的基本效能數據見表2。
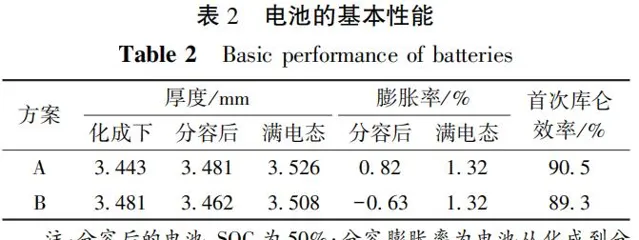
從表2可知,采用變壓力化成的B方案,化成後電池的厚度較采用恒壓力化成的A方案增加約40μm,但經過分容工序後,B方案電池厚度反而較A方案降低約20μm。這主要是由於B方案在化成大電流充電階段降低了化成壓力,使電池應力提前釋放,厚度出現反彈,導致化成後厚度較大,而經過分容工序後,由於電池的SOC降低,厚度隨之減小,因此,分容膨脹率為-0.63%。恒壓力化成A方案,化成過程壓力保持不變,電池厚度反彈出現在無外加壓力的分容工序,因此,盡管分容後電池的SOC降至50%,但厚度反而比化成後70%SOC時的更大,分容膨脹率為0.82%。兩種方案的滿電態膨脹率均為1.32%,B方案的電池滿電態厚度比A方案小約20μm。B方案電池的首次庫侖效率較A方案低,可能是由於化成後期壓力減小至0.5MPa,使得更多的電解液進入極片間參與成膜反應,導致消耗更多的活性鋰,首次庫侖效率略有降低。
2.2 直流內阻測試
不同 SOC 下,兩種化成方案電池的直流內阻,見圖 1。從圖 1 可知,隨著電池 SOC 從 10%增加到 100%,兩種化成方案電池的直流內阻均出現先降低、後增加的趨勢。同一SOC 下,兩種方案的直流內阻差異較小,說明化成過程大電流下,降低化成壓力對電池的直流內阻無明顯影響。
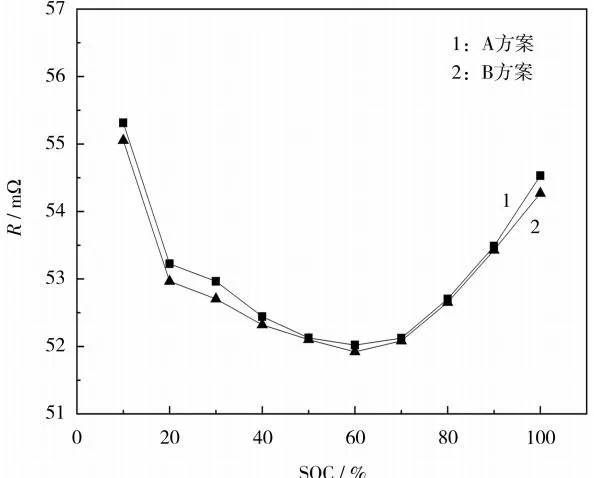
2.3 倍率放電效能
兩種化成方案電池在0.20C、0.50C、1.00C、1.50C倍率下的放電效能見圖2。從圖2可知,在0.20C和0.50C的小倍率下,兩種方案電池的倍率放電曲線基本重合。當放電倍率增加至1.50C時,B方案電池的倍率放電效能僅比A方案高0.36%,說明兩種方案電池的倍率效能無明顯差異。
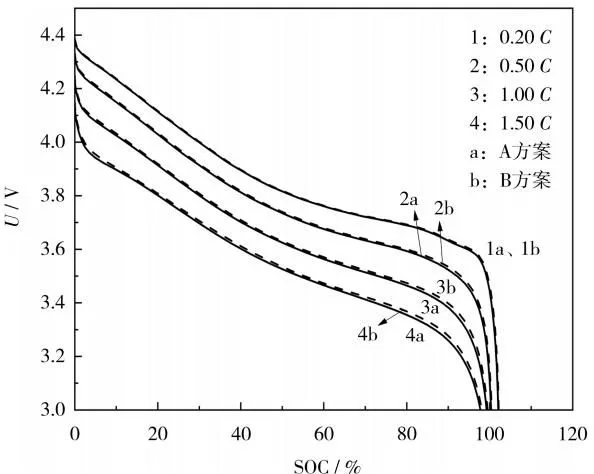
2.4 迴圈效能
兩種化成方案電池的常溫迴圈測試結果見圖3。從圖3可知,兩種化成方案電池的常溫迴圈容量保持率趨勢整體一致,500次迴圈後,A方案和B方案的容量保持率分別為95.23%和95.95%,說明采用變壓力化成對電池的迴圈穩定性無明顯影響。B方案電池在迴圈過程中的厚度膨脹率僅較A方案小0.24%,變化趨勢基本相同。
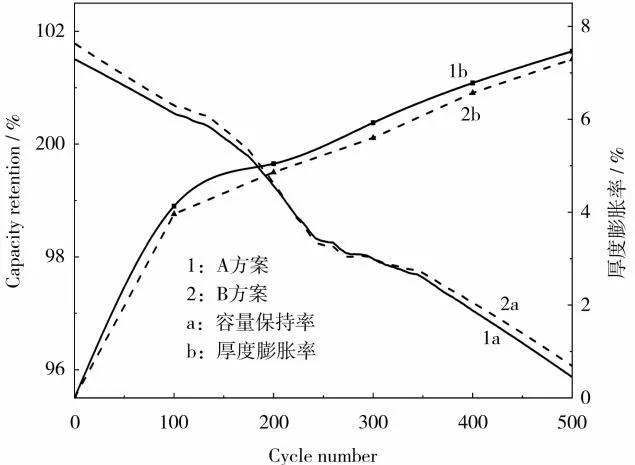
2.5 浮充測 試效能
電池在45℃下浮充測試的厚度膨脹率曲線見圖4。從圖4可知,在45℃條件下,經過84d浮充測試後,A方案與B方案電池的厚度膨脹率分別為6.28%和5.58%,說明化成大電流階段減小化成壓力,可降低電池在45℃浮充測試時的厚度膨脹率。
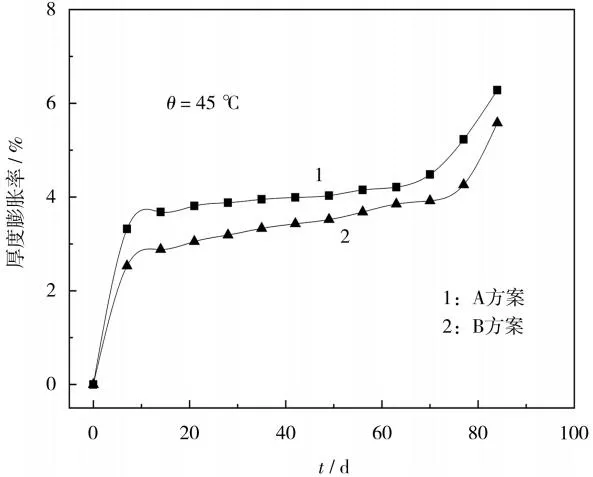
2.6 高溫儲存效能
兩種化成方案電池在60℃下高溫儲存30d的厚度膨脹率曲線見圖5。從圖5可知,在60℃高溫儲存30d,A方案電池的厚度膨脹率為2.83%,而B方案電池的厚度膨脹率為1.82%,厚度膨脹率減小1.01%。這說明,電池在化成過程60℃條件下釋放應力,厚度發生反彈,可以降低在高溫儲存時的厚度膨脹率。對於采用鋁塑封裝的軟包裝電池,由於鋁塑外殼的機械強度相對較小,對電芯束縛性弱,會降低在高溫環境下的膨脹率,能夠提高在高溫下使用的安全性。
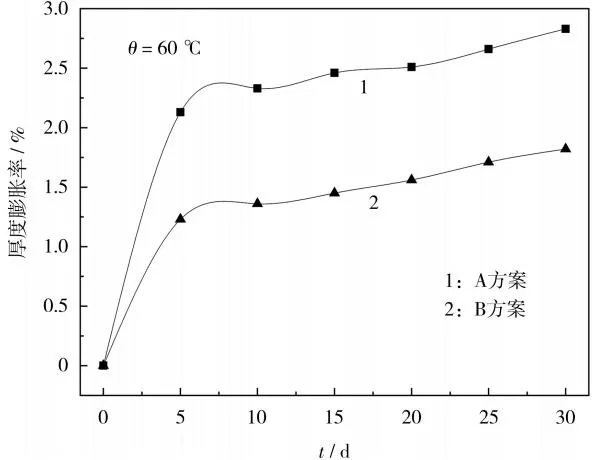
電池在60℃高溫儲存30d後的殘余容量與恢復容量數據見表3。從表3可知,A方案電池的初始容量較B方案高12mAh,原因是A方案電池的首次庫侖效率高於B方案。B方案電池的殘余容量和恢復容量均高於A方案,說明化成過程大電流時降低壓力使SEI膜的穩定性有所提高,在高溫儲存時,SEI膜的分解重組消耗的鋰更少,降低了容量損失。
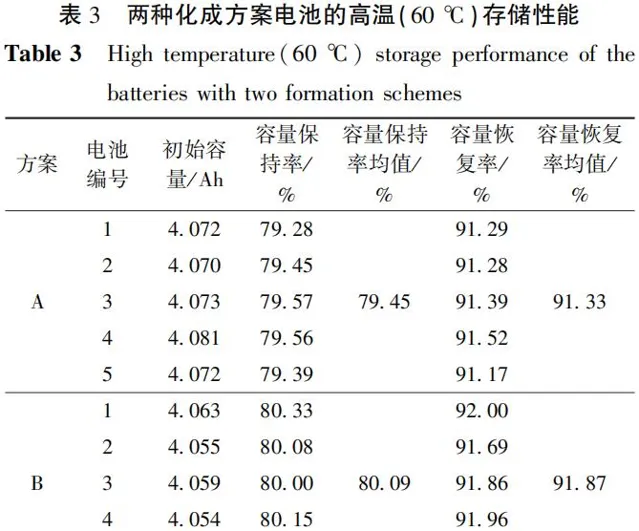
3 結論
目前,在軟包裝鋰離子電池化成過程中均采用恒定壓力進行化成,分容後電池厚度出現膨脹,導致電池厚度增加;而在化成大電流階段將化成壓力減小為小電流時的1/3,電池在化成階段釋放應力,可降低電池的最終厚度。與恒壓力化成相比,采用變壓力化成使得電池在浮充及高溫儲存時的厚度膨脹率分別降低0.70%和1.01%,提高了電池在高溫下使用的安全性。